Highlight Stories
- Au sujet de notre société
- À propos de notre rapport
- Sustainability Strategies
- Goals & Performance
- ESG Reporting Indices
- Téléchargements de rapports
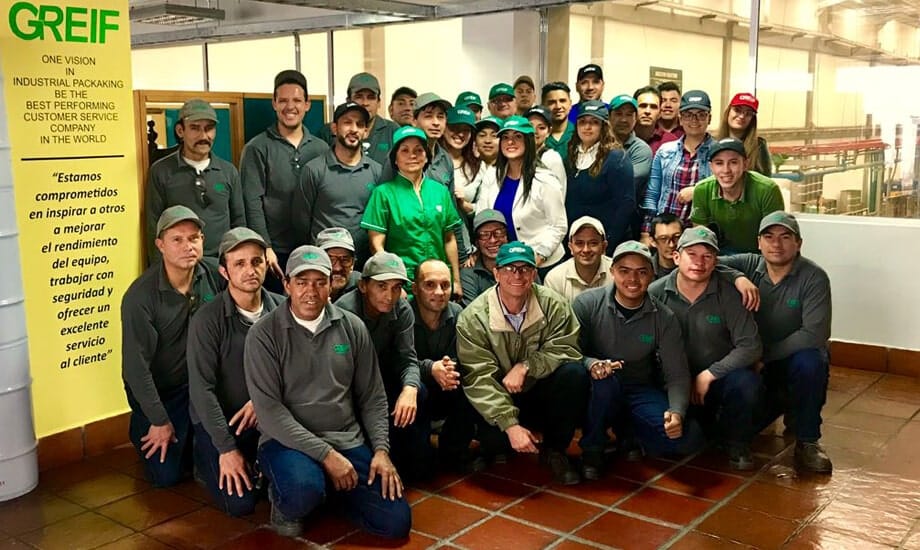
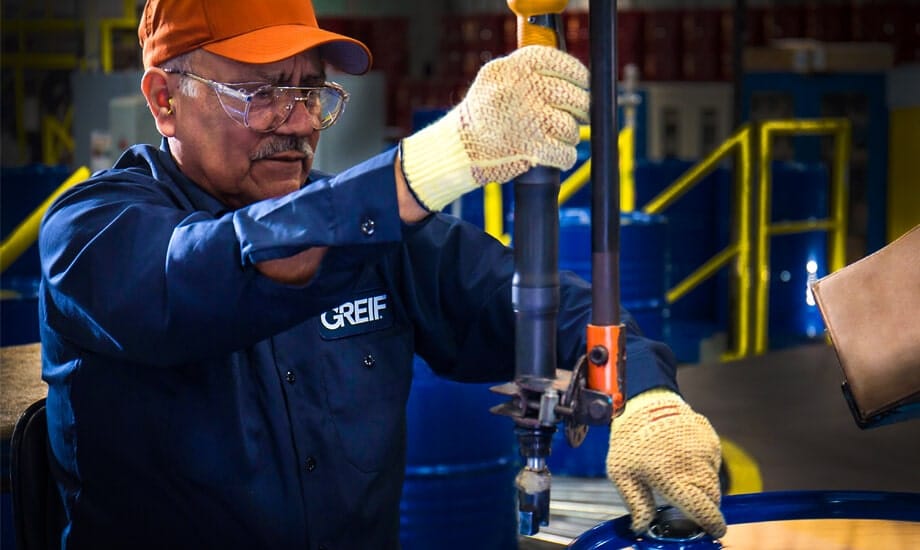
In 2014, our CAR data indicated that leaks were the most common quality complaint from customers. In response, we initiated a Zero-Leak Program to eliminate leaks from our products. When a leak complaint was received, it was escalated to the regional vice president and general manager and our engineering team was tasked with developing a concrete resolution to the problem and disseminating it to all facilities. Our focus on reducing leaks led to a 67 percent reduction in leak complaints from 2014 to 2018, as well as significant improvements in leakers in our Tri-Sure business.
In 2020 we kicked off a new global quality task force specifically to look at our most prominent customer issues related to product quality. Our focus was to analyze both external and internal factors to determine common trends. Through this we determined that our largest internal issues also