- Sustainability at Greif
- Estratégias de Sustentabilidade
- Metas e Desempenho
- Índices de relatórios ESG
- Relatório de downloads
Destaques
- At Greif, we believe that an engaged workforce is a safer workforce. Our safety ethos is built on fostering active participation at all levels by empowering employees to take ownership of workplace safety through strong safety committees and comprehensive safety programs.
- In 2024, we welcomed a new Senior Director for Environmental, Health, and Safety (EHS) in the Americas, who has been visiting facilities across the region to gain on-the-ground insights. This hands-on leadership approach reflects our belief that health and safety are collective responsibilities, requiring teamwork and commitment from leadership to frontline workers.
- Zero Harm is Greif’s commitment to safety within our Build to Last Strategy. It represents our unwavering commitment to ensuring every colleague leaves work as safe and healthy as when they arrived. Through our Commitment-Based Safety/Quality (CBS/Q) program, we emphasize personal accountability for safety at all levels of the organization. With a top-down and bottom-up approach, we are dedicated to protecting Greif’s most valuable asset: our people.
- We worked on aligning our health and safety initiatives across global business units to harmonize efforts and elevate safety practices across all operations.
Por que a saúde e a segurança são importantes
Safety is fundamental to our strategic mission to Create Thriving Communities by achieving Zero Harm. We strive to provide workplaces that support our colleagues’ health and safety, ensuring physical safety while creating a culture of mental and emotional well-being. We implement health and safety programs, comprehensive training, and proactive initiatives, and we raise awareness about preventing injuries and addressing close-call scenarios. By embedding safety into our workplace culture and focusing on continuous improvement, we aim to create a workplace that supports every colleague’s well-being. Our goal is to maintain Zero Harm so that everyone returns home as safe and healthy as when they arrived.
Our Approach
At Greif, creating a safe workplace is a shared responsibility across everyone at our company. The Global Operations Group (GOG), which is comprised of our Safety Leadership Team and representatives from each region, is responsible for implementing a culture of safety through global policies. The GOG also has oversight for the continuous improvement and compliance of our safety programs across all regions.
With our recent core business reorganization, we anticipate greater global integration of our health and safety management efforts. The updated governance structure streamlines safety communications and improvements, allowing for more effective and timely actions across our business. This enhanced integration is evident in the close collaboration between our Engineering and Health and Safety teams who integrate safety criteria into our Equipment Pre-Acceptance Review process (EPAR). Before new equipment arrives on site, we conduct visits to the equipment manufacturers to verify that our safety standards are met while the equipment is being produced. By applying a comprehensive set of health and safety standards from procurement through operations, we ensure that all equipment meets our safety requirements before being deployed.
Our EHS activities are built upon three pillars: skilled people; management systems; and design and technology. These are the foundational tools used to manufacture, market, and distribute our products globally in a manner that protects employees, neighbors, customers, and the environment. All our operations implement health and safety policies and programs that are aligned with our global EHS policies. We also employ a Política de Segurança do Contratante, which provides safety standards for our contractors, in addition to our other global policies which apply to all union and non-union colleagues in our workforce. We are committed to protecting everyone who works on our sites or does work on our behalf.
In 2024, our focus for global safety efforts was on alignment—bringing our safety programs together across all regions. We analyzed our health and safety data, gaining insights from key metrics from all our regions and identifying how to unify our safety approach. Our goal is to create consistent, effective safety programs that resonate across our diverse global operations. The GOG played a pivotal role in guiding these data-driven initiatives. As we carry out this work, our safety efforts have been supported by cross-functional team collaboration.
