Highlights
- Greif is committed to reducing our operational waste and supporting the transition towards a circular economy. We track the percentage of waste-to-landfill by business unit as a key performance indicator (KPI) and share it in monthly facility reports with our leadership.
- We have made considerable progress in managing waste across all facilities, with 60 facilities achieving zero waste-to-landfill status in 2024.
- Greif works collaboratively with internal and external stakeholders to manage difficult-to-divert waste streams, handle as much internal recovery as possible, and identify future opportunities for reusing waste.
- Within our Industrial Products Group (IPG) facilities, we are committed to sustainable waste reclamation practices and continue to explore opportunities for managing the return of customer waste as a way to process and sell recycled materials.
- Within our Recycled Materials Group (RMG) we help collect, process, and bale recyclables at our plants to then be shipped to our paper mills and other external manufacturers.
Why Waste Matters
We set ambitious waste management goals to safeguard the future of Greif and the planet. Aligned with our Build to Last Strategy, we have adopted closed-loop and zero-waste production processes that minimize operational waste sent to landfills. Our operations generate both hazardous and non-hazardous waste, and we aim to handle as much internal waste recovery as possible while working collaboratively with internal and external stakeholders to reduce and sustainably manage waste. Our waste-management approach delivers cost-savings, mitigates risks, and promotes the well-being of our employees, the environment, and the communities in which we operate.
Greif is a circular solutions-provider. We buy waste from other industries and repurpose it to make our products. Our products are lightweight and cost-effective, and we actively pursue opportunities across our value chain to promote resource conservation and reduce raw material use. We are dedicated to advancing the circular economy and tackling global environmental waste challenges via our operations and products.
Our Approach
We engage each of our colleagues in waste reduction initiatives. In North America, engagement takes place via our colleague training programs, including waste management and reporting training, accessible via Greif University. In Latin America, monthly KPI discussions emphasize waste-to-landfill, and CorrChoice and IPG also discuss this topic during their quarterly sustainability calls to share best practices and collaborate on challenges. All colleagues interacting with hazardous waste are also trained in Greif’s environmental, health and safety policies, hazard communication program, and hazardous waste management training. This training covers safe and proper labeling, handling, storage, sorting, and transportation processes.
Working Across our Value Chain
Our suppliers are often our customers, giving us an opportunity to make a meaningful impact across a circular value chain. For example, steel plant customers return their cardboard to our plants so that we can either reuse or bail-and-ship them to our Greif mills. We also help suppliers with their waste and create products that we sell to customers.
In 2024, across multiple locations in North America, we worked with our suppliers to reduce the amount of packaging used to transport the materials we purchase. For example, metal lock rings were packaged in large wooden cages weighing approximately 80 pounds each that were often being landfilled. By partnering with the supplier, we now receive the lock rings on foldable, reusable containers that the supplier collects to reuse for later shipments.
Our Life Cycle Services (LCS) division takes containers and reconditions them for reuse, rather than sending them to a landfill. In 2024, our LCS network collected 3.6 million containers, reconditioned or remanufactured more than 2.6 million of these containers and recycled the remaining containers. More information can be found in our Circular Manufacturing section of this report.
To effectively manage waste streams and meet our 2025 waste diversion target, we use waste diversion roadmaps. These roadmaps provide understanding and guidance to optimize waste management at our facilities not yet achieving our 90 percent landfill diversion goal. Roadmaps are informed by waste stream matrices that identify waste management processes and provide essential insights into difficult-to-divert waste streams. Greif’s subject matter experts review this information in collaboration with facility managers and partners to develop facility-specific waste diversion processes. The roadmaps are essential for driving continuous improvement and are key to achieving our 2030 goals. We are working to improve our waste stream matrix and plan to update our facility waste reduction/diversion roadmaps in the future. These roadmaps are housed in our Compliance Management System (CMS), providing streamlined tracking and accessibility. We are also working to implement a One Greif Best in Class program that includes waste-to-landfill as a metric to be tracked in each production facility to accelerate our zero waste-to-landfill aspirations.
Paper Mills
Our paper mills recover other people’s waste, primarily running on recycled fibers from cities throughout the U.S. We also send cardboard from legacy GIP sites in North America as recyclables back to our mills. This recycled waste is often contaminated with plastic and other materials. To help suppliers reduce contamination, Greif’s Recycled Materials Group is exploring ways to implement quality processes and technologies that help with sorting recycled paper and extracting as much reusable pulp as possible. By tackling this problem on the front-end, we increase efficiencies and optimize the amount of recycled material being used throughout the paper mill process.