correlated with our largest external issues. The largest customer issue continues to be product integrity. The group developed various action plans aimed at resolving these internal issues with the ultimate goal of reducing our largest customer issues. New metrics were created to keep track of the progress of these initiatives.
Leaker Rate | FY 2019 | FY 2020 | FY 2021 |
Asia Pacific | 0.37 | 0.14 | 0.29 |
Europe, Middle East and Africa | 0.23 | 0.23 | 0.12 |
North America | 0.22 | 0.22 | 0.16 |
Latin America | – | – | 0.07 |
Greif’s Global Industrial Packaging facility in Petaling Jaya, Malaysia demonstrated customer service excellence when they rose to the occasion to solve a customer’s packaging crisis in the idle of the COVID-19 pandemic. An existing Greif customer discovered they were unable to secure unlined ultramarine blue drums, which were required to ship edible oil from one of Greif’s competitors. Since the facility did not offer that product at the time, the Petaling Jaya team quickly worked to prepare new artwork, obtain external drum color approval and create a new product stock keeping unit. The team immediately began production and secured transportation for the drums to meet the customer’s urgent need. Due to the responsiveness and ingenuity of the team in responding to this emergency, the customer has continued ordering the product from Greif.
Greif’s Dalton, Georgia, PPS Recycling facility works closely with local flooring manufacturing plants to provide recycling services for tubes and cores, a significant waste stream produced by the industry. These same flooring manufacturers are also customers of Greif’s recycled paperboard tubes and cores. When the price for old corrugated cardboard (OCC) dropped in 2019, it became uneconomical to recycle these tubes and cores at market price. Greif engaged with the flooring manufacturers to develop a sustainable, circular solution that keeps waste out of landfills and allows Greif to continue providing our customers with excellent service and 100 percent recycled paperboard. Under the new business model, Greif receives payment for managing recyclable waste streams allowing us to process these materials and then send to our paper mills to manufacture 100 percent recycled paperboard.
