פַּסִים
- Our environmental management systems enable compliance with environmental laws and regulations, allowing us to maintain appropriate permits and operating licenses.
- Greif uses various tools and processes to manage geographic- and business-specific needs, administered under consistent environmental management system principles with oversight provided by a centralized Environmental Health and Safety Team.
- We offer robust training covering the critical aspects of our environmental management system, updating our training at least annually and when regulatory changes occur.
- Greif strives for zero instances of non-compliance at our sites and measures performance based on the results of regulatory compliance inspections. In 2022, we underwent eight inspections.
מדוע חשובות מערכות ניהול סביבתיות
Greif’s ability to operate hinges on our capability to abide by environmental laws and regulations applicable to our business. Our environmental management systems (EMS) ensure we sustain our compliance. We use our deep understanding of the complex regulatory environment and a proactive approach to maintain compliance and work with regulators to effectively manage environmental impacts. Failure to uphold these systems would render the Protecting Our Future pillar of our Build to Last Strategy unattainable.
ממשל
Greif has used our proprietary Compliance Management System (CMS) since 2011 to track and monitor compliance with applicable laws and regulations, including environmental compliance related to facility emissions, energy, water and waste. Facility roadmaps are also created, stored and reviewed in our CMS. Our Environmental Health and Safety (EHS) Team, led by our Senior Vice President of Global Operations, with support from the Global EHS Manager, the Senior Environmental Manager, the Environmental Specialist, Environmental Engineers, the EHS Director and regional managers that support Greif’s four operating regions, administer the CMS. Our recent realignment toward a global operation strategy has integrated the EMS Teams for Global Industrial Packaging (GIP) and Paper Packaging & Services (PPS) within our Global Operations Group, increasing efficiencies and collaboration across our business.
Greif is subject to many EHS regulations due to our global footprint and the potential environmental, health and safety impacts of our manufacturing operations. Across our organization, we use various tools and processes to appropriately manage geographic- and business-specific needs. Our global environmental management systems are administered under a consistent set of principles. Internal and external parties perform audits regularly to confirm that facilities comply with all required regulations.
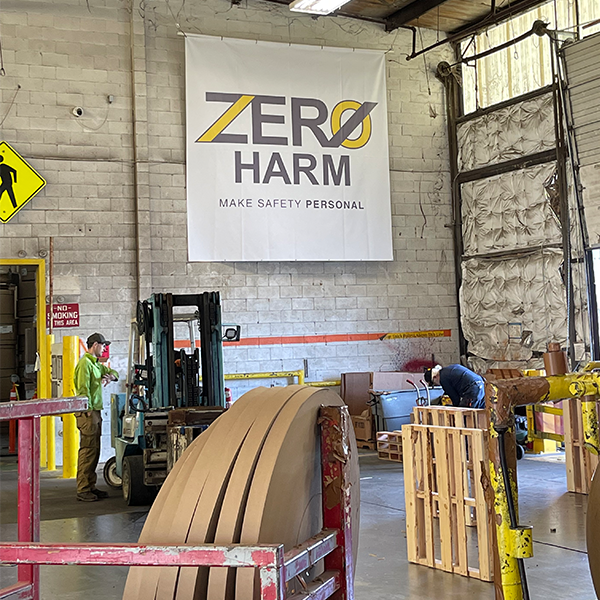
אימון EMS
Greif provides regular EMS training, directed by our EMS Team throughout the year, to routinely evaluate and update with new statistics, as needed. For example, our PPS business conducted seven training events on EMS usage in 2022. Our EMS Team directed approximately 196 compliance trainings events at North American PPS and GIP sites as well as all EMEA sites in 2021. These compliance training events include:
- הדרכה שנתית לרענון פסולת אוניברסלית
- SPCC Annual Refresher Training
- פסולת מסוכנת והדרכה לרענון חירום
- DOT Hazmat Shipping 3-year training
- הדרכת רענון של תוכנית המודעות לאסבסט
- Annual RCRA Hazardous Waste Refresher Training
- אימון רענון שנתי למזבלה פסולת מוצקה
- הכשרה לניטור אישורי אוויר ופליטות
- אימון אטימות
- אימון ריענון שנתי של Stormwater
- אימון הפחתת רעש
- אימון בקרת אבק וחלקיקים
- אימון ריענון שנתי של Stormwater
- הכשרה לאישור מי סופה תעשייתי
- אימון לכידת פליטות
- VOC Legal Requirement Training
Greif facilities in North America supplement their compliance management systems through Dakota, an advanced EHS compliance and risk management software that tracks new and upcoming regulations applicable to each facility’s unique profile. Greif supplements our use of Dakota by conducting internal and third-party audits to determine additional facility-specific tasks that may support better environmental risk management. This year, we conducted in-house audits quarterly for all PPS facilities. We also conducted regular and as-needed internal audits for the GIP business. All-encompassing third-party environmental audits have been paused since 2020 due to the COVID-19 pandemic but are planned to resume in 2023.
