供应链管理为何如此重要
Greif 与供应商合作,以确保我们对可持续发展的承诺不仅仅涵盖我们自己的运营。我们希望我们的供应商能够像我们一样保持同样的诚信、责任感和对可持续发展的承诺。通过积极与供应商合作,我们最大限度地降低了潜在的环境和社会风险,同时创造了有效利用材料和实施对客户产生积极影响的解决方案的机会。
治理
Greif 采购树脂、油漆和钢材等直接材料以及消耗品、服务和运输等间接材料。作为 Greif 业务系统 (GBS) 的一部分,Greif 的全球采购和供应链团队 (GSSC) 每月跟踪材料成本、营运资本、交易条款和库存的改善情况。我们在以下文件中概述了对供应商的期望 供应商行为准则 ,我们于 2021 年对其进行了更新。我们根据评分卡评估前 20 家供应商,评分卡考虑质量、交付、成本、增值服务、环境影响和技术支持。可持续性标准(例如减少材料、使用对环境影响较小的材料和供应商可持续性计划)占供应商评分卡的 5%。
Greif 遵守适用法律,以管理我们供应链中潜在的侵犯人权行为。由于某些 Greif 产品含有锡,我们致力于了解我们供应链中的 3TG 金属。为了评估整个供应链中的冲突风险,我们验证了我们的 冲突矿物政策 并发布我们的 冲突矿物报告 每年。根据 2010 年加州供应链透明度法案,Greif 采取措施防止和消除直接供应链中的强迫劳动,如我们的《供应商行为准则》和 供应链披露的透明度。
在我们的企业风险管理过程中,我们认识到供应链是一个需要谨慎管理的关键风险,因为它可能会影响我们的业务连续性或履行客户承诺的能力。我们必须能够为我们的同事和设施提供他们所需的一切,以提供卓越的客户服务并满足我们的产品质量标准。在 2020 年,保持连续的供应链对于在 COVID-19 疫情期间支持业务连续性至关重要。我们利用现有的程序、控制和流程来确保我们的设施拥有所需的所有物资,包括个人防护设备。通过与供应商合作,我们在需要时利用备用供应商和新供应商,最大限度地减少了短缺。
供应链可持续发展目标由我们的可持续采购团队提供支持,该团队评估减少材料使用的机会并寻找更可持续的原材料替代品。该团队由来自各个地区的同事组成,评估全球各地的机会,并努力与全球采购团队分享可持续采购方面的最佳实践。2018 年,我们开始用电动叉车取代可燃汽油和液化石油气驱动的叉车。这一转变既支持了 Greif 的可再生叉车政策,又显著减少了排放。到 2020 年,我们已将 EMEA 地区 99% 的叉车转换为电力驱动,同时将车队规模减少了 17%,并在 2020 年实现了 $352,000 的成本节省。在北美,我们已更换了 2% 的车队,并在 2020 年节省了 $250,000。