Semana da Segurança Greif
Greif held our annual Safety Week in May of 2024, which included participation from the Executive Leadership Team and external speakers with over 7.5 hours of available presentations to join. Colleagues immersed themselves in practical exercises spanning facility, office, and remote working scenarios. Throughout the week, we deepened colleagues’ understanding of safety fundamentals, facilitated the exchange of best practices, and strengthened our approach to safety leadership. In addition to health and safety at work, Safety Week emphasized safety at home, providing colleagues a Safety Care Package with activities to share our Zero Harm mindset with family members at home. In December 2024, we held our Safety Leadership Conference—attended by top Greif leaders—where we reinforced the importance of a safety culture dedicated to Zero Harm.
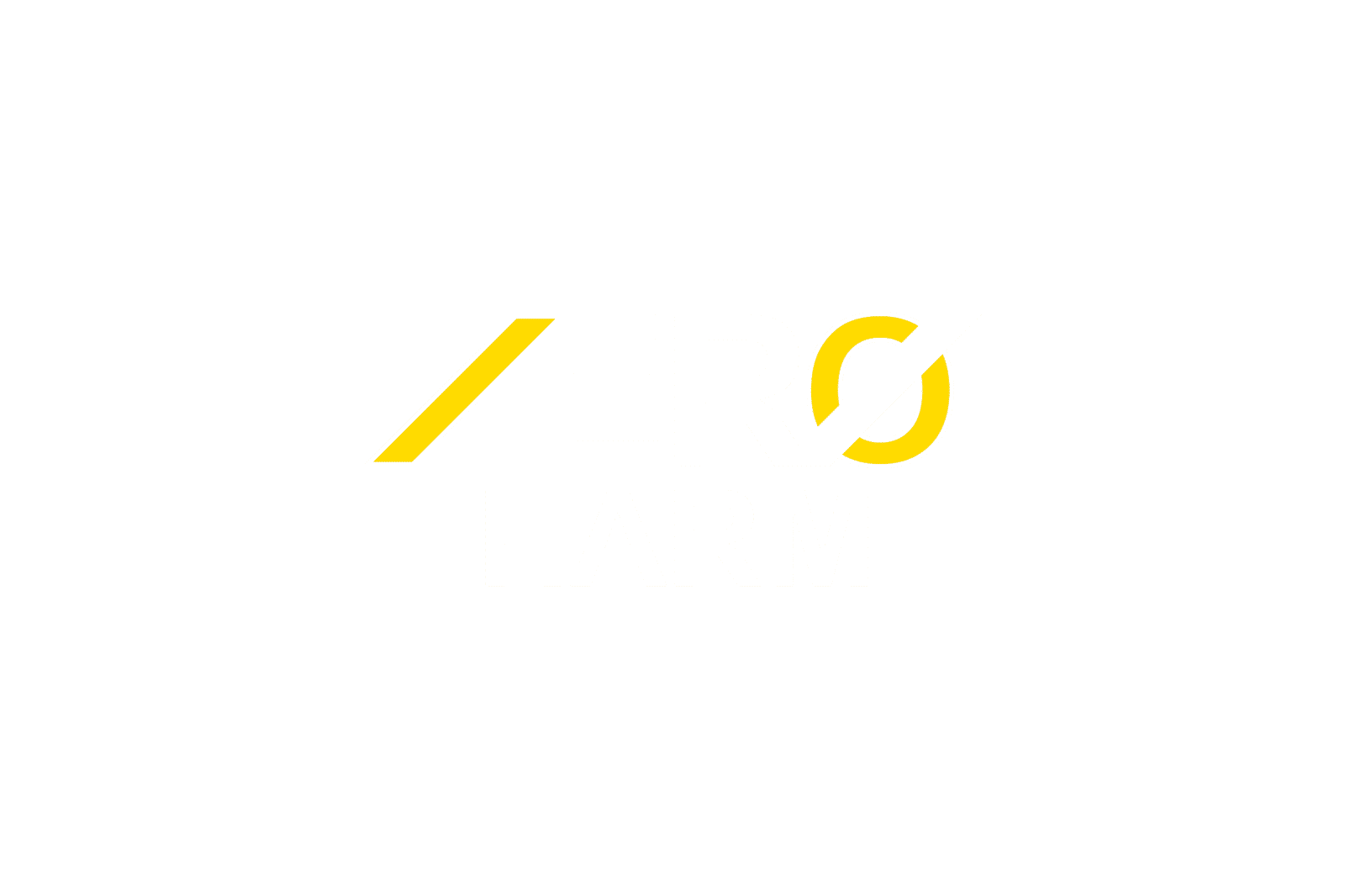
Auditing plays a critical role in verifying that our colleagues and operations are upholding the policies and guidelines we have established to create a safe workplace. We utilize our Safety Audit system in Greif QS to log and track the status of third-party audits. We conduct third-party audits on a rolling basis at each facility to verify compliance with applicable laws, regulations and policies. In addition, our industrial hygiene audit program addresses health risks associated with chemical, biological, and physical agents, including noise, vibration, heat, and radiation. These specialized audits are conducted at least every three years, or whenever workplace changes occur that alter exposure potential. One hundred percent of Greif facilities are assessed for risk every year and then audited within each three-year audit-cycle. In 2024, 49 facilities were audited within our North America (NA) and Latin America (LATAM) regions, whereas in 2023, 62 facilities were audited across all regions. While these audits are vital for meeting compliance requirements, they also serve as a valuable tool for continuous improvement. The audit scores inform our LIFE program risk areas, safety management systems, and standardized performance measurement.
Through Greif’s Compliance Management System (CMS), we track audit results and develop corrective actions to address any identified issues. The CMS provides real-time updates on auditor feedback and creates a dashboard of safety KPIs aligned with recommended tasks. Colleagues can easily view and address corrective actions related to any audit findings, while more complex issues require colleagues to conduct a full root-cause investigation. Our internal reporting process includes daily reports to CMS users and weekly and monthly updates to EHS Directors. We publish our “Target Zero” quarterly newsletter to communicate safety-related news and highlights from our facilities worldwide to all Greif colleagues.
