Highlights
- We ensure compliance with applicable environmental laws and regulations with the use of our Environmental Management Systems (EMS), which allow us to maintain business continuity and retain appropriate permits and operating licenses.
- Guided by consistent environmental management system principles, our Environmental, Health and Safety (EHS) Team oversees the implementation of various tools and processes to manage geographic- and business-specific needs.
- We provide annually updated training covering the critical aspects of our environmental management system, making additional updates when the regulatory landscape changes.
- Greif strives for zero instances of non-compliance at our sites and measures performance based on the results of regulatory compliance inspections.
Why Environmental Management Systems Matter
Greif’s operational success relies on our strict adherence to environmental laws and regulations relevant to our business. Our EMS are instrumental in maintaining compliance. By leveraging our in-depth knowledge of the intricate regulatory landscape and adopting a proactive stance, we ensure ongoing adherence. We regularly engage with regulators to proficiently address and manage environmental impacts. Failing to uphold these systems would impede our ability to achieve the Protecting our Future mission of our Build to Last Strategy.
Governance
Greif’s proprietary Compliance Management System (CMS) is how we diligently monitor and ensure adherence to relevant laws and regulations. This includes thorough oversight of environmental compliance, covering aspects such as facility emissions, energy consumption, water usage, waste management, trainings completed, incident tracking, compliance tasks, safety audits and actions and more. Our CMS serves as the central hub for creating, storing and regularly reviewing facility compliance roadmaps. CMS administration is guided by our EHS Team, under the leadership of the Senior Vice President, Global Operations Group. This team actively oversees compliance and is supported by other key positions such as the Global EHS Manager, Senior Environmental Manager, Environmental Specialists, Environmental Engineers, EHS Director and regional managers overseeing Greif’s four regions. In alignment with our One Greif approach, we integrated the EHS Teams for Global Industrial Packaging (GIP) and Paper Packaging and Services (PPS) into our Global Operations Group. This strategic realignment has not only enhanced operational efficiency, but also fostered collaborative efforts across our global business landscape.
The inherent environmental and safety impacts of our global manufacturing operations require that we are diligent about compliance with numerous EHS regulations. Across our organization, we employ a variety of tools and processes tailored to specific geographic and business needs. Guided by consistent principles, our global EMS undergo regular audits by internal and external parties to verify strict compliance with all regulations at our facilities.
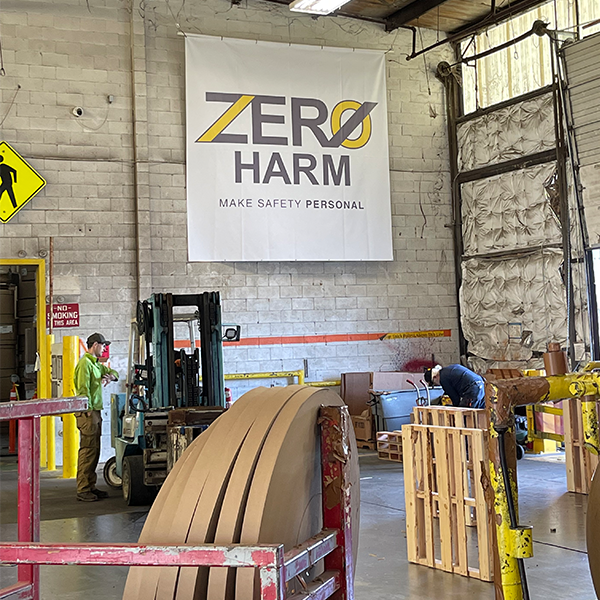
EMS Training
Our EHS Team provides colleagues with regular training throughout the year. Our EHS Team directed compliance trainings events at approximately 163 global GIP and PPS sites in 2023. These compliance training events include:
- Universal Waste Annual Refresher Training
- Spill Prevention, Control, and Countermeasure Annual Refresher Training
- Hazardous Waste and Emergency Refresher Training
- U.S. Department of Transportation Hazmat Shipping 3-year training
- Asbestos Awareness Program Refresher Training
- Annual Resource Conservation and Recovery Act Hazardous Waste Refresher Training
- Landfill Solid Waste Annual Refresher Training
- Air Permit and Emissions Monitoring Training
- Opacity Training
- Stormwater Annual Refresher Training
- Noise Reduction Training
- Dust and Particle Control Training
- Industrial Stormwater Permit Training
- Emission Capture Training
- Legal Requirement Training
In North America, Greif facilitates elevated compliance management through Dakota, an advanced EHS compliance and risk management software. Dakota tracks new regulations tailored to each facility’s unique profile. Greif reinforces these efforts with internal and third-party audits, pinpointing facility-specific tasks to enhance environmental risk management. Looking ahead, we plan to globally consolidate localized EMS in the coming year.
Regular internal audits remain a cornerstone for the GIP and PPS businesses. Notably, in 2023, audit simulations were internally piloted at five sites, complementing the frequent desktop audits conducted internally. Third-party audits are planned to proceed in 2024.
The EHS team ensures compliance with air permits at all facilities, providing regular training to colleagues on particulate matter, odor, noise and other air pollutants. Greif aims to minimize hazardous emissions, such as volatile organic compounds, through a variety of programs such as implementing chemical substitutions, using carbon filters, installing permanent total enclosures, installing a water scrubber system with bacterial regeneration, and changing from solvent-based to water-based coatings. CMS is employed to develop and track relevant tasks, while emissions data monitoring is facilitated through systems like SBP, Progea and Resource Advisor. Initiatives include regenerative thermal oxidizers inspections, industrial hygiene surveys, source testing and the use of engineering technologies for filtering or reducing emissions, supported by routine preventative maintenance.
