Why Waste Matters
Reducing our operational waste, waste to landfill and packaging waste is fundamental to our business. We work to establish closed loop and zero waste processes that support our circularity strategy and the transition to a more circular economy. Our waste reduction efforts add value throughout our supply chain by reducing emissions and environmental impacts, conserving valuable resources through lower material use and helping the communities we serve. We also provide value to our customers by providing lighter weight and more cost-effective products. Through our waste reduction efforts, we reduce emissions in our operations and contribute to addressing global environmental waste challenges.
Gobernancia
71%
of waste diverted from landfills
Our efforts to reduce waste are global, with each facility working towards our 2025 goal.
For all facilities, excluding legacy Caraustar facilities, we create a detailed waste matrix to help us understand each facility’s waste streams, each waste stream’s disposal method (recycling, reuse, landfilling, etc.) and manage progress. The waste matrices also serve as a collaboration tool allowing facilities to compare management of common waste streams. We are expanding collaboration between our facilities through monthly or quarterly town halls during which facility success stories and key learnings are shared with a wider audience across our Global Industrial Packaging (GIP) business. We are also improving collaboration and transparency with our waste collection partners supporting our continued waste management progress and our understanding of our waste streams at a more detailed level.
Management at each facility, excluding legacy Caraustar facilities, that has not yet reached our 2025 waste diversion target is responsible for creating a quarterly, or semi-annual, roadmaps to evaluate all waste streams going to landfill and develop a diversion strategy. Each facility includes at least the top three waste diversion projects and reports on associated cost reductions, waste to landfill reductions and the status of each project. Our waste diversion roadmaps provide great insight into our facilities and their waste management progress. For example, the Greif Hadımköy team in Turkey utilized their waste roadmap to assess their waste streams and reach their facility’s 90 percent waste diversion goal.
In 2018, Greif entered into a partnership with Operation Clean Sweep (OCS), an organization dedicated to keeping plastics out of the environment, to expand our commitment to reducing plastic waste. Through the partnership, we commit to conducting audits in our facilities to evaluate our plastic resin handling operations and implement good housekeeping and pellet, flake and powder containment practices. We have conducted audits at our Hazleton, Pennsylvania, Houston, Texas and Mt. Sterling, Kentucky locations and will resume conducting audits when able to do so safely in light of the COVID-19 pandemic.
In 2021, we will continue to integrate legacy Caraustar facilities into our waste management goals and construct a roadmap towards reaching our 2025 target. We are also evaluating the long-term and strategic impact of waste reduction to our business and our customers in support of establishing a new 2030 waste goal. We will continue to work with our customers to meet their sustainability goals.
Goals & Progress
In 2018, we created a goal to divert 90 percent of waste from landfills from all Greif production facilities globally by the end of fiscal year 2025. This year we began to include waste data from our legacy Caraustar facilities as well. Globally, we diverted 71 percent of waste from landfills in 2020.
Progress:
FY 2020* |
facilities with 90%+ Diversion |
facilIties with 99%+ Diversion |
facilIties with zero waste to landfill |
||
---|---|---|---|---|---|
Total |
109 |
45 |
39 |
||
América del norte |
38 |
8 |
5 |
||
Europe |
51 |
31 |
29 |
||
América Latina |
8 |
0 |
0 |
||
Asia Pacífico |
12 |
6 |
5 |
Actuación
WASTE STREAM
|
FY 2017 |
FY 2018 |
Año fiscal 2019 |
Año fiscal 2020 |
---|---|---|---|---|
Hazardous Waste |
|
|||
Total Waste to Landfill |
527 |
1,639 |
2,428 |
3,608 |
Waste to Landfill |
527 |
1,292 |
1,161 |
2,989 |
Incinerated (no energy recovery)**** |
- |
347 |
1,267 |
619 |
Total Non-Landfill* |
7,109 |
14,105 |
20,725 |
19,199 |
Incinerated (with energy recovery)** |
1,202 |
3,372 |
4,073 |
3,275 |
Composted*** |
- |
0 |
0 |
1 |
Recycled† |
2,011 |
7,604 |
14,084 |
14,160 |
Reused†† |
399 |
1,513 |
651 |
706 |
Reclaimed††† |
194 |
217 |
366 |
376 |
Miscellaneous (Non Landfill) †††† |
3,303 |
1,399 |
1,551 |
681 |
Total Hazardous Waste |
7,638 |
15,744 |
23,153 |
22,807 |
Non-Hazardous Waste |
|
|
||
Total Waste to Landfill |
57,403 |
54,594 |
33,837 |
137,211 |
Waste to Landfill |
57,403 |
54,110 |
33,380 |
137,066 |
Incinerated (no energy recovery)**** |
- |
485 |
457 |
151 |
Total Non-Landfill* |
161,796 |
257,219 |
184,357 |
326,546 |
Incinerated (with energy recovery)** |
945 |
2,054 |
2,950 |
17,006 |
Composted*** |
15,277 |
35 |
15,784 |
49,734 |
Recycled† |
111,861 |
231,997 |
141,217 |
212,075 |
Reused†† |
17,147 |
11,641 |
12,321 |
19,441 |
Reclaimed††† |
13,187 |
9,439 |
9,847 |
11,701 |
Miscellaneous (Non Landfill)†††† |
3,379 |
2,052 |
2,239 |
16,589 |
Total Non-Hazardous Waste |
219,199 |
311,813 |
218,194 |
463,757 |
Total Waste (Hazardous & Non-Hazardous) |
226,835 |
327,557 |
241,347 |
486,564 |
Notes:
- Legacy Caraustar facilities were incorporated into waste reporting in FY 2020.