Greif’s LIFE program identifies risks, close calls, first aids, medicals, and other incidents (such as property damage) that could lead to life-altering events. LIFE oversees risks associated with nearly a dozen risk categories including hazmat, fire or explosion, electrical exposure, lockout/tagout, machine guarding, forklift safety, and other high-risk scenarios and includes training specific to these types of risks. Our LIFE program is also a key instrument for monitoring, tracking, and preventing workplace incidents, with reported incidents now reviewed during monthly calls with our Global Industrial Packaging (GIP) function. This process advances root-cause investigations and provides senior leadership visibility and follow-up on key safety issues.
By analyzing our safety metrics and audit results, we can make informed business decisions and focus on the areas that will have the greatest impact on the health and safety of our colleagues. We review key safety metrics and prioritize our actions based on data-driven insights. In 2024, we identified two critical focus areas, Lockout/Tagout/Tryout (LO/TO/TO) procedures and machine guarding. To address these, we revamped our LO/TO/TO training program, standardizing the process of machine safety during repair and routine maintenance and applying the process globally. Similarly, we developed a standardized machine guarding program, which eliminates inconsistency in safe machine operation and establishes a clear global standard for machine safety.
Leadership training also emerged as a critical area for improvement. We began enhancing leadership training programs to support our safety goals in 2024. Looking ahead to 2025, we plan to expand our virtual health and safety training for plant leaders and other members of our leadership team, aiming to strengthen their safety expertise so they can drive safety excellence within their teams.
Greif empowers every colleague with stop work authority and the right to speak up when unsafe conditions are present, without fear or repercussions. Our TAKE2 program enables colleagues to take two minutes to analyze the process, personal actions, equipment, and potential hazards before performing non-routine tasks. Our CBS/Q program reiterates that colleagues must be attentive to situations that pose a safety risk to themselves or others. Each team is responsible for identifying potential safety hazards within their job function. In the event of an incident, Greif maintains a colleague hotline to elevate and report cases that cannot be resolved locally. Additionally, our North America colleagues have access to a direct medical support hotline service that streamlines our colleagues’ access to medical care and guidance.