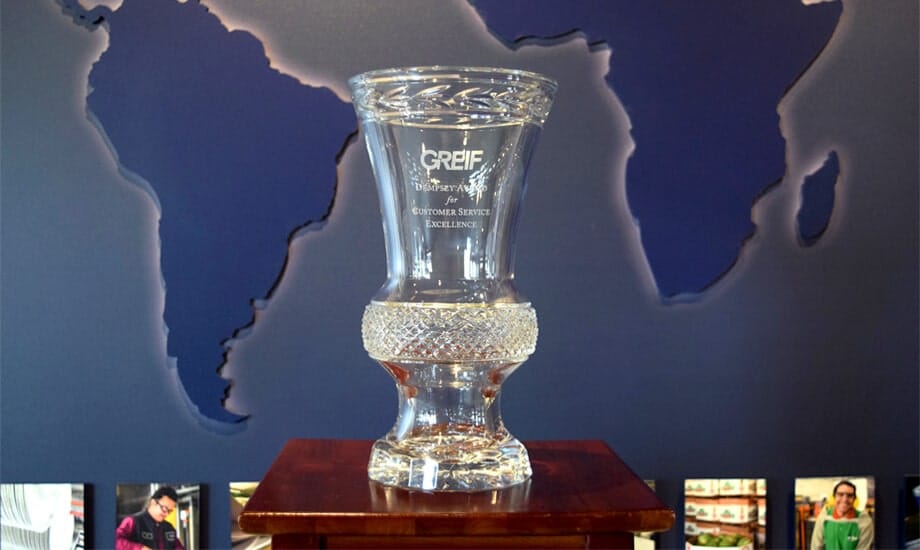
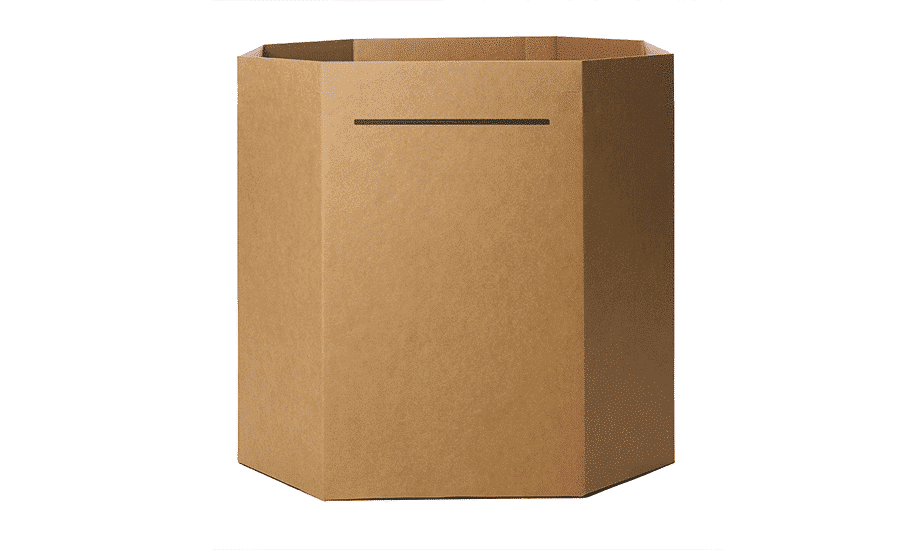
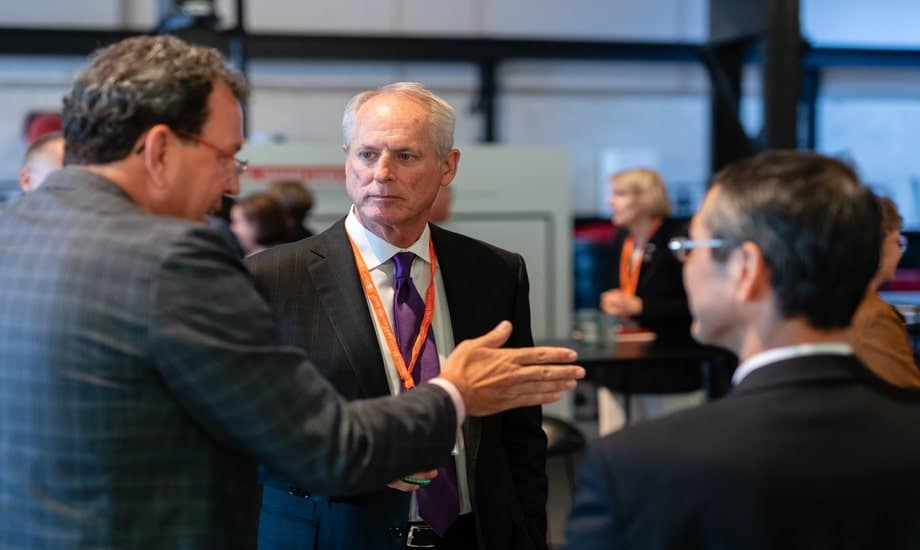
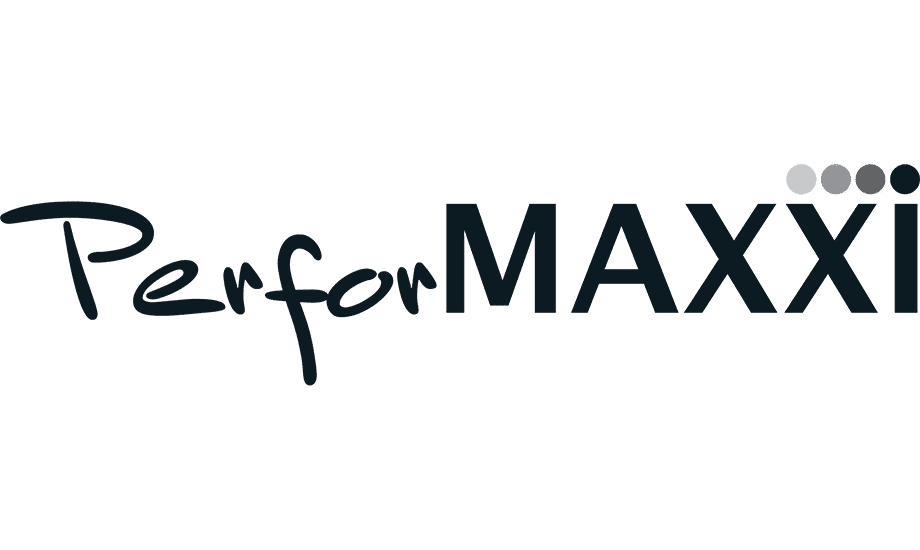
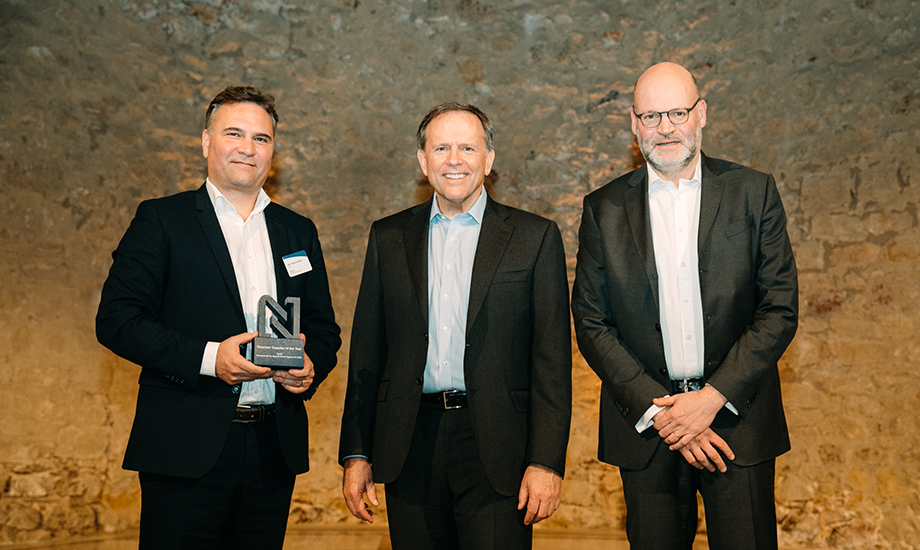
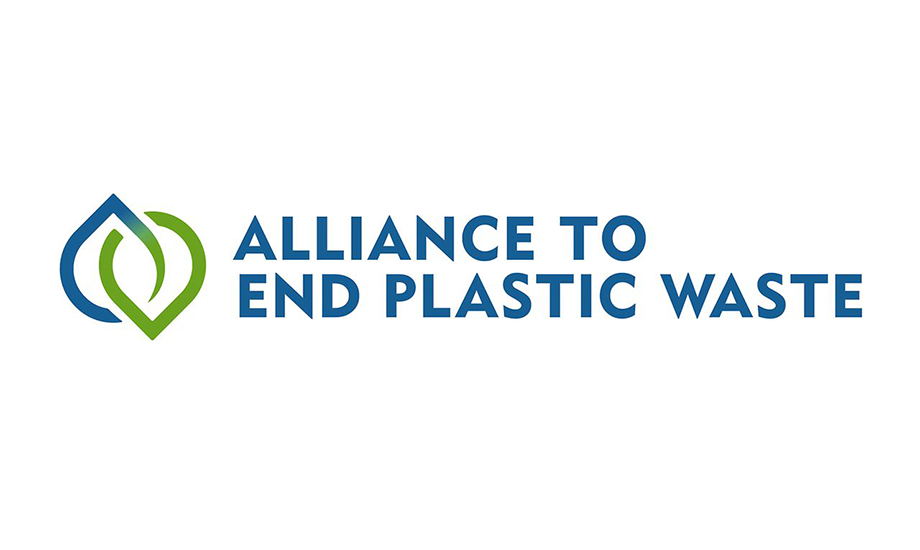
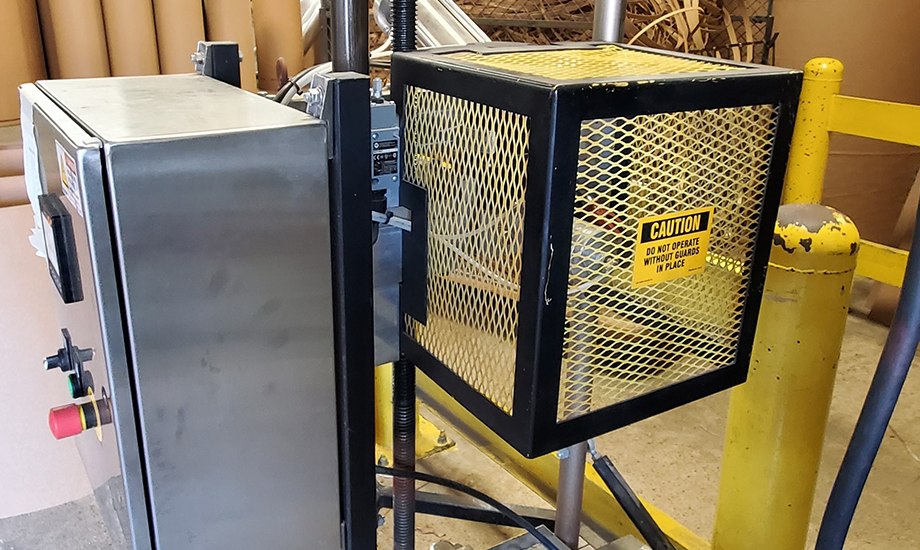
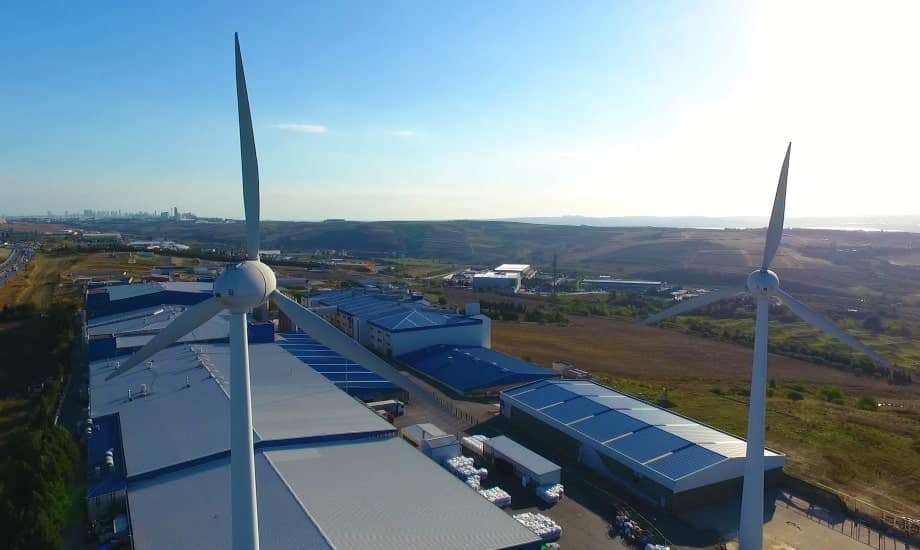
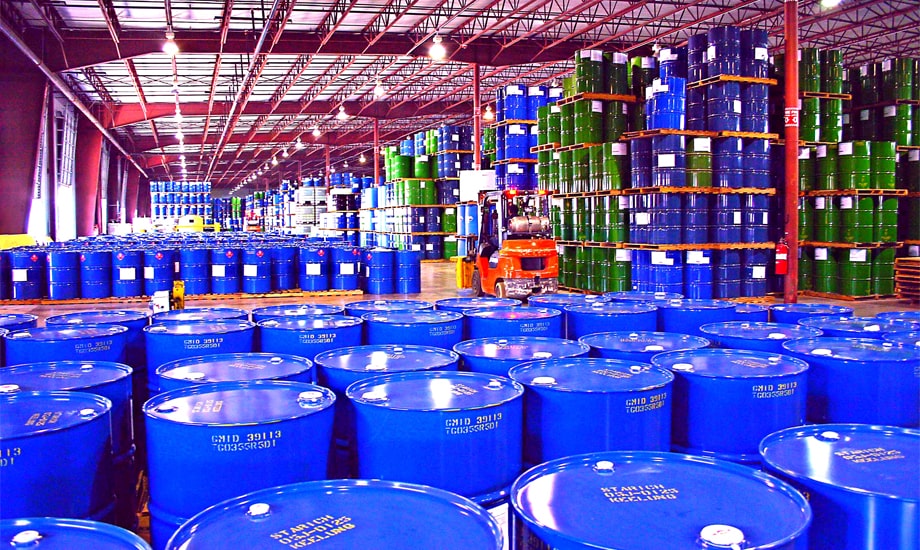
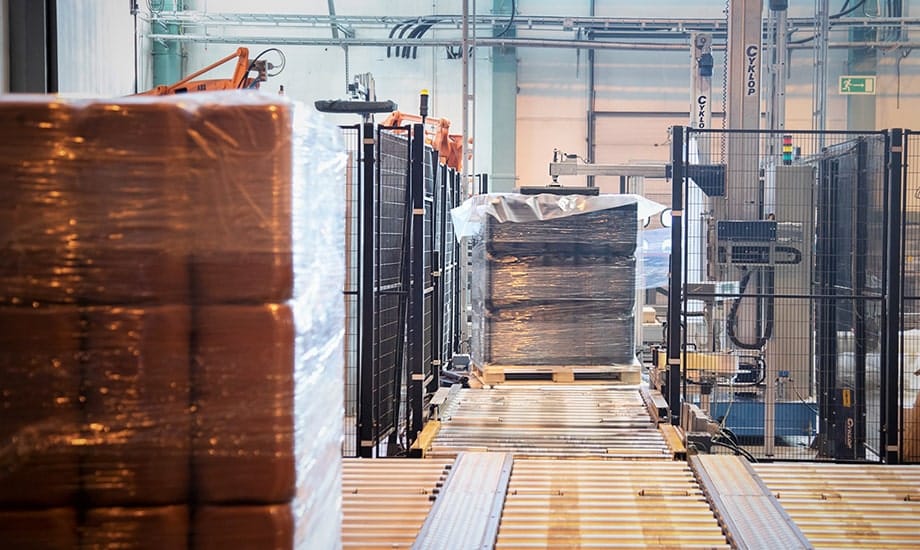
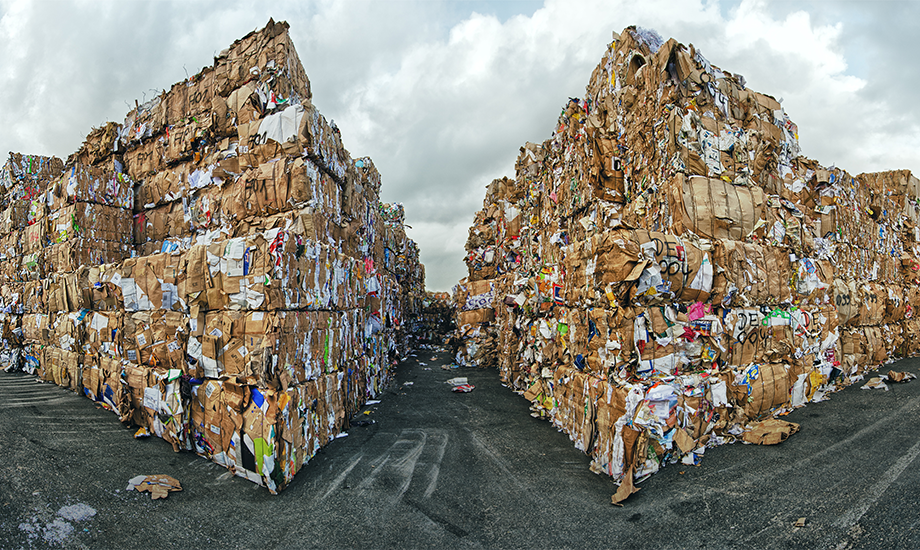
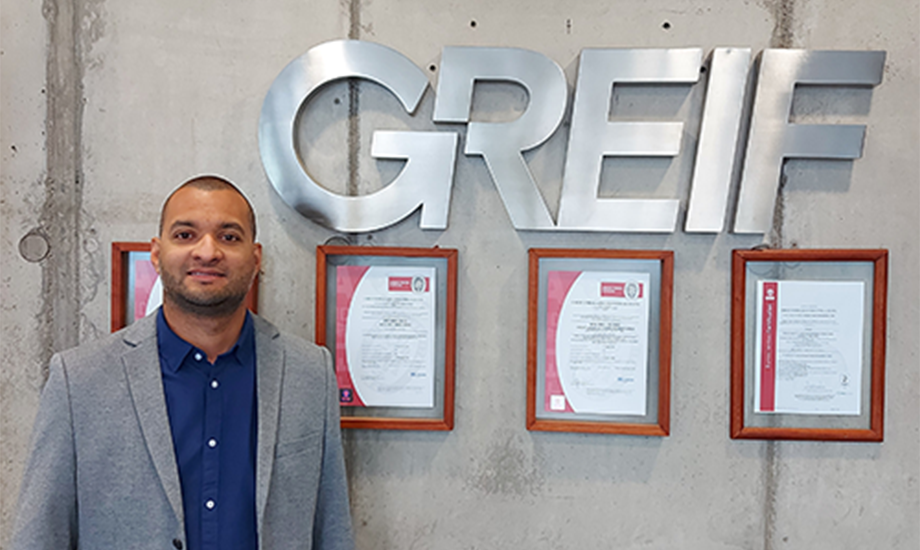
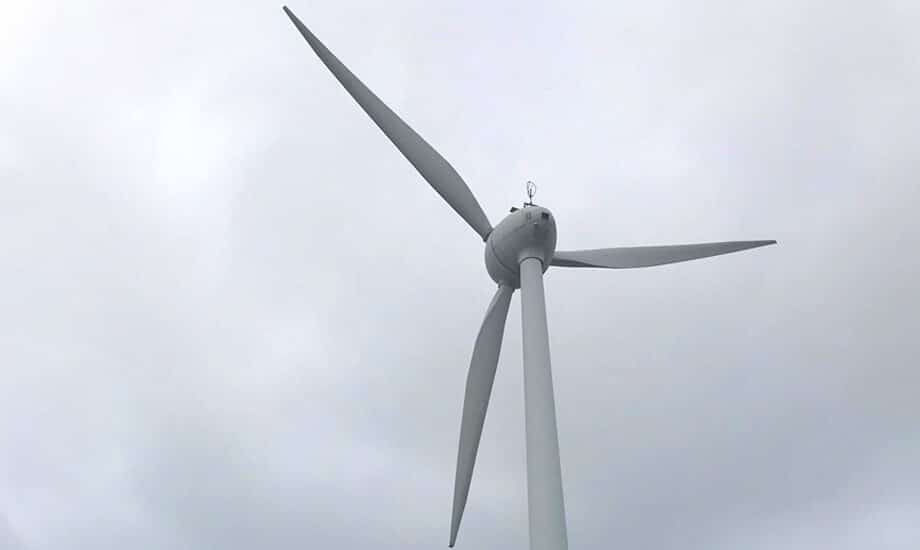
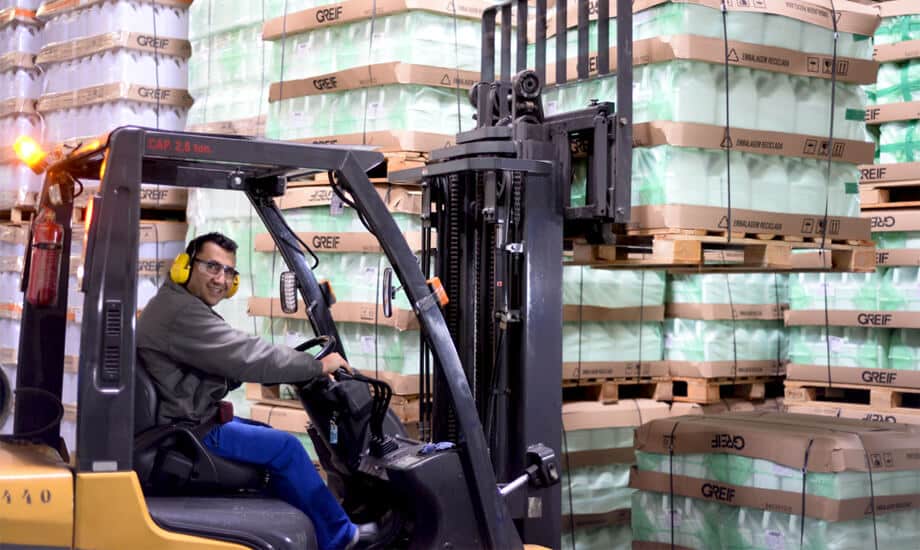
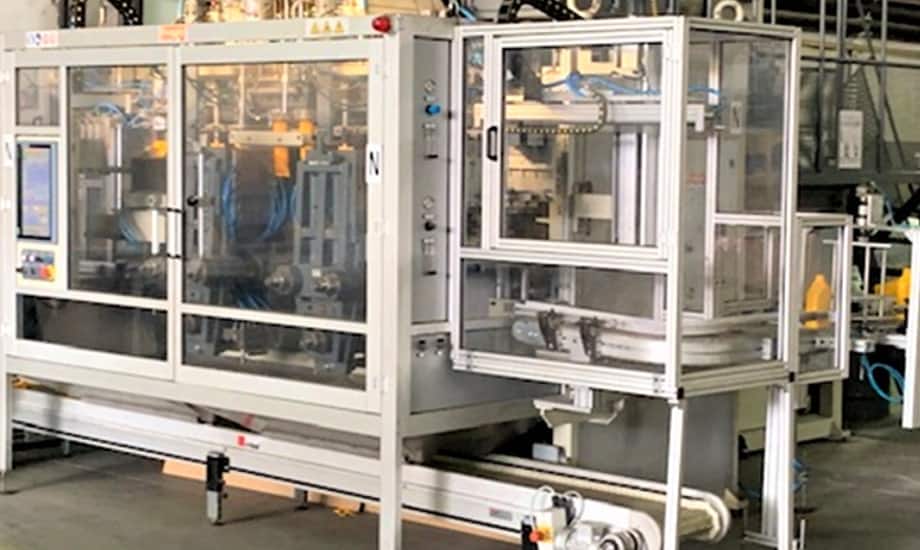
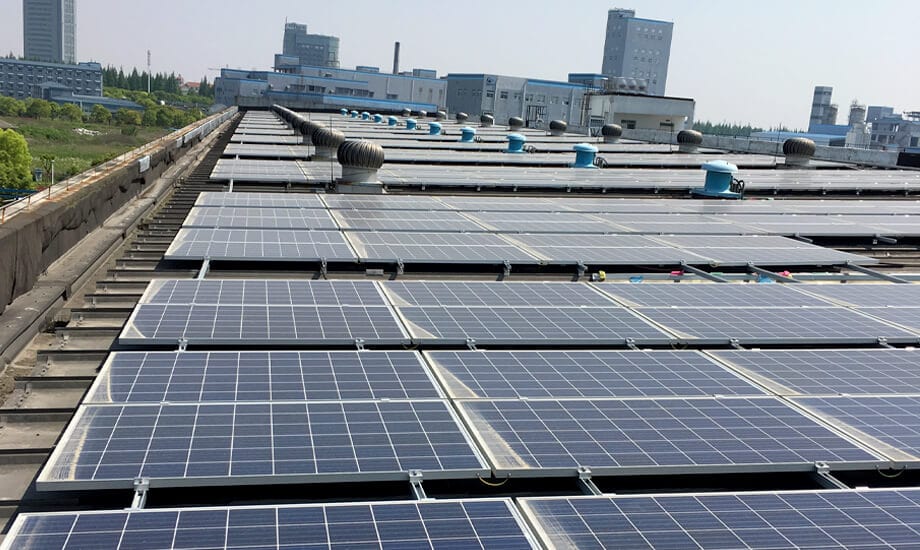
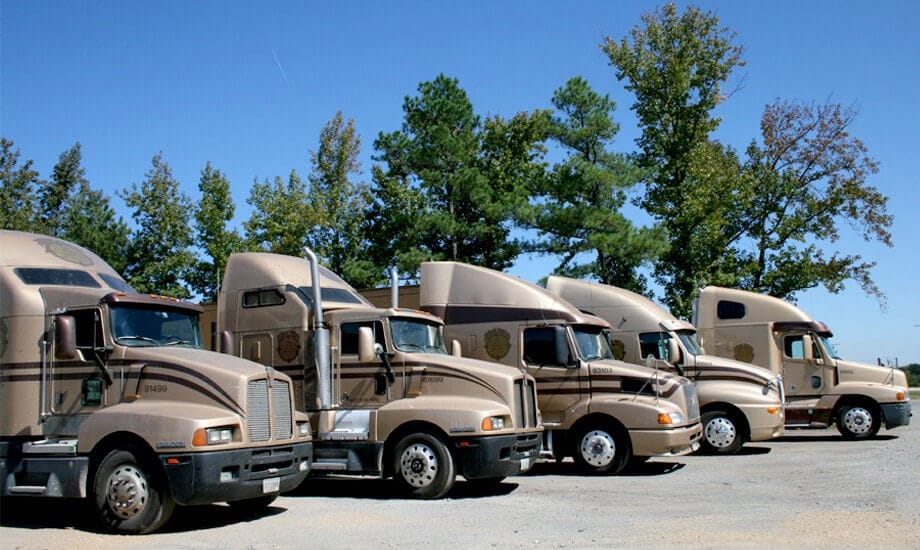
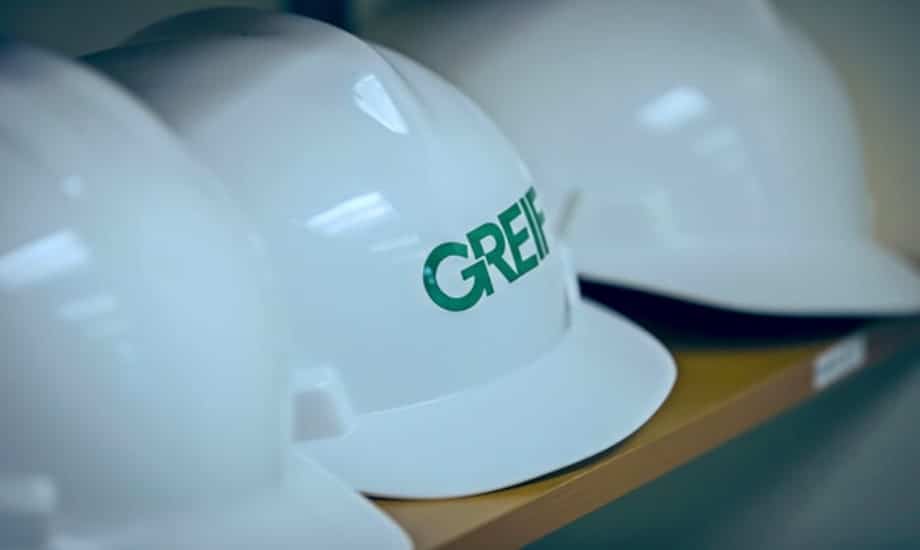
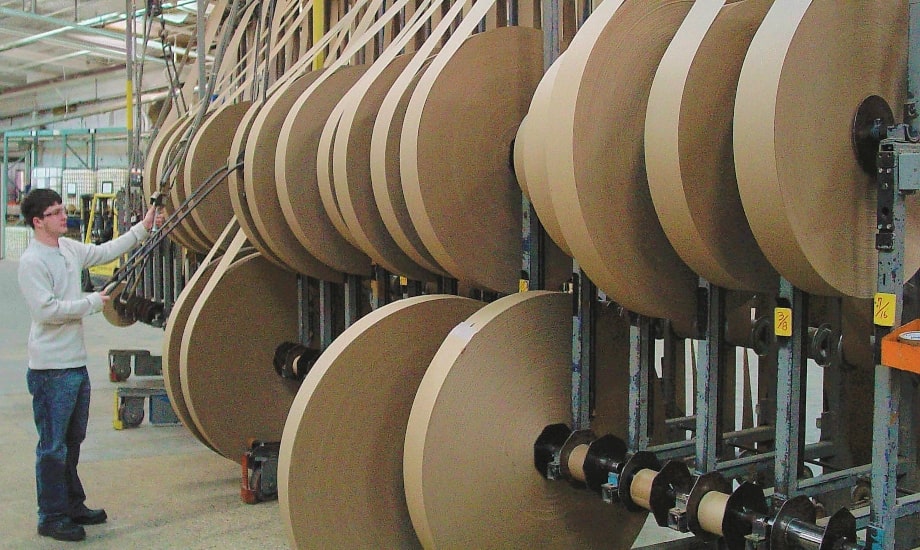
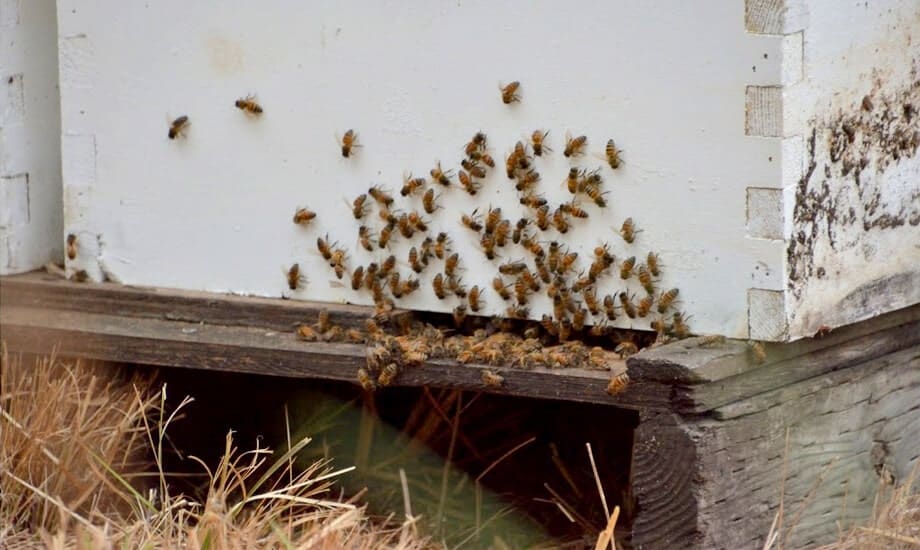
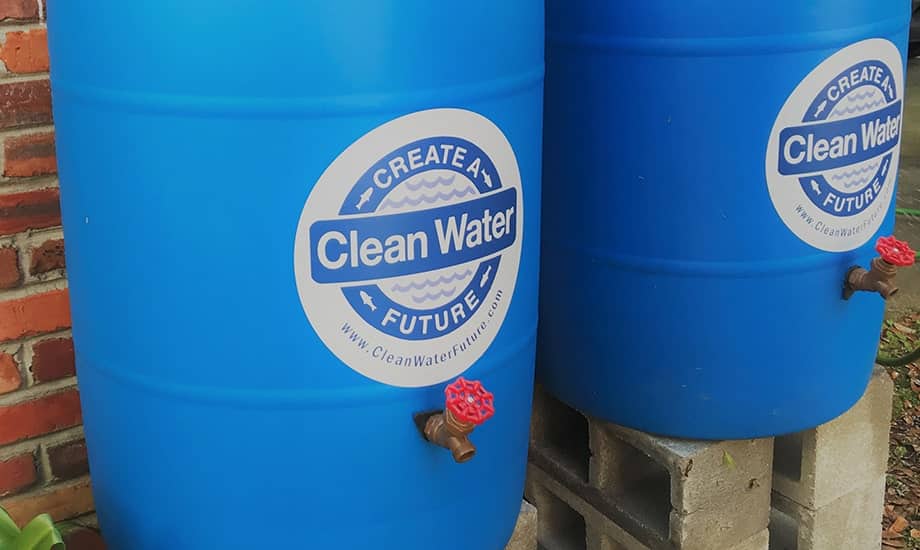
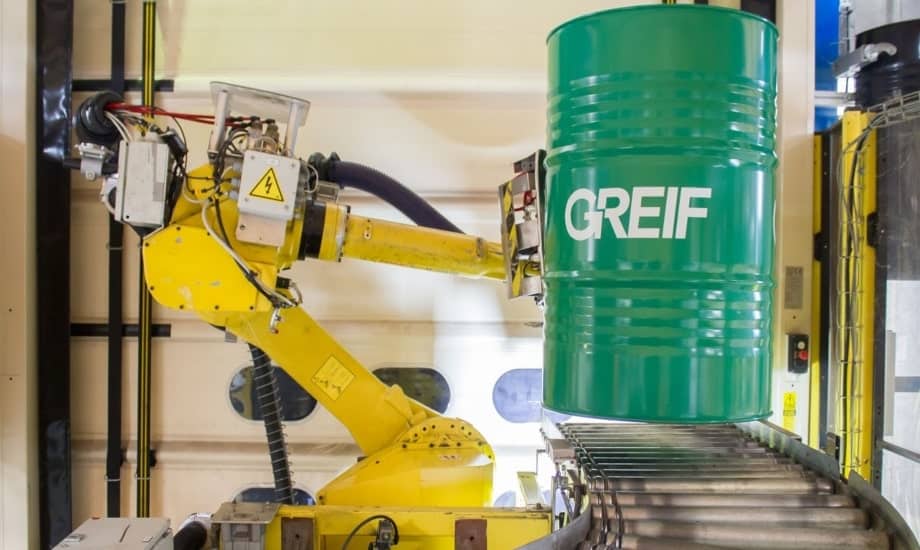
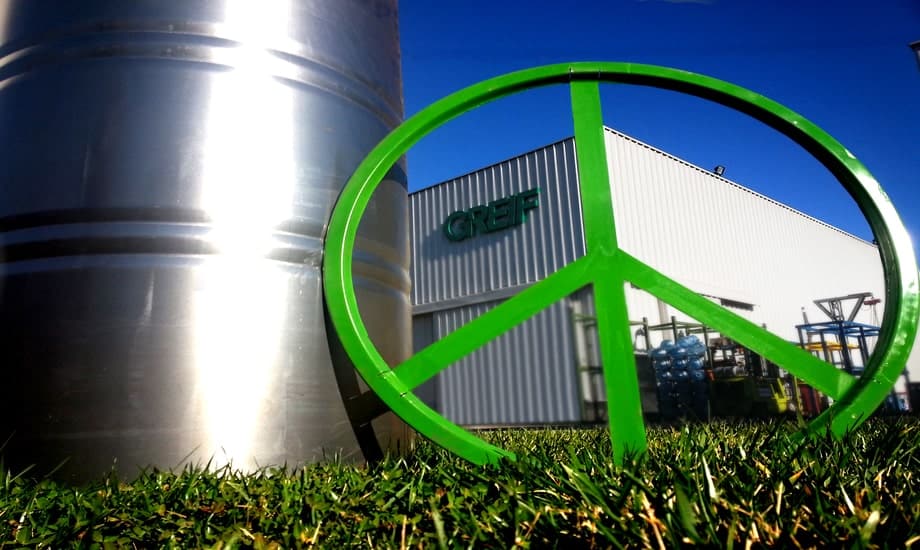
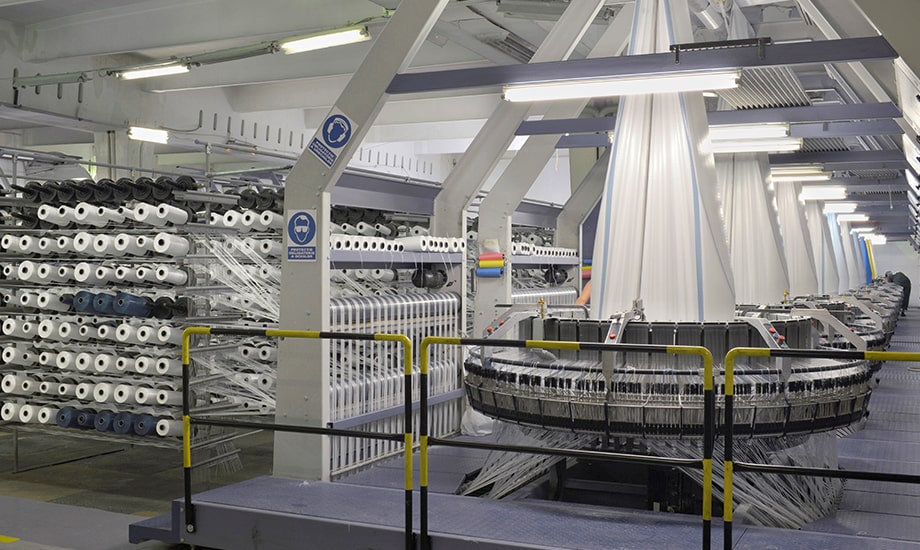
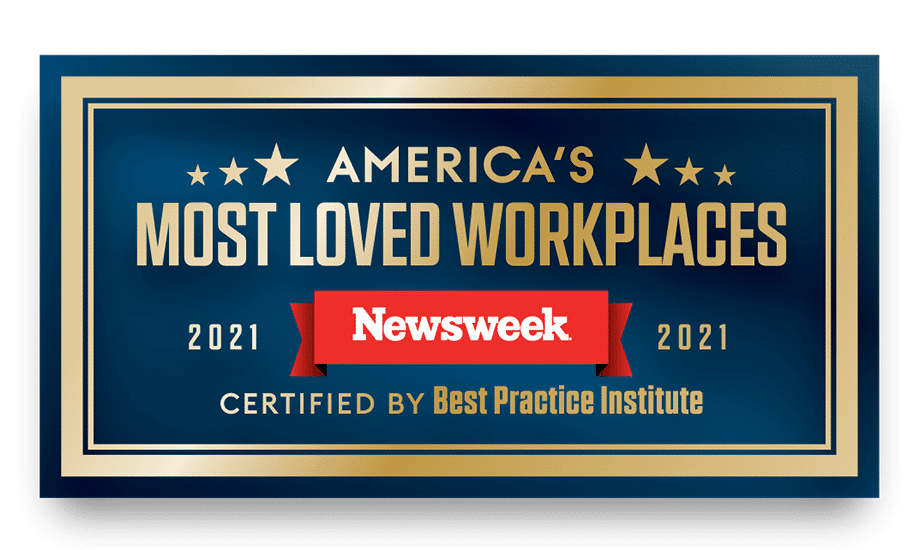

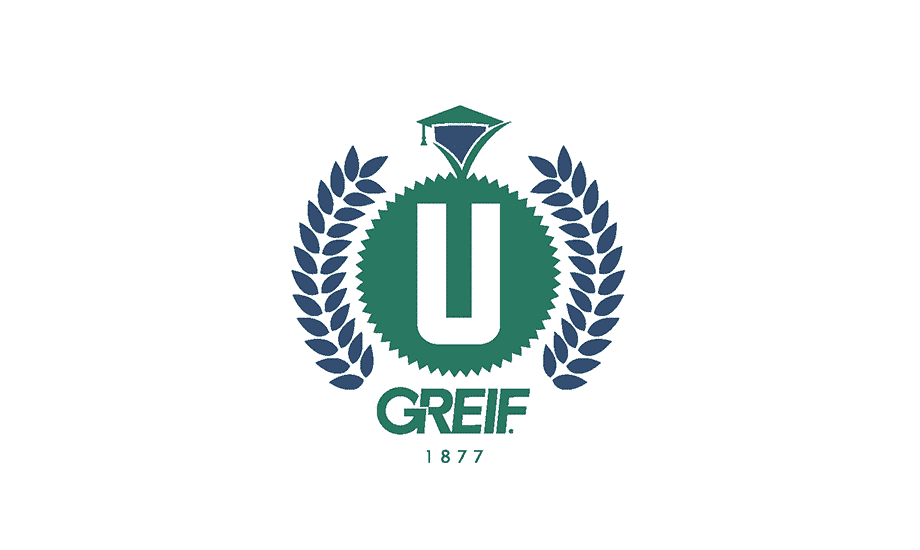
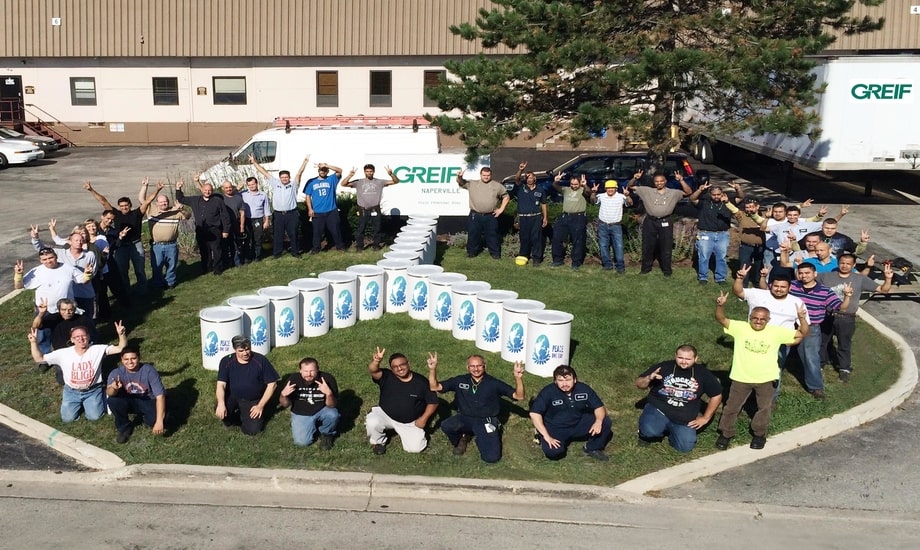
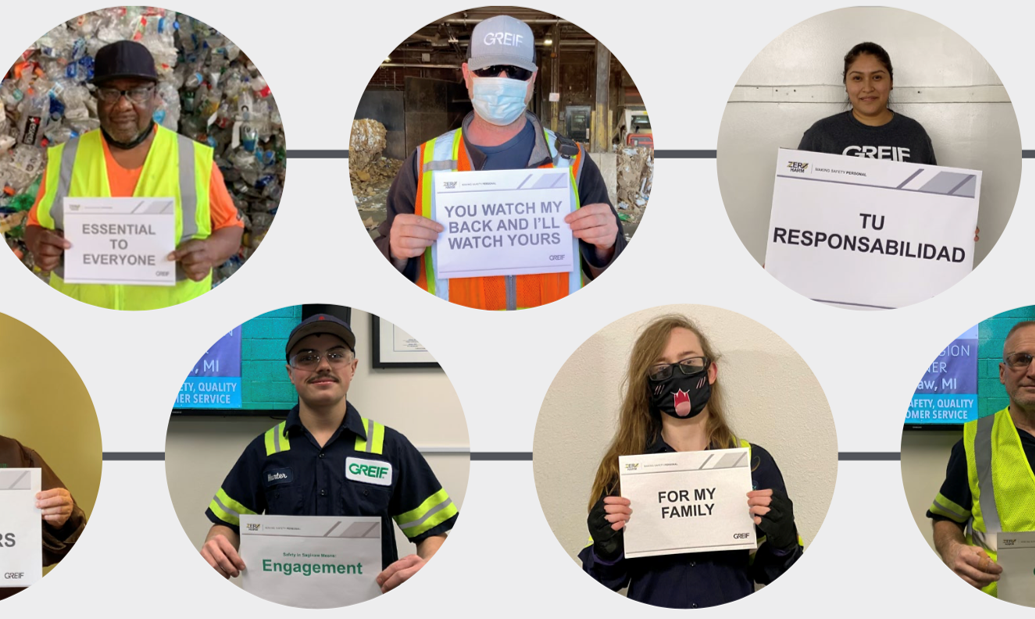
Greif’s long-term health and safety aspiration is to achieve zero accidents at all our facilities worldwide. While we recognize the challenge of this aspiration, 20 of our Global Industrial Packaging (GIP) facilities including the following sites have achieved ten or more years of accident-free operations:
- Amaititlan, Guatemala – 14 years
- Midland Warehouse – 14 years
- Angarsk, Russia – 13 years
- Beloyarsky, Russia – 13 years
- Esteio, Brazil – 13 years
- Chino, USA – 13 years
- Volgograd, Russia – 13 years
- Vologda, Russia – 13 years
- Delta Cincinnati, USA -12 years
- Kazan, Russia – 12 years
- Manaus, Brazil – 12 years
- Mandra, Greece – 12 years
- Pioneer, Singapore – 12 years
- Rio de Janeiro – 12 years
- Huizhou, China – 11 years
- Mombasa, Kenya – 11 years
- Vung Tau, Vietnam – 11 years
- San Juan, Argentina – 10 years
- Delta Shanghai, China – 10 years
- Houston Plastic, USA – 10 years
Chairman’s Safety Excellence Award
Each facility that achieves an MCR of zero wins the Chairman’s Safety Excellence Award. Globally, 94 of our production facilities received the award in 2021 and were recognized at a virtual ceremony.