*Non-Landfill: Includes chemical-physical, incineration with energy recovery, recycled, reused, reclaimed, composted and fuels blending treatment methods
**Incinerated (with energy recovery): Treatment method involving the combustion of solid waste that results in energy capture.
***Composted: Treatment method involving the biological decomposition of solid or liquid operational waste.
**** Incinerated (no energy recovery): Treatment method involving the combustion of solid waste that does not result in energy capture.
†Recycled: Treatment method involving the separation, preparation and sale of recyclable materials to end-user manufacturers.
††Reused: Treatment method involving the use of a material for its original purpose multiple times.
†††Reclaimed: Treatment method involving the process of extracting and converting materials from recycled materials to be used again.
†††† Miscellaneous (Non Landfill): All other treatment methods not mentioned previously, including Deep Well Injection and On-Site Storage, which were reported separately in 2017.
EARTHMINDED LIFE CYCLE SERVICES – ESTIMATED DRUMS AND IBCS RECONDITIONED*
|
FY 2016 |
FY 2017 |
Fy 2018
|
Año fiscal 2019
|
Año fiscal 2020
|
---|---|---|---|---|---|
Recycled |
1,045,093 |
904,883 |
849,498 |
831,576 |
968,296 |
Tambores de acero |
689,513 |
534,369 |
571,355 |
509,884 |
562,980 |
Poly Drums |
277,672 |
212,272 |
161,447 |
243,186 |
358,280 |
IBC (Contenedores a granel) |
77,908 |
158,242 |
116,696 |
78,506 |
47,036 |
Reconditioned |
3,808,242 |
3,218,885 |
3,258,848 |
3,533,358 |
3,276,259 |
Tambores de acero |
3,072,348 |
2,565,052 |
2,713,025 |
2,699,393 |
2,483,485 |
Poly Drums |
375,307 |
321,188 |
244,497 |
194,011 |
178,627 |
IBC (Contenedores a granel) |
360,587 |
332,645 |
301,326 |
639,954 |
614,147 |
Total Collected |
4,853,335 |
4,136,828 |
4,105,936 |
4,348,706 |
4,164,585 |
Tambores de acero |
3,761,861 |
3,099,633 |
3,284,380 |
3,193,049 |
2,971,549 |
Poly Drums |
652,979 |
535,460 |
405,944 |
437,197 |
536,281 |
IBC (Contenedores a granel) |
438,495 |
501,735 |
415,612 |
718,460 |
656,755 |
Virgin Materials Saved by Reconditioning and Reuse (Metric Tons)** |
71,573 |
63,111 |
63,587 |
76,415 |
71,149 |
Steel |
65,743 |
56,200 |
57,664 |
66,860 |
62,016 |
High-Density Polyethylene |
5,830 |
5,150 |
4,243 |
5,897 |
5,553 |
Wood |
1,761 |
1,680 |
3,659 |
3,580 |
|
Virgin Materials Saved by Recycling (Metric Tons)*** |
17,402 |
18,755 |
16,644 |
14,117 |
14,358 |
Steel |
13,288 |
13,463 |
12,697 |
10,273 |
10,215 |
High-Density Polyethylene |
3,817 |
4,580 |
3,385 |
3,402 |
3,871 |
Wood |
297 |
712 |
562 |
442 |
272 |
Notes:
- Virgin Materials Saved by Reconditioning and Reuse data has been restated to standardize units across regions.