Goals, Progress, & Performance
Metas para 2025:
- Reduce medical case rate (MCR) by 10 percent annually to achieve our long-term target of 100 percent safety with an MCR of zero. Our revised goal is to achieve a MCR below 1.5 in 2025.
- Cada fábrica terá um Comitê de EHS colaborativo composto por gerentes e trabalhadores até o final do ano fiscal de 2024.
100
Greif facilities achieved a zero MCR in 2024
Implementing a strong training program helps us create a safe workplace culture. We offer our health and safety training in approximately 20 languages to increase accessibility to as many colleagues as possible. Our leadership training equips leaders with the knowledge and resources to manage safety practices, address safety issues, stay vigilant to risks, and facilitate meaningful conversations through our CBS/Q discussions that occur at the start of every work shift. Looking ahead, we plan to enhance and expand our virtual health and safety training for plant leaders and other members of our leadership team, further developing their safety expertise to drive safety excellence within their teams.
We focused our efforts on facilities with higher safety risk, refining our facility safety plans, and reinforcing goals and actions tailored to address the most significant safety risks at each facility. We share lessons learned from these efforts, resulting solutions, and improvements across our other facilities. Greif’s Focus Facility Program helps to identify sites around the world that are facing safety challenges. Once identified, we assess the site and support local management teams to develop their own action plans based on feedback from Point of Contact colleagues and observations. Regular follow-ups are held so the necessary resources and support are provided for successful implementation.
Since 2007, we have experienced a 52 percent reduction in MCR, improving from 3.48 to 1.67 in 2024. This is a slight decrease over the previous year’s MCR of 1.75. Since 2011, the Lost Workday Case Rate (LWCR) has improved from 1.3 to 0.89, a 31.5 percent overall reduction.
While the total number of medical and non-medical LIFE events was 175 in 2023 and 174 in 2024, we had a notable reduction in our severity rate, a measure of the number of lost work days per hours worked. Our severity rate dropped from 0.35 in 2023 to 0.18 in 2024.
We introduced a new balanced scorecard to our health and safety roadmap. Our global EHS team colleagues meet regularly to discuss our three-year health and safety roadmap and connect on team development and relationship building.
SAÚDE E SEGURANÇA DOS COLEGAS
Programa de Assistência ao Empregado (EAP)
Todos os colegas da Greif no Canadá e nos Estados Unidos têm acesso a um programa de assistência ao funcionário (EAP). O EAP da Greif é um programa confidencial de intervenção baseado no trabalho que oferece aos colegas e suas famílias serviços informativos projetados para melhorar o bem-estar emocional, mental e psicológico geral. O programa fornece intervenções preventivas e proativas para a detecção precoce, identificação e/ou resolução de problemas pessoais e de trabalho que podem afetar negativamente o desempenho e o bem-estar. Esses problemas e questões podem incluir, mas não estão limitados a, relacionamentos, saúde, trauma, abuso de substâncias, jogos de azar e outros vícios, problemas financeiros, depressão, transtornos de ansiedade, transtornos psiquiátricos, problemas de comunicação e enfrentamento de mudanças.