Though regulations and environmental impacts vary between facilities depending on operations, regulations and geography, the EMS team ensures all comply with air permits and routinely trains colleagues on particulate matter, odor, noise and other air pollutant emissions. Additionally, Greif minimizes and reduces hazardous materials, including volatile organic compounds (VOCs), by finding and using chemical substitutions. Greif uses CMS to develop relevant tasks for facilities to complete, and SBP, Progea and Resource Advisor are other systems used to monitor emissions. Such tasks and other relevant initiatives to monitor and reduce emissions may include regenerative thermal oxidizers (RTO) inspections, industrial hygiene surveys, source testing, engineering technologies for filtering or reducing emissions and routine maintenance. Please visit the איכות המוצר section of our report to learn more about our product safety and standards.
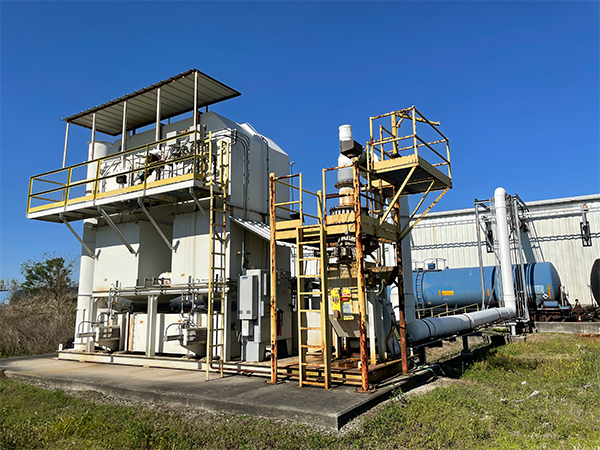
מחמצנים תרמיים רגנרטיביים
In 2022, Greif introduced and fully implemented a maintenance program to advance the longevity of our regenerative thermal oxidizers (RTOs) that control volatile organic carbon (VOC) emissions at 10 of our GIPNA sites across North America. Continuing our shift to a corporate-driven management system, we work with a third-party partner to manage the recently implemented devices. Our third-party partners assist us in assuring that our RTOs are maintained in compliance with all relevant regulations and in avoiding or solving any maintenance-related issues. We will continue to have quarterly, semi-annual- and annual maintenance evaluations, tracking this program within our Compliance Management System (CMS). In 2023, we plan to install new RTOs at our Baytown and HS1 facilities to improve efficiency and expand to all applicable facilities in the future. At our Warminster facility, we built full enclosures to capture all emissions and direct them to a recently optimized RTO. Before this project, the site produced nearly 20 metric tons of annual emissions. We estimate next year’s emissions will be eight metric tons, a 60 percent reduction.