**Estimates based on the quantity of reconditioned packaging and average packaging specifications (North America and Europe)
***Estimates based on the quantity of recycled packaging and average packaging specifications (North America and Europe)
REBU – ESTIMATED FIBCS RECONDITIONED (EMEA)*
|
FY 2017 |
FY 2018 |
Fy 2019 |
Año fiscal 2020 |
---|---|---|---|---|
Total FIBCs Collected | - | 316,324 |
275,732 |
242,000 |
Reconditioned |
- |
224,418 |
179,912 |
167,000 |
Recycled |
- |
91,906 |
95,820 |
75,000 |
Total Virgin Polyethylene Saved (Metric Tons)** |
- | 727.6 |
634.2 |
556.6 |
Virgin Polyethylene Saved by Reconditioning and Reuse (Metric Tons)**
|
- |
516.2 |
413.8 |
384.1 |
Virgin Polyethylene Saved by Recycling (Metric Tons)*** |
- |
211.4 |
220.4 |
172.5 |
**Estimates based on the quantity of reconditioned packaging and average packaging specifications (Europe)
***Estimates based on the quantity of recycled packaging and average packaging specifications (Europe)
Sawdust Waste Recycling in Omsk
In July 2020, Greif’s Global Industrial Packaging (GIP) facility in Omsk, Russia implemented an innovative means of reducing their wood waste to landfill by turning their sawdust into insulation. During the production of the Clovertainers the facility generates up to seven tons of sawdust annually which represented their largest source of waste and 39 percent of their waste that was being sent to landfill. To reduce their waste to landfill, the team began searching for recycling solutions for the sawdust and discovered they could process it into components for pallet production. Once processed, it can be sold to farmers for use as insulation for their livestock in the winter or to construction companies to be used as fuel. As a result, they have reduced their waste to landfill and realized cost savings.
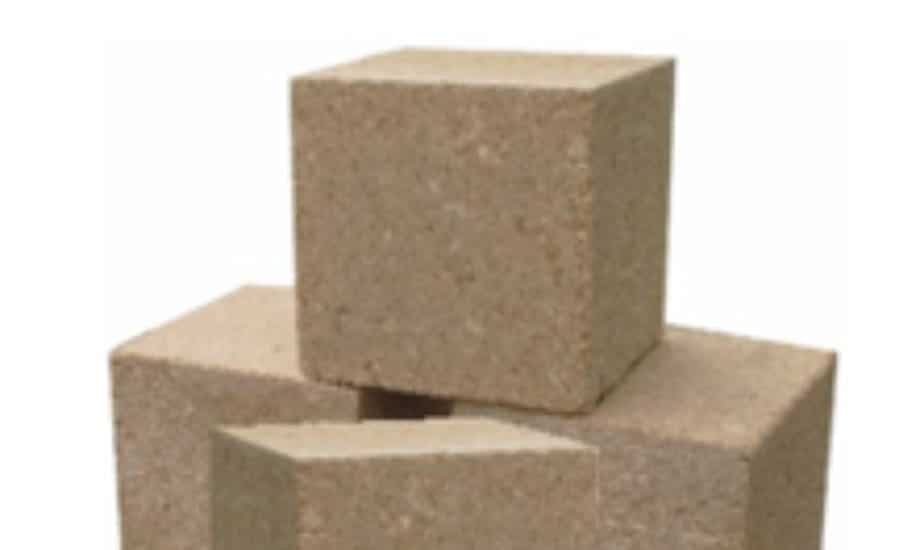
Turning Waste to Fuel
In 2019, Greif collaborated with one of our waste management partners to identify materials used in our operations that could enter their engineered fuels program, which aims to identify materials that have a high heat value such as plastics, oils and absorbents, that can be used as fuel in certain applications that require significant amounts of energy, such as cement kilns. Through this collaboration, polypropylene lids used on Greif’s fibre and plastic drums were identified as strong options to enter this program. Since these lids cannot be recycled, Greif’s Naperville, Illinois facility collected and palletized 3.3 tons of lids to enter into this program. Without this program, the lids would have been sent to landfill. This program is available to Greif North American facilities.