Inclusive Leadership Training
The Inclusive Leadership Journey is for people managers and senior leaders at Greif to learn about inclusive leadership. The program covers the foundations of inclusive leadership for global leaders to develop and exhibit inclusive behaviors in the workplace. The training goes in-depth about defining and discussing the impact of unconscious and implicit bias, best practices for inclusion and actionable steps, and examining the impact of inclusion. The learning journey includes a confidential assessment of current level of inclusive behavior for each participant and a personalized action plan for implementation of key topics. The sessions began in October 2021, and will continue through April 2022.
Diversity Week in LATAM
At Greif, we encourage and embrace our diversity of culture, language, location and thought. During the week of August 9-13, 2021, the Human Resources Teams in LATAM held a Diversity week event to educate our colleagues on the importance of respecting others and living The Greif Way. The week-long event included virtual learning sessions covering the topics of Unconscious Bias, Gender, Women & Career, Generations, LGBTQIA+ and Diversity of Origins / Ethnicity. In total, more than 700 colleagues participated.
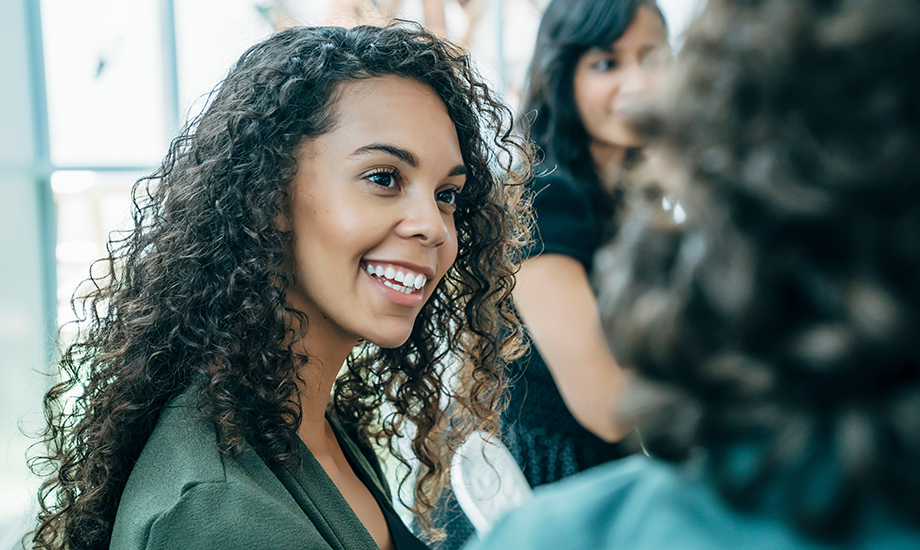
Laser Markings on IBCs
Greif Sweden/Nordic is the first in the market to replace ink jet markings with laser markings on Intermediate Bulk Containers (IBCs), reducing the use of solvent-based ink during production. By eliminating the use of solvents and ink, the production environment is cleaner. We also are able to reduce the weight of the IBC by one kilogram by removing the plate traditionally used for laser marking. We believe this innovation will set a new standard for markings on IBCs.
Knock Down Drums (KDD) for Remote Locations
Greif’s Knock Down Drums (KDD) offer the optimal sustainable solution for transporting steel drums to remote locations. Semi-finished drum parts are shipped and assembled locally on site with minimum people and equipment. The unique concept allows transportation of up to 1,176 KDDs in a 20’ sea container compared to 80 full finished drums, saving valuable space, optimizing transport costs and minimizing our customers’ carbon footprint during longer transit times. Drums are delivered directly to our customers’ filling station helping to improve efficiencies with minimum stock and less manual handling.