我们还做出了一些改变,以影响我们的卡车和同事车队的能源和排放使用。到 2020 年,我们已将 50% 的北美车队转换为太阳能 GPS 装置。在欧洲、中东和非洲地区,我们为经批准的同事车辆制定了严格的排放指南,以推广更节能的车辆,并在可行的情况下推广电动汽车。通过该计划,我们已将欧洲、中东和非洲地区 41% 的车队转换为太阳能 GPS 装置,并在 2020 年实现了 $166,000 美元的成本节省。
2020 年,我们启动了一项提高压缩空气效率的计划,这将显著减少 EMEA 地区的能源使用量。2020 年,我们还开始在全球范围内用功能更强大的设备替换旧式小型复印机。新复印机包含限制用户打印的软件,将在全球范围内减少纸张和墨粉的使用。在我们位于特拉华州的总部,新复印机在四年内减少了近 300 万张打印量。我们继续跟踪有可能通过 GBS 产生积极可持续发展影响的采购项目。2020 年,我们确定了 10 个项目,在可持续发展影响项目上节省了 $587,000 美元。
Greif 致力于在我们的产品和运营中寻找和实施化学替代品,以消除和减少危险废物,包括挥发性有机化合物 (VOC)。自 2015 年以来,我们一直致力于降低钢卷材料量和运营中潜在的危险油漆。我们现在在许多产品中使用更安全的替代品,包括我们的 Tri-Sure Vreeland 衬里和水性丙烯酸涂料。我们所有的北美工厂(佛罗里达州奥本代尔除外)都在使用水性涂料。亚太地区的五家工厂正在转向水性涂料,包括我们的珠海工厂,2020 年该工厂 70% 的涂料使用量为水性。我们为减少危险废物而采取的措施符合我们的 环境健康与安全政策。
所有新供应商均可访问我们的 供应商行为准则 通过 Greif.com 并期望遵守其中的原则。在全球范围内,我们的《供应商行为准则》是供应商必须签署的每份采购订单和协议的一部分。2020 年,我们开始将《供应商行为准则》与传统的 Caraustar 采购订单一起发送。这开始提升《供应商行为准则》以及环境、社会和治理主题对供应商和采购决策过程的重要性。
我们正在修订《供应商行为准则》,以便为我们的供应商设定更好的期望,并根据我们服务的关键行业更好地应对我们供应链中的环境和社会风险。我们将发布更新后的《供应商行为准则》作为正式政策,并开始在我们的供应商中加强执行,包括将其纳入供应商审计。2020 年,我们制定了内部采购政策,为我们的同事提供采购指南。该政策包括对环境和社会采购标准的考虑,包括绿色材料、废物和供应商多样性。我们还在美国和加拿大发布了更新后的临时劳工政策。临时劳工政策正式确定了对临时劳工代理机构提供商的额外要求,并确保遵守所有监管要求。