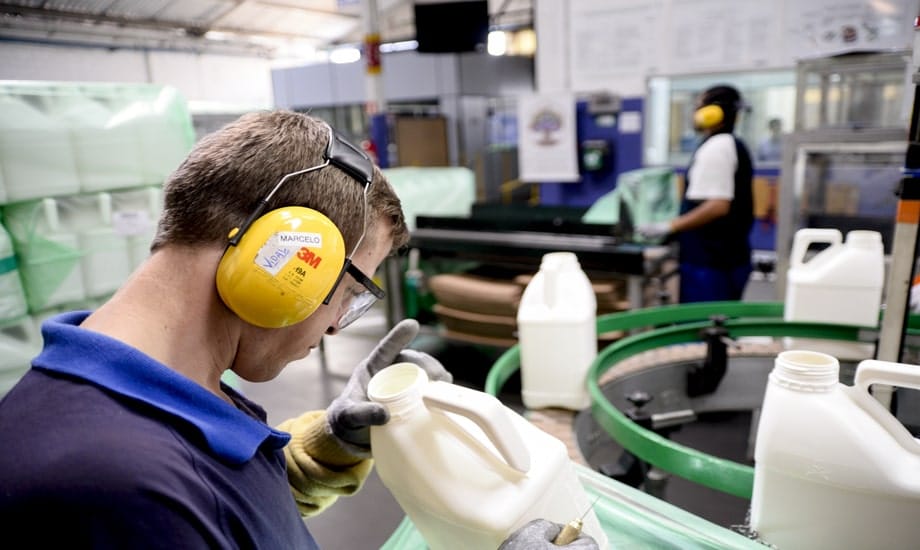
Greif Hadımköy Reaches and Exceeds 90 Percent Waste Diversion Target
During 2020, the Hadımköy team in Turkey developed a waste roadmap by assessing their waste streams and determining a path to reduce their waste going to the landfill. The Hadımköy team introduced separation bins for paper waste in production, separated leftover food waste and sent it to local animal shelters, and introduced separation bins for packaging and paper waste in the cafeteria. In total, these efforts led to a seven percent reduction in their waste to landfill. By the end of 2020, Hadımköy used the projects on their waste roadmap to further reduce their waste to landfill an additional five percent and already exceeded the corporate 2025 waste target.
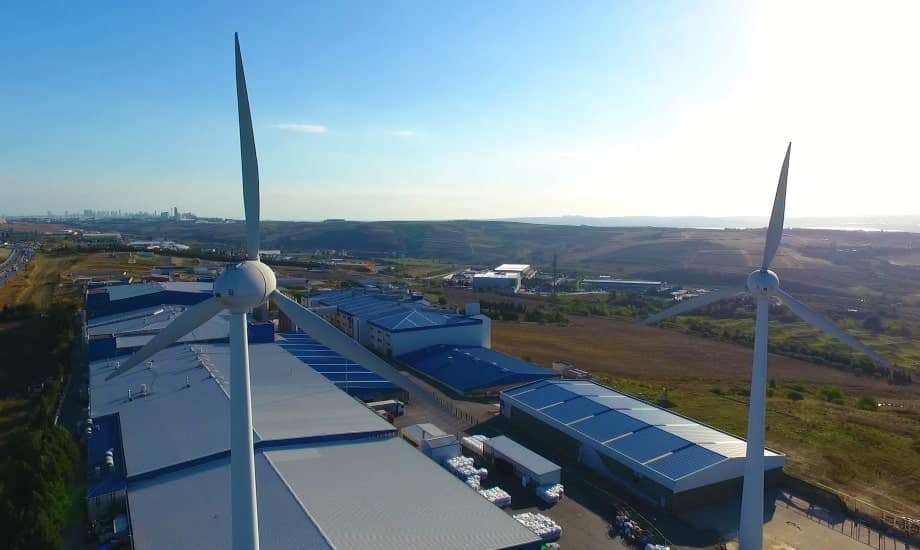
Reducing VOC’s Through Use of Water-Based Exterior Paints
Greif is committed to using water-based exterior paints in our operations where possible, rather than high volatile organic compound (VOC) exterior paints. In Global Industrial Packaging (GIP) North America, eight out of our nine steel plants use water based paints. In GIP China, the Greif Zhuhai plant has converted to 70 percent water-based paints and in 2020, they began testing the use of water based regular drum liners in our products to further reduce the VOC impact of our products.