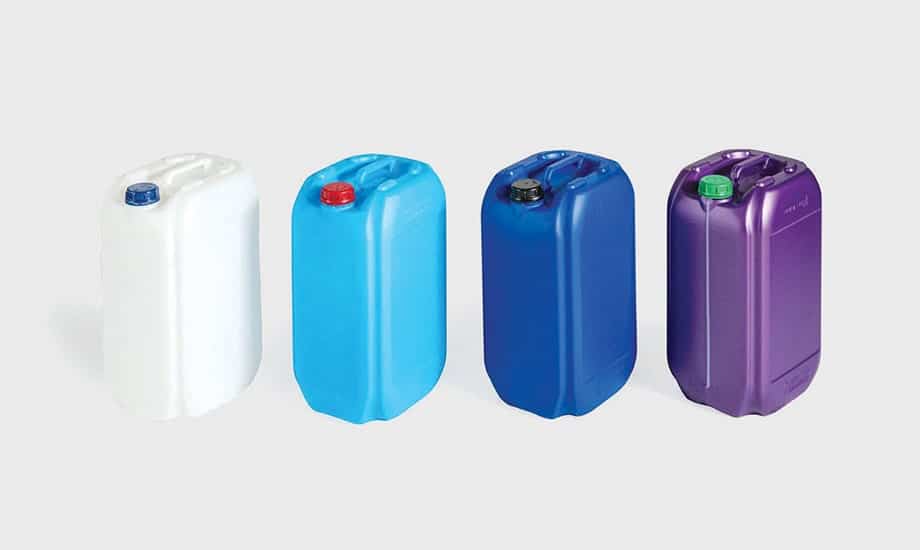
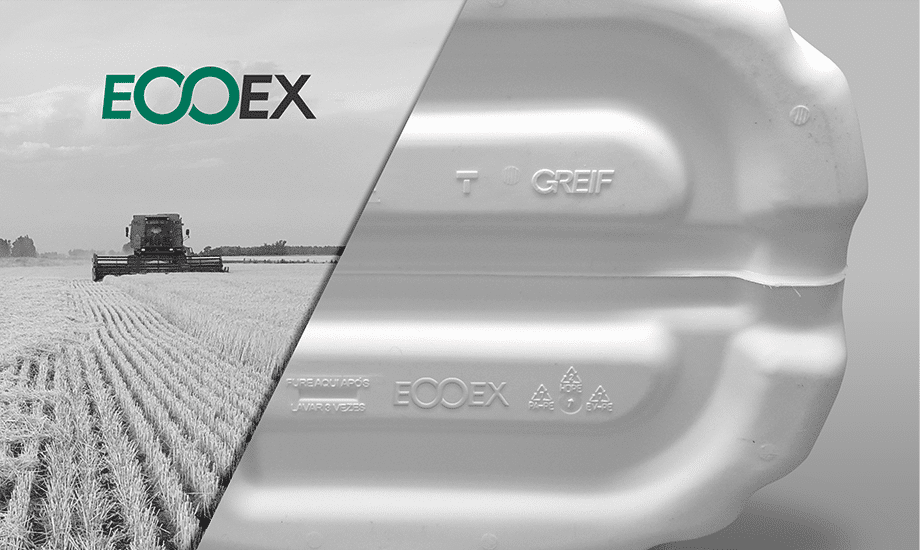
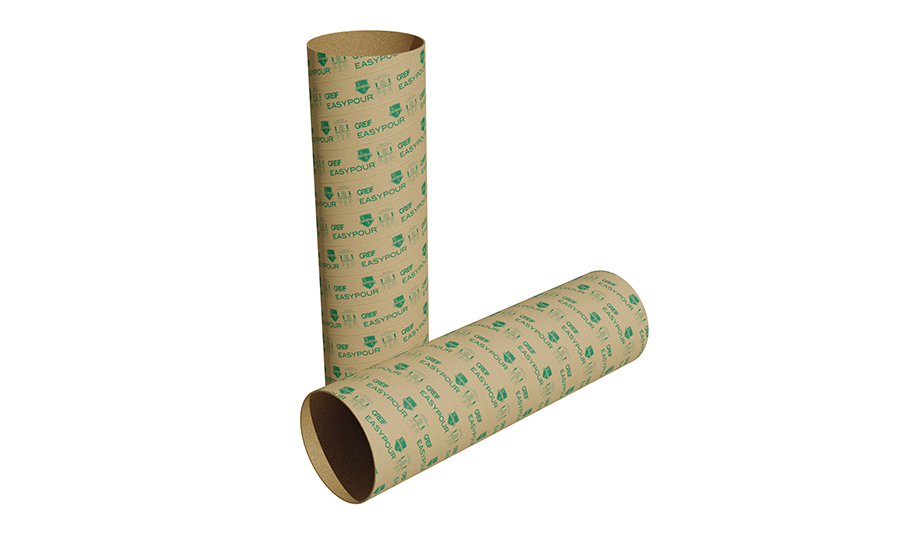
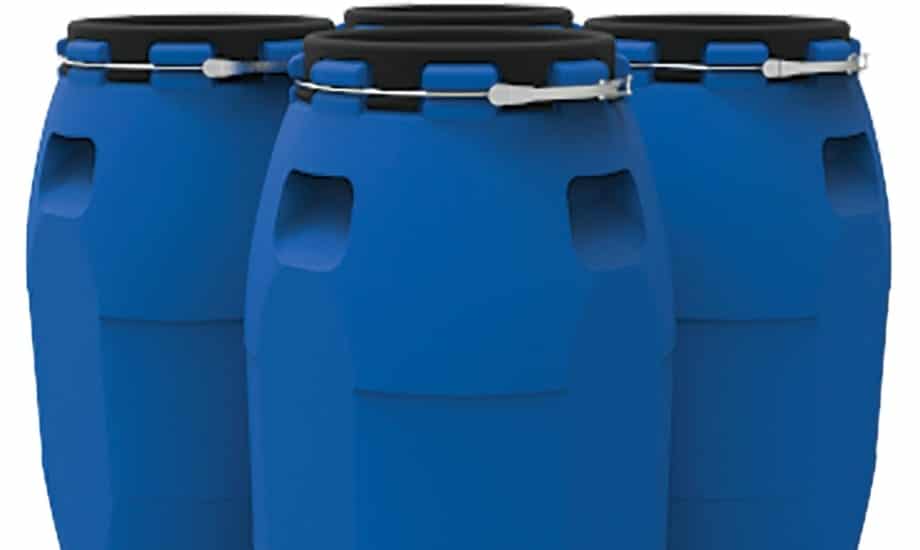
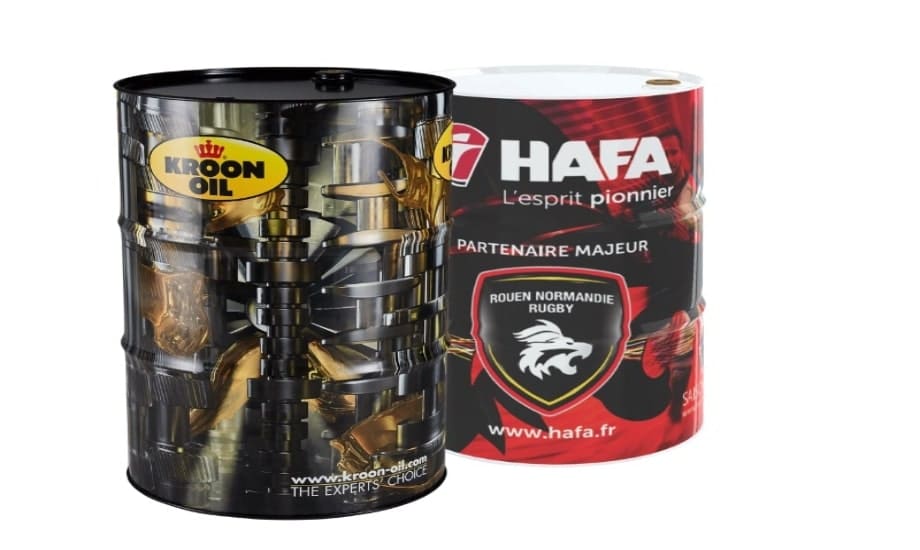
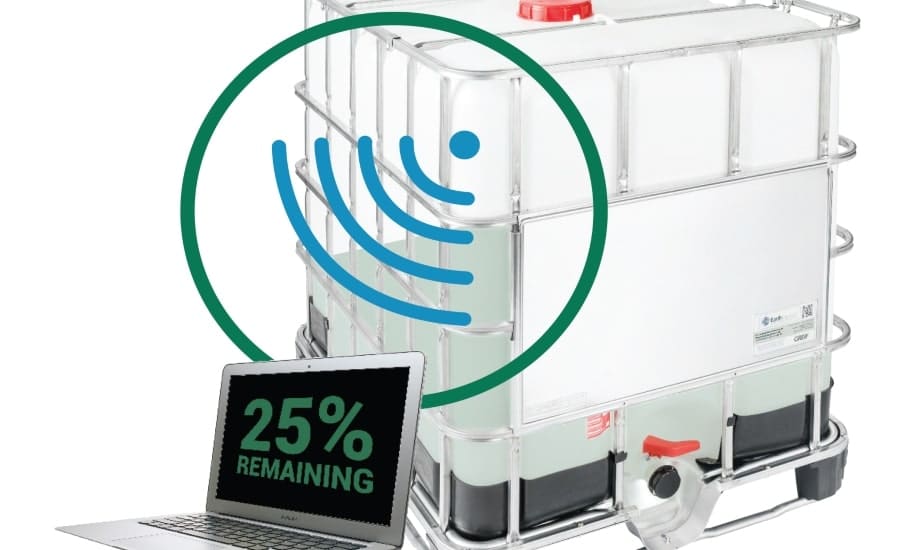
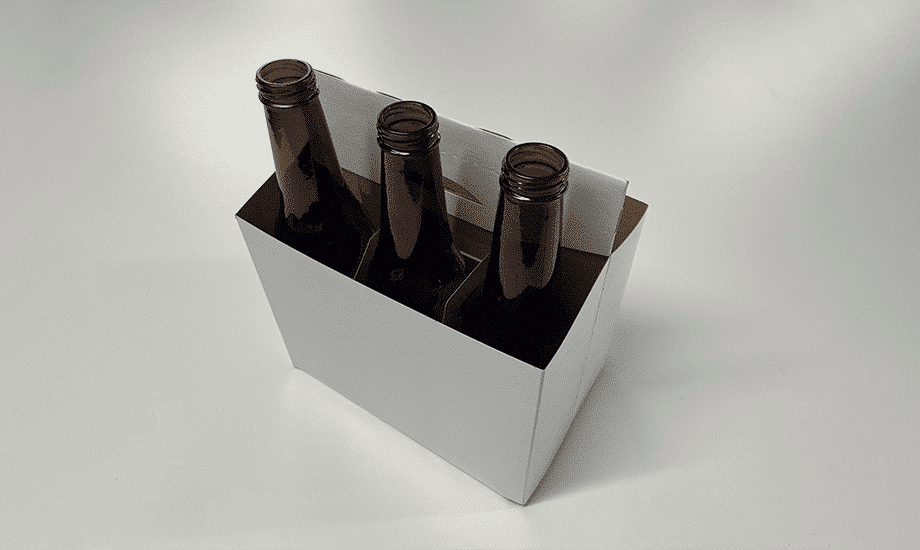
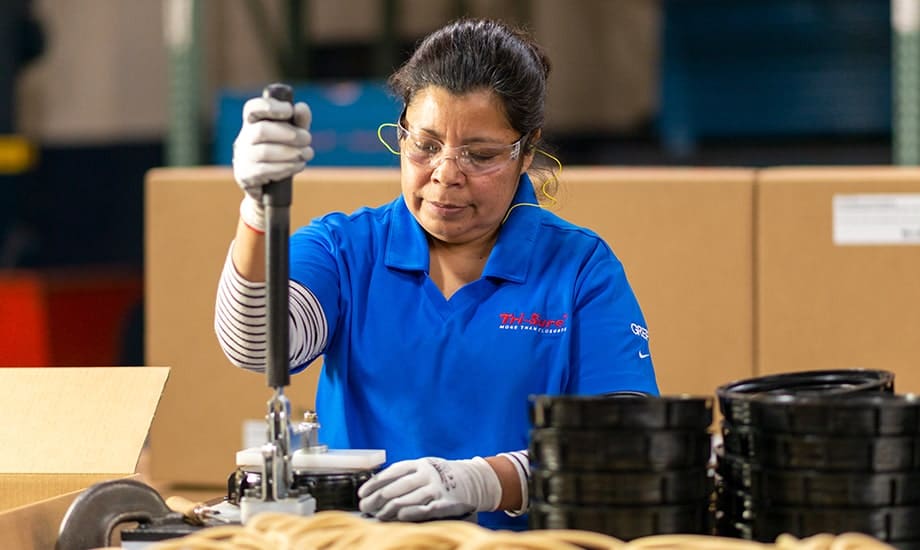
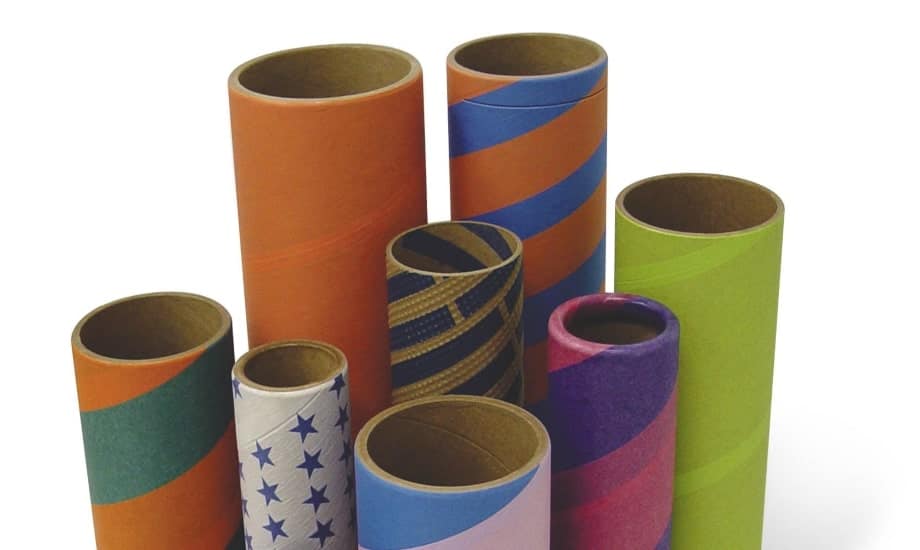
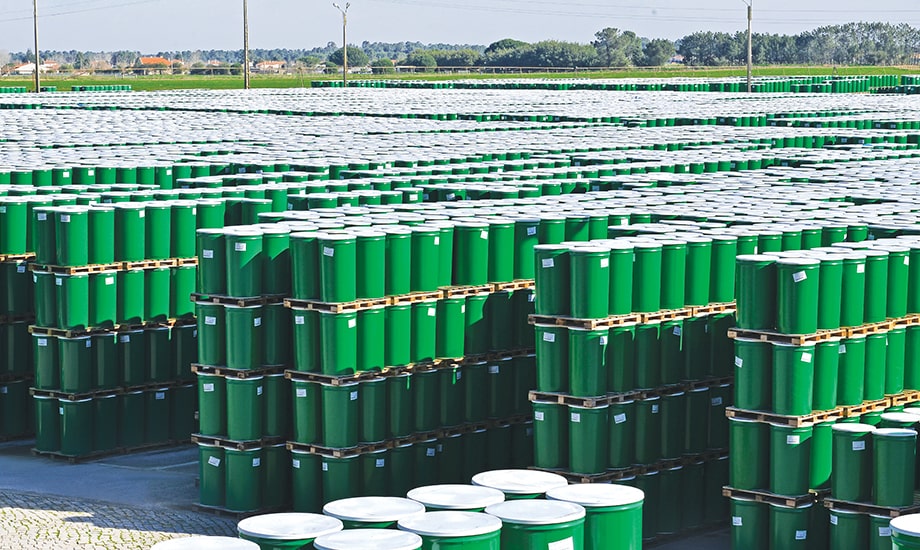
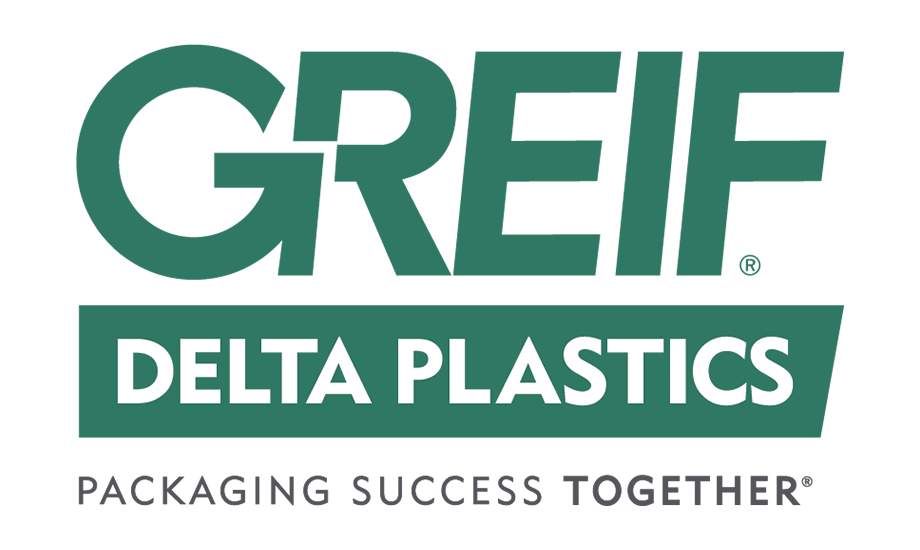
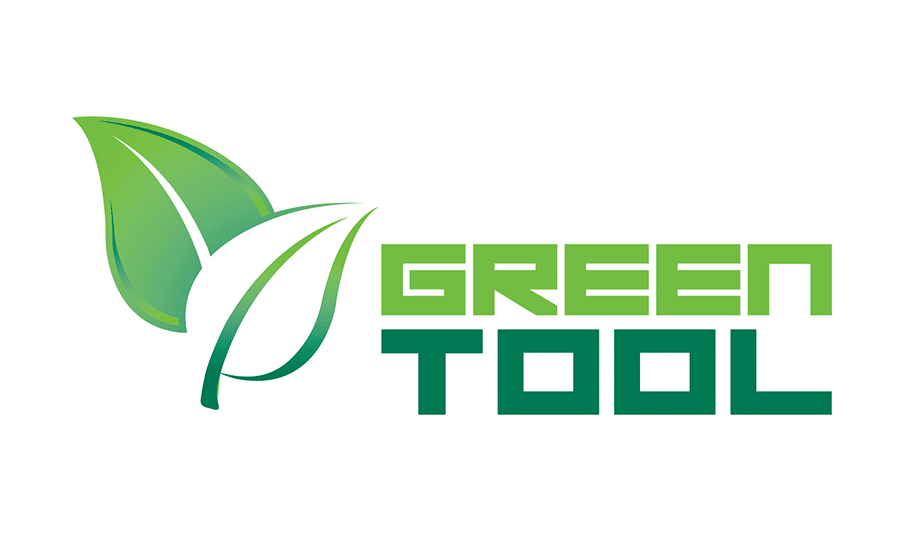
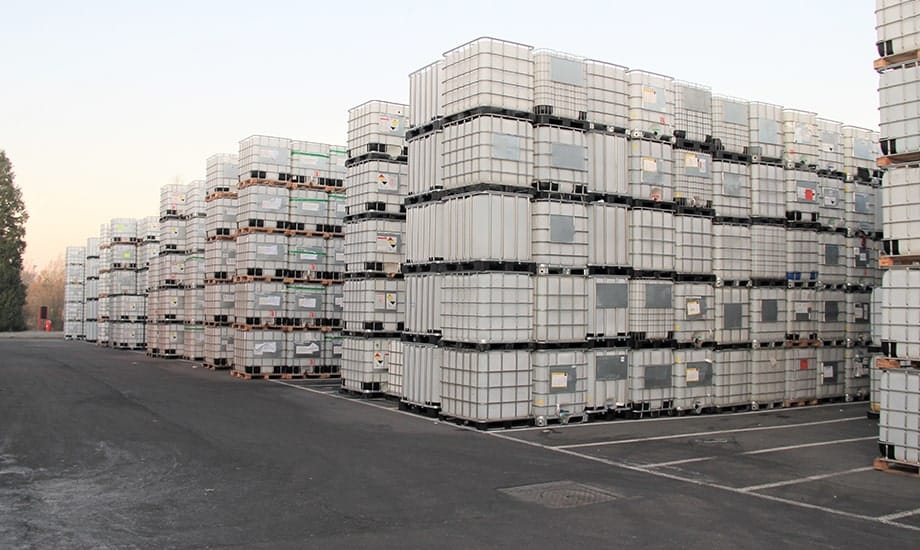
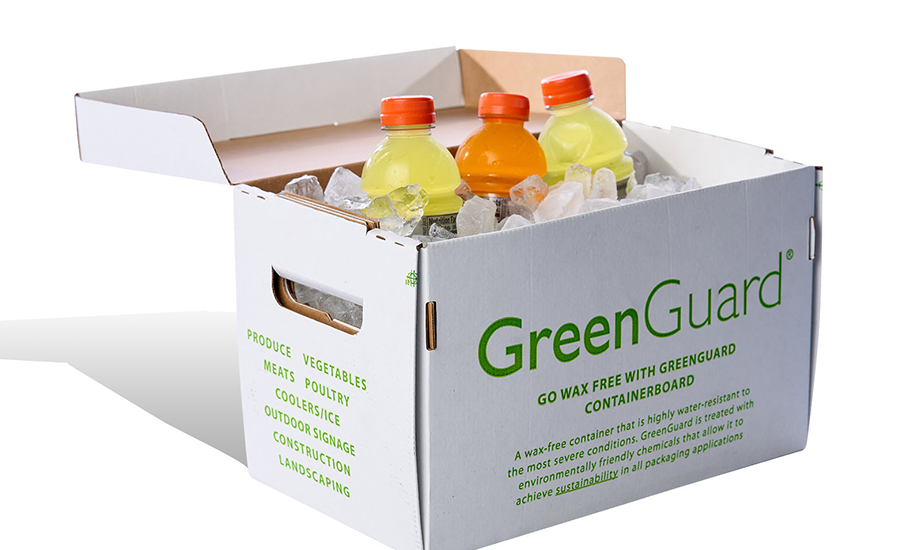
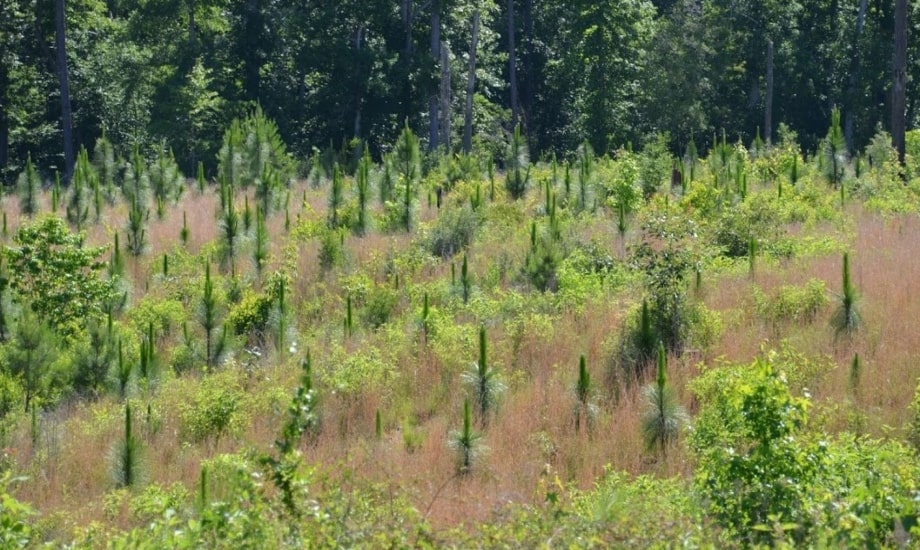
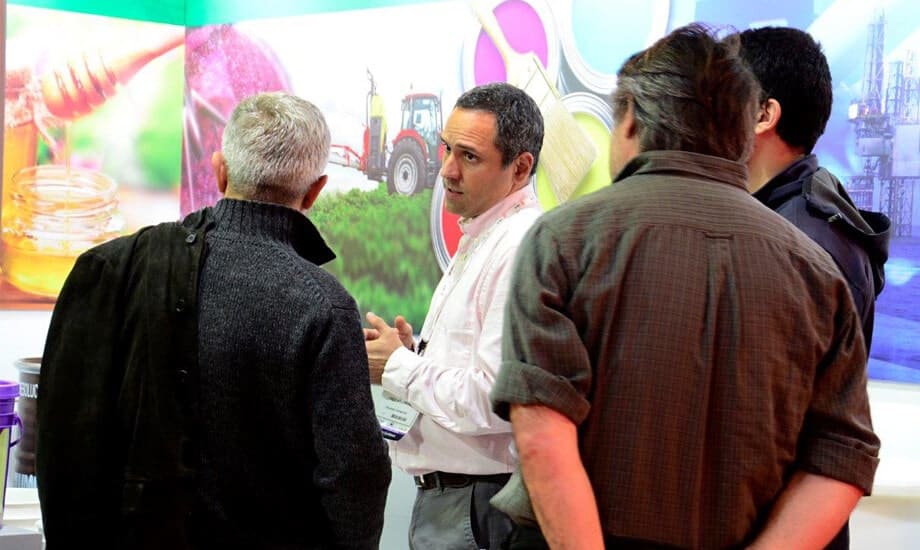
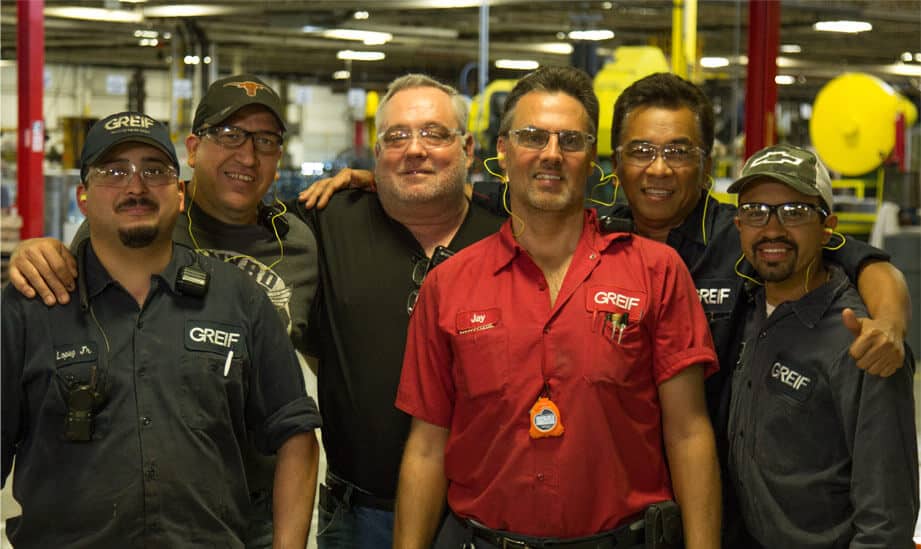
- RIPS Naperville, Illinois: 100%
- RIPS Mendig, Germany: 98%
- RIPS Cologne, Germany: 98%
- RIPS Lockport, Illinois: 98%
- FPS Sultanbeyli, Turkey: 98%
- RIPS Europoort, Netherlands: 97%
- RIPS Attendorn, Germany: 96%
- RIPS Usti, Czech Republic: 95%
- RIPS Campana, Argentina: 83%
- RIPS Shanghai, China: 80%