In 2022, we rolled out a global environmental risk tool. This tool was created based on a global risk assessment conducted at all sites, excluding the Europe, Middle East and Africa (EMEA) region, which completed a separate risk assessment. We went through multiple iterations of the tool during its production to ensure its risk assessment, calibration and standardization capabilities. Since its launch, the tool has helped us evaluate sites with high environmental risk, allowing us to take the necessary corrective actions.
To manage chemical use, we continued our New Chemical Request and Equipment Pre-Acceptance Review processes in 2022. We also use a safety and environmental review process that requires corporate review when a facility requests to purchase or, at our Delta locations, process a new chemical product. The chemical undergoes an environmental review conducted by our corporate environmental engineer and a safety review performed by the regional EHS manager. The director of EHS and senior environmental manager review the results, and if approved by both parties, we begin onboarding the chemical. This process allows us to mitigate the actual and potential impacts of potentially hazardous chemicals.
In our PPS business, we continued our project development checklist. When a mill has a new capital project, the project manager must fill out the environmental checklist form, disclosing the project’s impacts, regardless of whether significant impacts are expected. The comprehensive checklist includes factors such as compliance, changes in emissions and wastewater management. Once complete, our EHS professionals review the list to confirm whether the project can progress. The checklist implementation ensures that all new equipment meets our environmental, quality, health and safety standards before being approved for purchase and installation.
We have continued our Management of Change (MOC) process in GIP NA to assess potential commercial, EHS, plant, quality and regulatory impacts of manufacturing or materials changes, completing 88 MOC reviews in 2021. In 2022, we extended the MOC process to the EMEA region and completed 55 reviews. We also completed and uploaded environmental checklists for all our Title 5 facilities. In PPS, 28 new Chemical Requests were conducted in 2022.
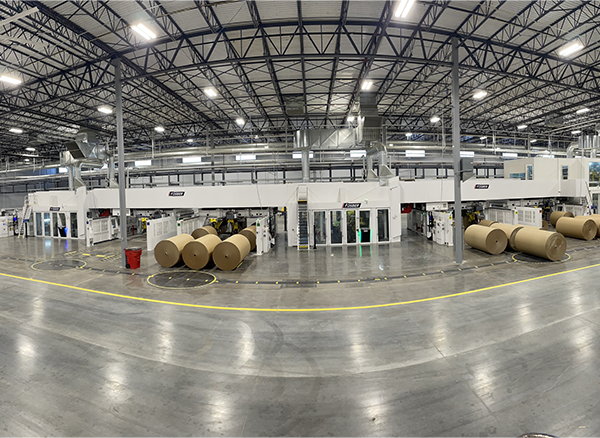
EMS Certifications
Each Greif production facility manages quality, safety and environmental standards through certifications such as OHSAS, ISO, FSSC and SQF. Our PPS operations maintain ABI, FSC, OSHA, PEFC®, SFI®, RPA 100 and RPTA FDA certifications. All our CorrChoice facilities and most mills have SFI® Chain of Custody Certification, and all our mills are certified to FSC® (FSC® C003539) and PEFC® Chain of Custody standards. Additionally, most mills have RPA100 certification. Globally, 15 sites have achieved ISO 14001 certification. Please visit our 2023 Certificates מסמך כדי ללמוד עוד על אישורי המתקן שלנו.
מטרות, התקדמות וביצועים
In previous years, Greif has completed a series of environmental management audits across North America (NA). Building on this program over the past two years, we launched and carried out a third-party environmental audit program across EMEA. Like its NA predecessor, this program established organized processes to monitor environmental initiatives and progress. These audits were performed with local third-party experts to ensure the process was representative of the specific environmental conditions of each jurisdiction. We plan to resume external audits in EMEA and beyond in 2023.
Greif strives to have zero instances of non-compliance. If conditions of non-compliance are discovered, we take steps to immediately correct the circumstances of the non-compliance. We measure EMS performance based on regulator inspection results.