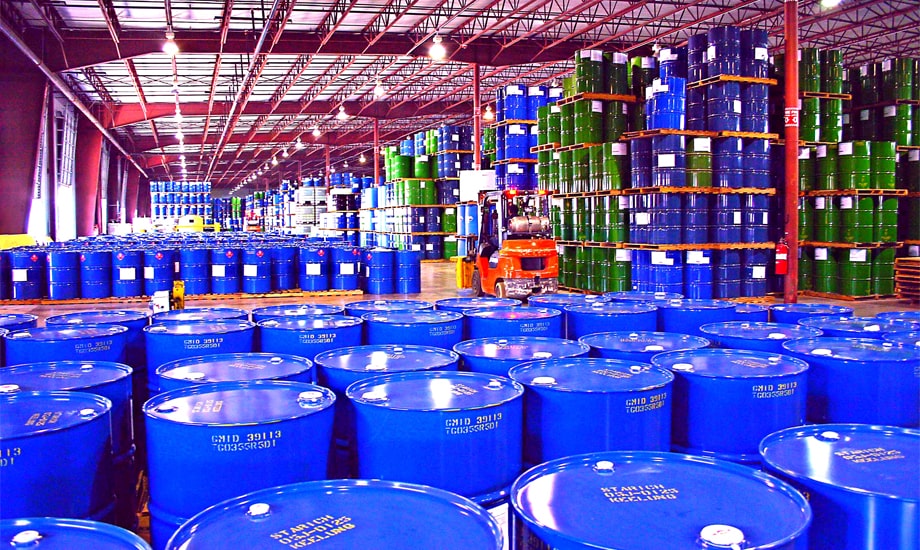
Achieving Waste Reduction through Customer Service Excellence
In 2019, Greif’s Global Industrial Packaging (GIP) facility in Sweden received a customer complaint that jerrycans were being damaged during unpacking because the plastic film used to wrap the pallets was too tight and difficult to remove. In response, the facility tested a number of film alternatives that were easier to remove and posed less risk of damaging the cans and ultimately selected an alternative that reduced the use of film by 48 percent, saving 7500 kg of materials annually. The transition also led to $12,000 USD savings and a 22,000 kg emission reduction. In order to scale the project, the team has updated the standard operating procedure for using similar films and have worked with our procurement team to update the supplier and material for the film.
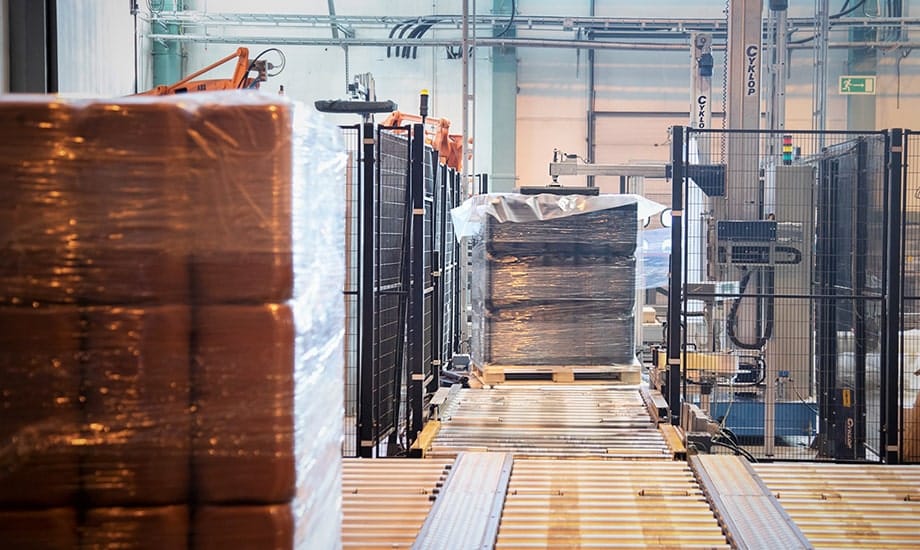
Greif Riyadh Reduces Waste by Addressing Wastewater
In 2017, Greif’s Global Industrial Packaging (GIP) facility in Riyadh, Saudi Arabia was the largest contributor of waste to landfill in the EMEA region with 36 percent of waste going to landfill. By analyzing their waste streams, the facility team determined that this was primarily due to wastewater that, if treated properly, could be recycled. Despite limited infrastructure support, availability of recycling partners and transportation options, the team established a process to internally separate and clean water to acceptable levels for local transporters and recyclers and consistently return water to them. Through these measures, the team reduced the oil content of the water from 60 ppm to 1.5 ppm and decreased their waste-to-landfill to four percent by the end of 2019. Due to Saudi Arabia’s own water scarcity, the impact of this initiative goes far beyond Greif’s operations. Through initiatives like this Greif has the ability to set a precedent for other businesses to follow and ultimately benefit the local community.