我们继续将环境和社会标准纳入供应商审计。为了确保供应商在同事健康和安全等领域不断改进,我们将符合标准和 ISO 认证发展的语言纳入供应商审计。我们以行业最佳实践为基准,改进我们的供应商记分卡, 供应商行为准则, 和评级程序。我们创建了有关反垄断政策和产品的法律培训,所有同事都可以通过我们的在线培训系统获得这些培训。我们正在利用 EcoVadis 评估来分析供应商的可持续发展绩效。我们从 2020 年开始要求我们最大的 40 家供应商完成 EcoVadis 评估。到目前为止,占我们供应商支出 11% 的供应商已经提交了 EcoVadis 回复,我们的目标是到 2021 年底评估 25% 的供应商支出。作为该计划的一部分,我们对 EcoVadis 进行了培训,以了解评估、识别 EcoVadis 评级的因素并充分利用评估中的信息。
2020 年,我们制定了战略路线图,详细说明了我们到 2023 年的供应链战略。作为该路线图的一部分,我们确定了与我们的主要采购工作流相关的可持续发展项目机会。根据“客户之声”项目的成果,我们还致力于让 GSSC 团队更多地参与客户服务的执行。让 GSSC 团队参与进来,使我们能够采取更积极主动的方法,改善与设施和客户的沟通,并实现额外的成本节约。
目标与进展
2017年,我们制定了2025年目标:
- 以2017财年为基准,将生产当前产品所需的原材料/物流成本降低百分之一。
- 如果经济上可行并且能够为我们的客户提供高质量的产品,则从非绿色(石油基、能源密集型)材料采购转向绿色材料采购。
到 2021 年底,我们将原材料用量减少了 0.7%,并且有望实现到 2025 年减少 1% 的目标。为了继续实现 2025 年的目标,我们在招揽潜在供应商时将目标纳入了 RFQ 流程。我们的采购经理将碳含量、可回收性和包装改进等主题纳入与许多供应商的对话中,以寻找推进目标的机会。我们已经进行了绿色材料替代,以增加产品中消费后再生塑料的使用。我们提高了瓦楞纸箱和其他包装材料的效率,以提高可重复使用性,同时优化物流路线,以减少运输费用。在一些 EMEA 工厂,我们引入了一种更易生物降解的油来清洁我们的油漆生产线。从非绿色产品和材料(如油基产品)的转变促使我们从供应商那里采购绿色材料。我们已经开始从溶剂型涂料转向水性涂料和桶衬里。我们通过内部变革(例如转向 LED 灯)来补充这项合作工作。这些举措都是与供应链团队合作的一项更大规模培训计划的一部分,旨在思考和开发新项目,并将可持续性纳入我们 13 个买家(包括钢铁、树脂和物流买家)的绩效评估中。