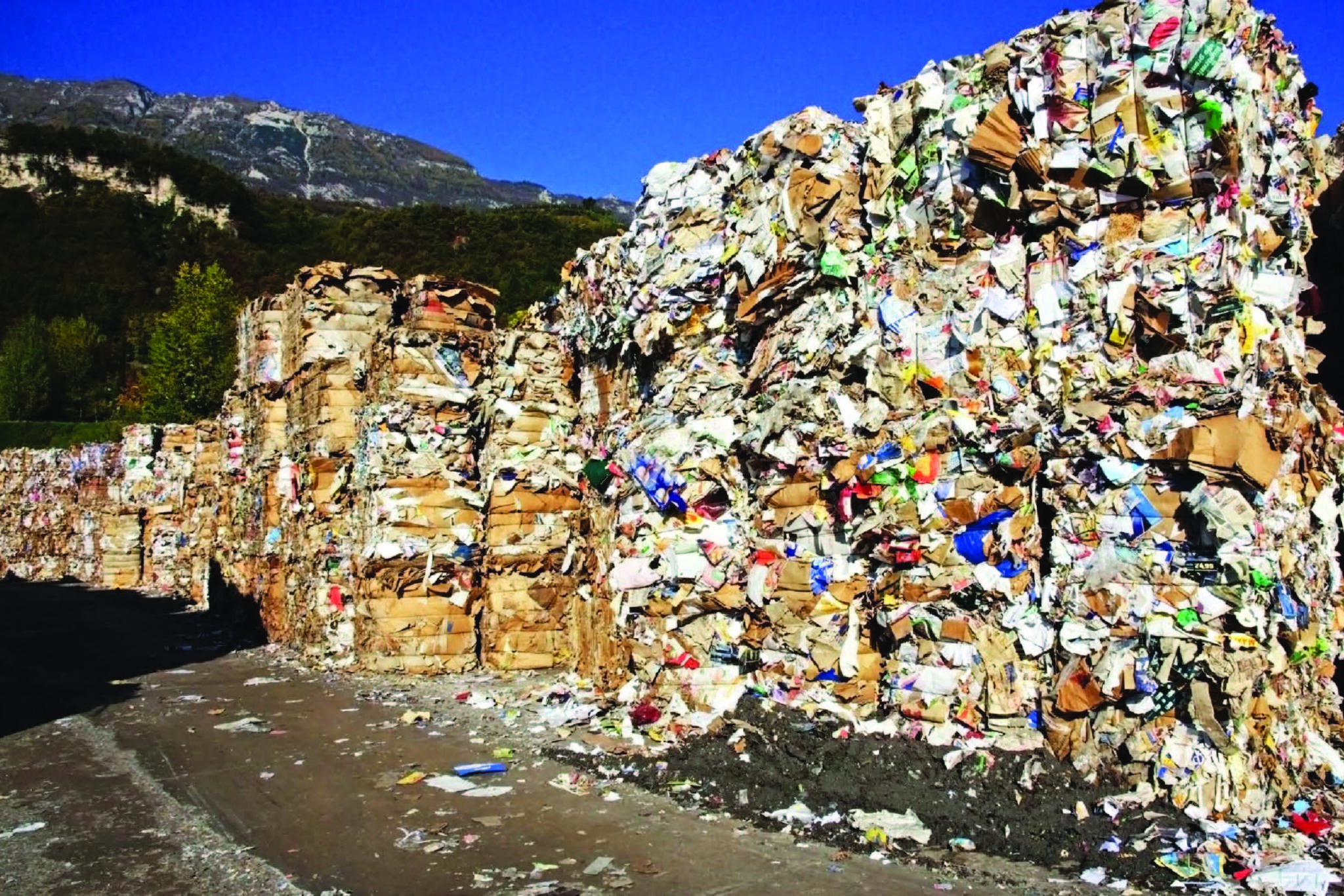
Goals, Progress, & Performance
2025 Goal:
- Divert 90 percent of waste from landfills from all legacy Greif production facilities globally by the end of FY25.
2030 Goal:
- Reach zero waste-to-landfill at 97 percent of our production facilities.
We strive to continue enhancing collaboration across business units and improving waste management performance within our operations. Our regular waste audits keep us informed about waste streams at our sites and enable us to explore options for diverting waste from landfills. We aim to reduce and reuse waste internally, drive innovation, and solve the global waste problem as One Greif.
Our commitment to waste management has enabled us to make significant progress toward achieving our waste diversion goals. All our Latin America, Europe, Middle East and Africa, and Asia Pacific facilities have achieved our 2025 goal ahead of schedule. In North America, almost all legacy Greif sites are meeting our diversion target, and our Waste Diversion Team is focusing its efforts on supporting sites not yet meeting these targets. In 2024, 60 facilities globally achieved zero waste-to-landfill, and an additional 112 facilities achieved 90 percent diversion. Further, we diverted 87 percent of all waste from landfill.
We track our waste management efforts through our Compliance Management System (CMS), which facilitates accurate data collection, performance monitoring, and progress tracking. Facilities report waste data through the CMS monthly, while data governance controls and third-party assurance confirm our data’s integrity. This data feeds into our waste metrics, allowing us to track progress year-over-year. In 2024, we saw a 16 percent increase in the number of facilities meeting our enterprise waste KPI target (90 percent landfill diversion), tracked via Greif Business System 2.0 (GBS 2.0) Must Win Battle scorecard. We are refining our approach to waste data management to gather insights and drive ongoing improvement.