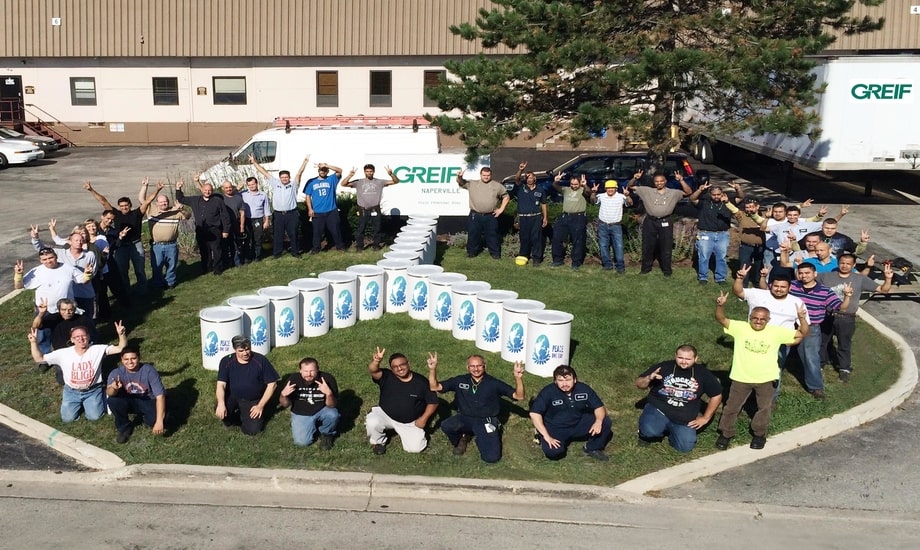
Comemorando operações sem acidentes de longo prazo
A aspiração de saúde e segurança de longo prazo da Greif é atingir zero acidentes em todas as nossas instalações no mundo todo. Embora reconheçamos o desafio dessa aspiração, 10 de nossas instalações da Global Industrial Packaging (GIP), incluindo os seguintes locais, atingiram dez ou mais anos de operações sem acidentes:
- 17 years – Amatitlan
- 16 years – Beloyarsky
- 16 years - Kazan
- 16 years – Midland Warehouse
- 16 years – Omsk
- 15 years – Mandra
- 14 years – Mombasa
- 14 years – Rio de Janeiro
- 14 years – Volgograd
- 14 years – Vologda
- 13 years – Huizhou
- 13 years – Vung Tau
- 12 years – San Juan
- 11 years – Almasfüzitö
- 11 years – Mobeni
- 11 years – Riyadh
- 11 years – TS Vreeland
- 10 years – Casablanca
- 10 years – Petaling Jaya
- 10 years – Sadat City
Essas conquistas, assim como outras instalações com zero acidentes em 2023, fornecem modelos sólidos em apoio à nossa aspiração de zero acidentes em todas as nossas instalações no mundo todo.
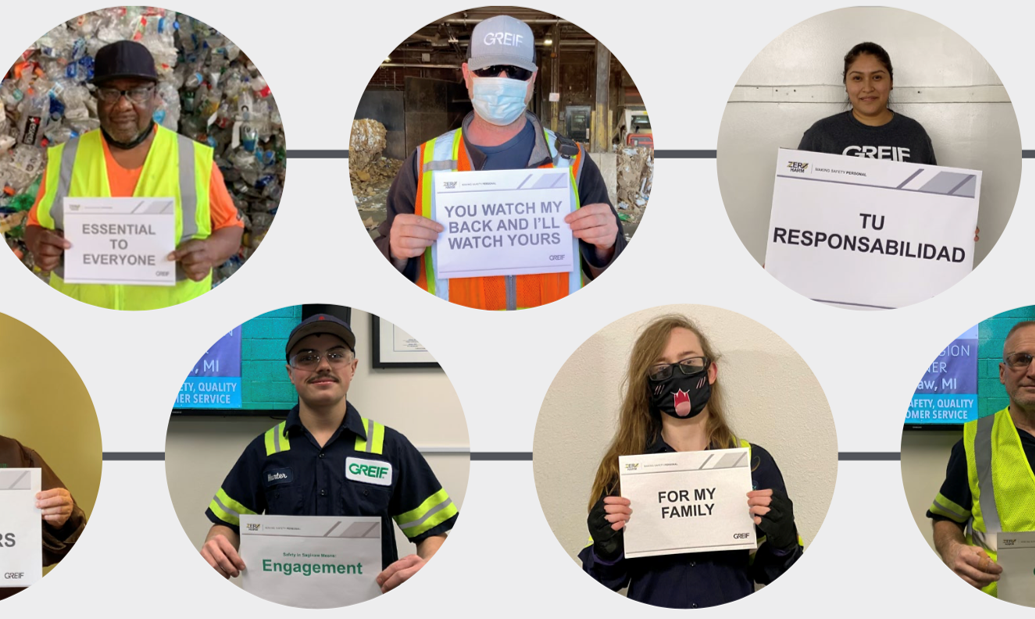
Prêmio de Excelência em Segurança do Presidente
Each facility that achieves an MCR of zero wins the Chairman’s Safety Excellence Award. Globally, 100 of our production facilities received the award in 2024 and were recognized at a virtual ceremony. We also recognized one facility from each of our 7 strategic business units with the Safety Pioneer Award for the first time. The Safety Pioneer Award is given to recognize impactful environmental, health, and safety improvements and innovations.