可持续森林管理
Greif 纸板厂已获得可持续林业倡议 (SFI®) 认证、森林管理委员会 (FSC®) 认证和森林认证认可计划 (PEFC®) 产销监管链认证。这些认证系统提供第三方认证,以跟踪和传达来自可持续管理土地的产品数量。
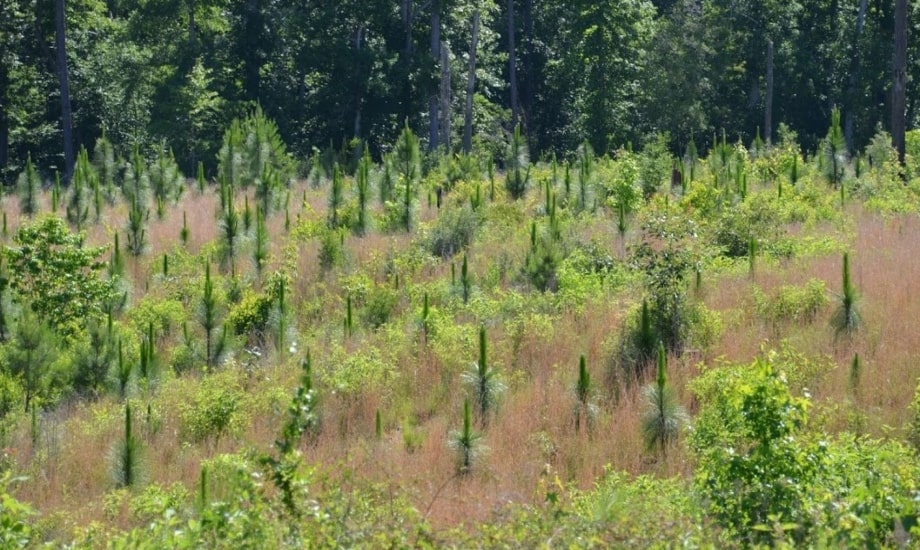
生态Vadis
2020 年,Greif 凭借出色的企业社会责任表现获得了 EcoVadis 颁发的金牌认可。这一分数使 Greif 在 EcoVadis 评估的所有供应商中位列前 3%。
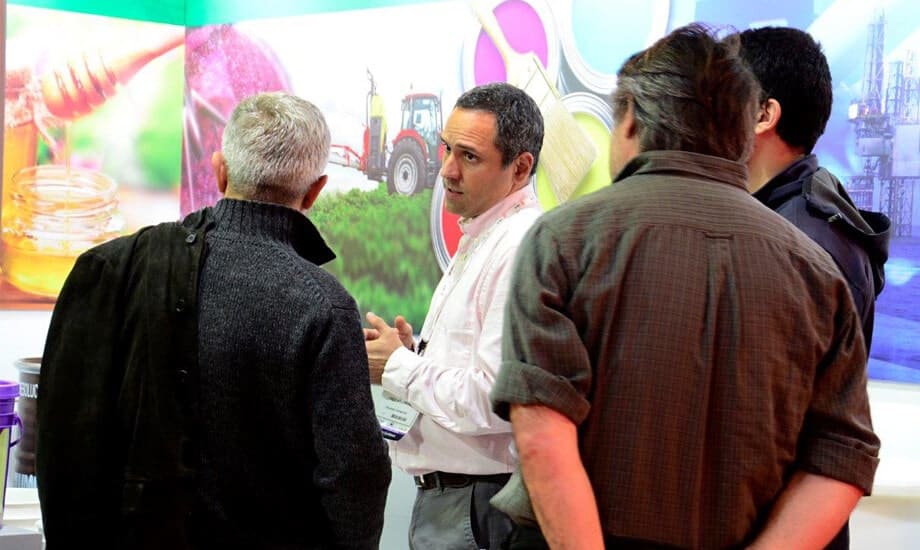
携手实现可持续发展
携手实现可持续发展
自 2014 年以来,Greif 一直与 Together For Sustainability (TfS) 合作,帮助为化学品制造商的供应商建立行业范围的可持续发展标准。TfS 代表其 20 多家化学品制造商成员,根据 30 多项管理、环境、健康和安全、劳工和人权以及治理标准对供应链合作伙伴进行审核。TfS 将结果分发给其成员以支持采购决策,从而取代了对公司特定审核的需要,并要求供应商遵守行业一致的标准。9 家 Greif 工厂接受了审核,平均得分为 93.9%,表明我们的工厂没有重大问题。2020 年,TfS 对我们位于土耳其苏丹贝利的工厂进行了审核。
TfS 审计绩效
- RIPS 伊利诺伊州内珀维尔: 100%
- 德国科隆RIPS: 98%
- 德国洛克波特RIPS公司: 98%
- 土耳其苏丹贝利FPS: 98%
- 荷兰RIPS Europoort: 97%
- 德国阿滕多恩 RIPS 电视台: 96%
- 捷克共和国乌斯季 RIPS: 95%
- 阿根廷坎帕纳的RIPS: 83%
- RIPS上海,中国: 80%
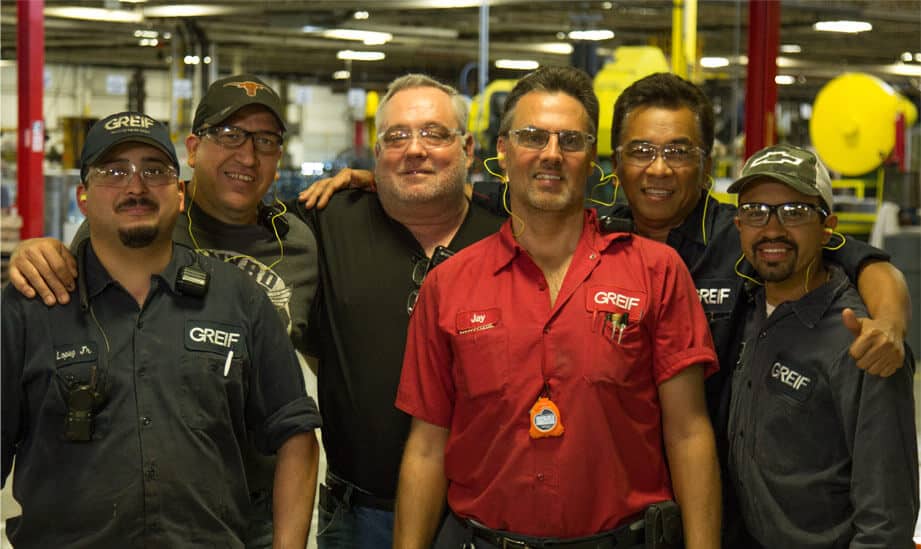
仪表改进
Greif 每月都会跟踪进货原材料的规格。我们与供应商合作,始终满足我们的最低规格,帮助我们降低物流成本,并尽量减少产品中使用的原材料(与最高规格的材料相比)。2019 年,我们通过改进规格的努力节省了 $1 百万。
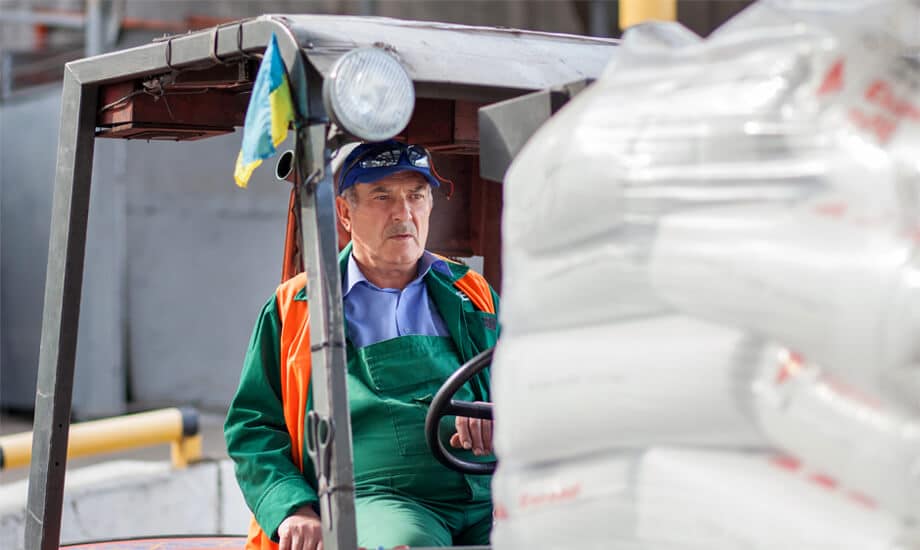