Greif Facilities Progress toward Waste Diversion Goals
FY 20241,2 |
Facilities not yet Meeting 90% Diversion Goal | Facilities With 90%–95% Diversion | Facilities With 95%–99.5% Diversion | Facilities With Zero Waste to Landfill (99.5%+ Diversion) |
---|---|---|---|---|
Total | 22 | 29 | 83 | 60 |
North America | 22 | 28 | 50 | 21 |
Europe | 0 | 0 | 22 | 26 |
Latin America | 0 | 1 | 10 | 4 |
Asia Pacific | 0 | 0 | 1 | 9 |
Greif Houston Facility
The Greif facility in Houston saw marked improvement in its ability to divert waste from landfill during 2021. The facility installed a de-chimer, a device designed to safely and efficiently remove the metal chimes which are used to secure the top and bottom of fiber drums. Once the chimes are removed, the fiber and metal can be directed to separate waste streams for recycling. Since the de-chimer’s installation in July 2021, the facility has diverted more than 90 percent of its waste from landfills. The facility sends the fiber to our PPS Recycling Group, further reducing the waste disposal cost.
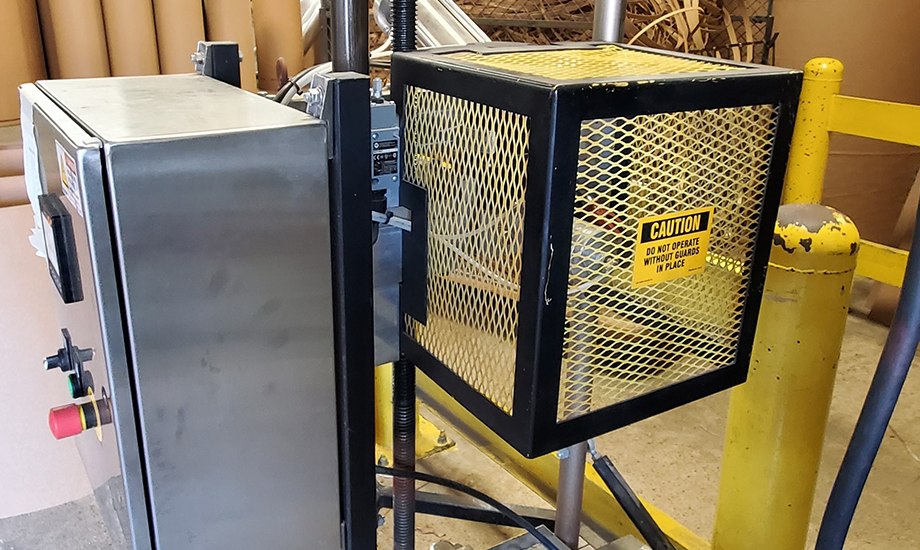
Reducing VOC’s Through Use of Water-Based Exterior Paints
Greif is committed to using water-based exterior paints in our operations where possible, rather than high volatile organic compound (VOC) exterior paints. In Global Industrial Packaging (GIP) North America, eight of our nine steel plants use water-based paints. In our Asia Pacific (APAC) facilities, there’s ongoing transition to water-based paints, which includes our facilities in Zhuhai, Shanghai and Taicang, with 81 percent, 84 percent and 41 percent, respectively, of their paint usage being water-based in 2023. In EMEA, the Czech Republic, Belgium, Germany, Hungary, Israel, Italy, Portugal, Saudi Arabia, the UK, and Poland use water-based paints alongside solvent-based paints.
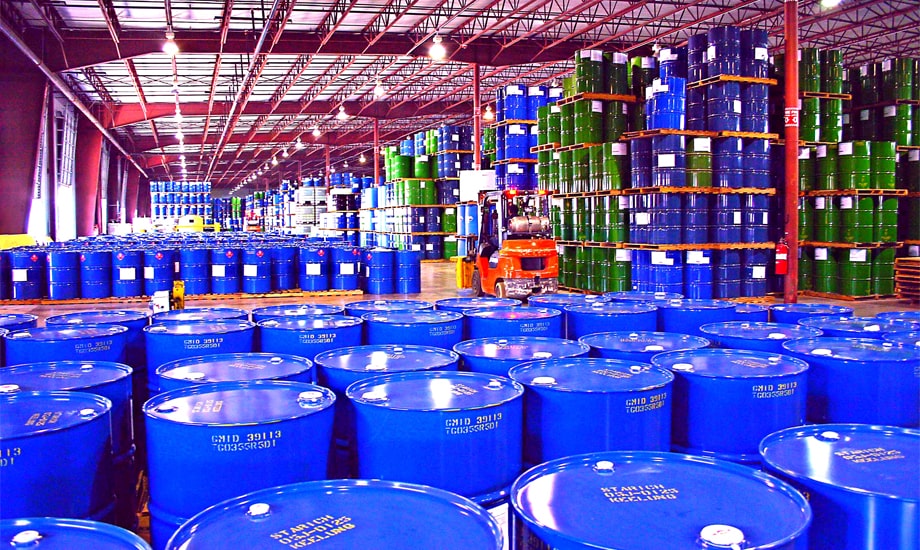