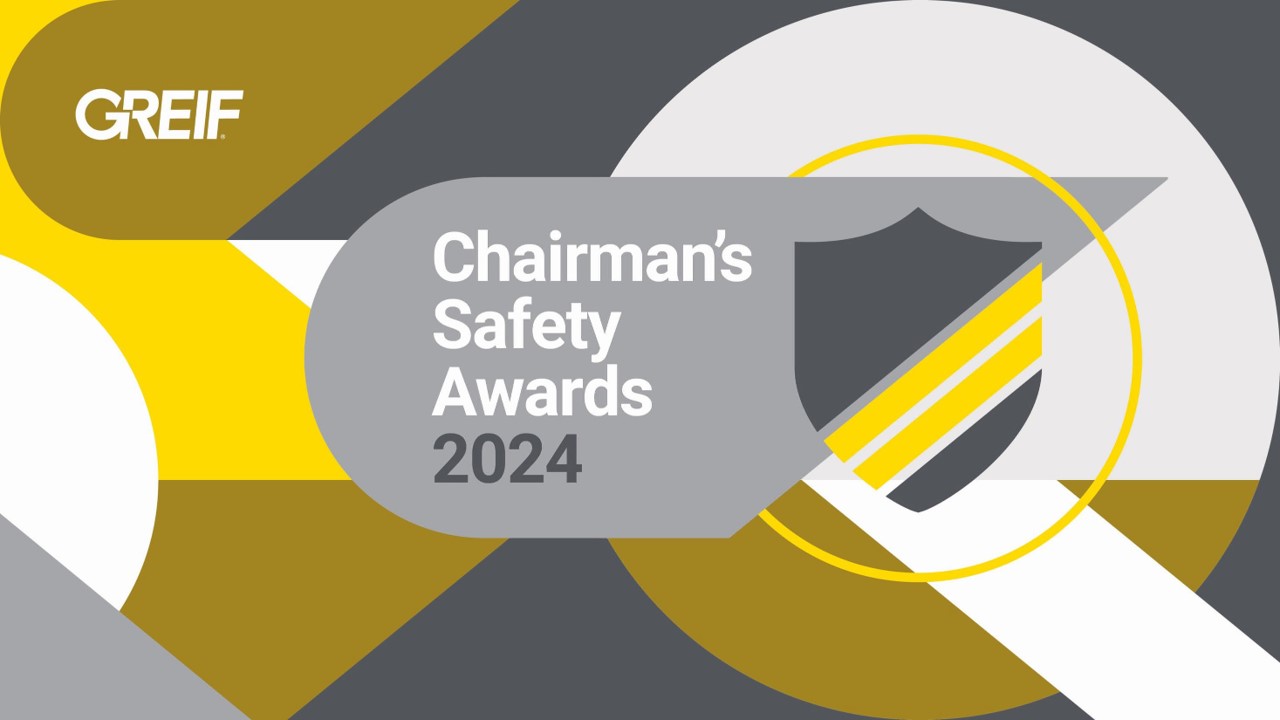