In 2022, we unveiled a global, internal tool dedicated to assessing environmental risks. This tool emerged from a comprehensive risk assessment covering 100 percent of North American sites, distinct from the Europe Middle East, Asia Pacific and Latin America regional assessments, which also occurred in 2022 for 100 percent of those facilities. As we developed and defined the tool, we optimized its capabilities in risk assessment, calibration and standardization. Since its launch, the tool has proven invaluable in evaluating sites with significant environmental risks, enabling us to promptly implement essential corrective actions. Based on risk results, each facility is required to have a contingency plan and emergency procedure in place to minimize the potential for injury, property damage, environmental release, and interruption of business.
In 2023, we continued using our New Chemical Request and Equipment Pre-Acceptance Review processes. When a facility aims to acquire or process a new chemical product, we initiate a comprehensive safety and environmental review process, subject to corporate scrutiny. Our corporate environmental engineer leads the environmental assessment, while the regional EHS manager conducts the safety review. Following this, the director of EHS and senior environmental manager review the results. Upon approval, we begin the onboarding process for the chemical. This approach enables us to effectively address both the actual and potential impacts of hazardous chemicals. At our PPS mill locations, securing pre-approval for all additive substances is a mandatory requirement. Additionally, in 2023, we incorporated a per- and polyfluoroalkyl substances (PFAS) statement into the review process, requiring vendors to commit to refraining from PFAS use.
In our PPS business, our project development checklist is used whenever a mill embarks on a new capital project. The project manager completes an environmental checklist form, disclosing the project’s impacts, regardless of anticipated severity. The checklist encompasses factors such as compliance, changes in emissions and wastewater management. Our EHS professionals thoroughly review the list to affirm the project’s readiness to proceed. The checklist’s implementation affirms that all new equipment complies with our environmental, quality, health and safety standards before obtaining approval for purchase and installation.
In our GIP business in both North America and Europe Middle East, our proactive Management of Change process continued in 2023, encompassing a total of 186 reviews. We also completed and uploaded environmental checklists for all our Title 5 facilities. Within our PPS business, we executed 229 new Chemical Requests in North America, and 343 globally.
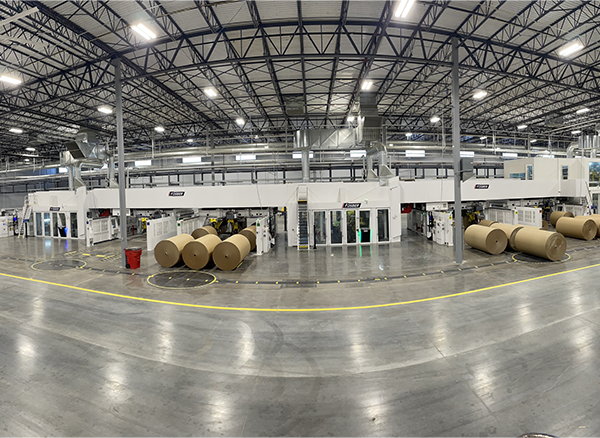
Our Third-Party Certifications
Our production facilities manage quality, safety and environmental standards through certifications such as OHSAS, ISO, FSSC and SQF. Our Paper Packaging and Services operations maintain ABI, FSC, OSHA, PEFC®, SFI®, RPA 100 and RPTA FDA certifications. All our CorrChoice facilities and most mills have SFI® Chain of Custody Certification, and all our mills are certified to FSC® (FSC® C003539) and PEFC® Chain of Custody standards. Most mills have obtained RPA100 certification. Throughout our operations, 11 sites have achieved ISO 14001 certification, and two more achieved ISO 50001 certification. Please visit our 2024 Certificates document to learn more about our facility certifications.
Goals, Progress & Performance
Greif is committed to maintaining a zero-tolerance approach to non-compliance. When we identify instances of non-compliance, we swiftly address and rectify the situation.
Regenerative Thermal Oxidizers
In 2022, Greif implemented a maintenance program to advance the longevity of our regenerative thermal oxidizers (RTOs) that control volatile organic carbon (VOC) emissions at 10 of our GIPNA sites across North America. Continuing our shift to a corporate-driven management system, we work with a third-party partner to manage the recently implemented devices. Our third-party partners assist us in assuring that our RTOs are maintained in compliance with all relevant regulations and in avoiding or solving any maintenance-related issues. We hold quarterly, semi-annual- and annual maintenance evaluations and track this program within our CMS. We continue to install new RTOs at our facilities and anticipate leveraging the program at all applicable facilities, leading to improved efficiency and reduced emissions.
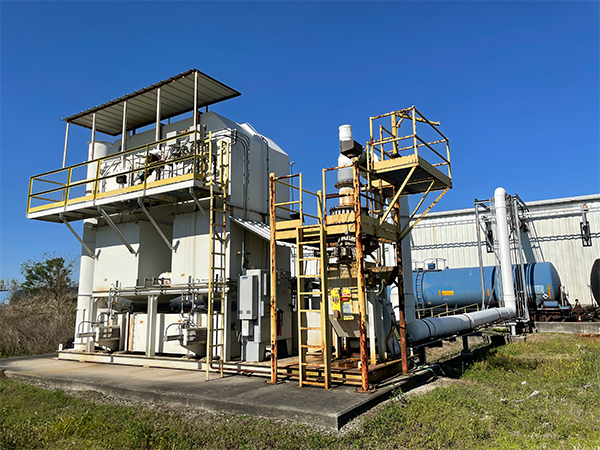