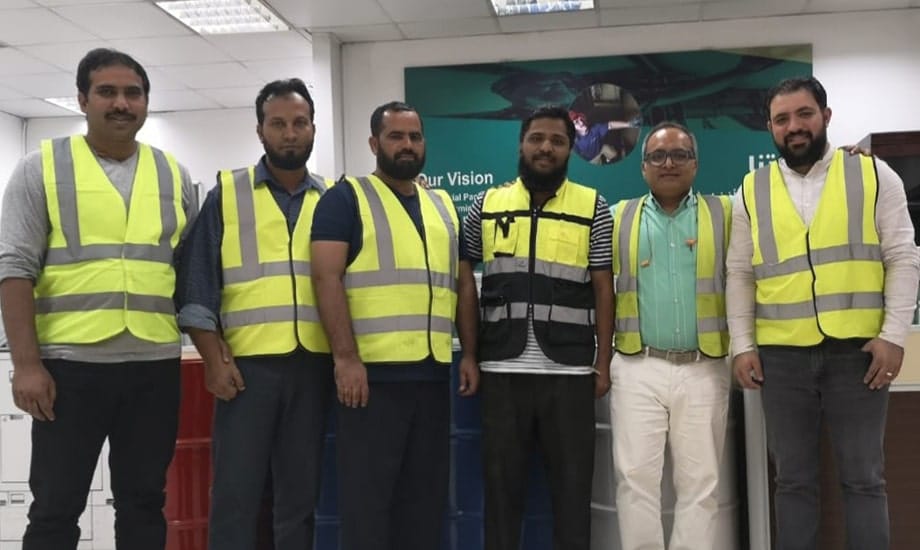
Removing Solvents in IBC Printing
Greif’s Global Industrial Packaging (GIP) facility in Falkenberg, Sweden implemented an innovative printing process for intermediate bulk containers (IBCs) that reduces waste, eliminates the use of solvents in printing and generates efficiencies in the manufacturing process. By replacing traditional ink jet printing with laser engraving to mark IBCs, the team has eliminated ink-based solvents from the manufacturing process and the need to change printing plates between production runs, creating a more efficient facility, and reduce the amount of resin required by 6.7 percent. In total, this change will lead to $50,000 annual savings and can easily be implemented in other Greif facilities.
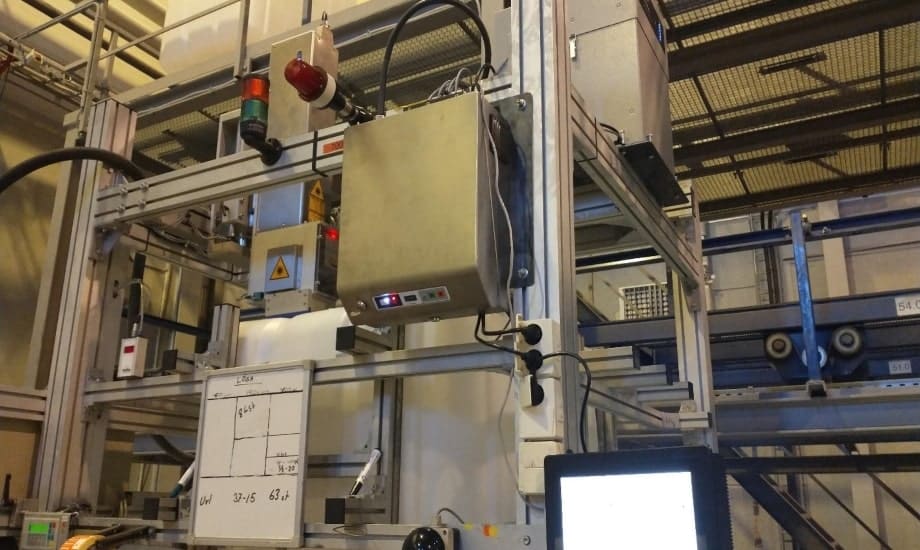
SUSTAINABILITY HIGHLIGHTS
71%
Of waste diverted from landfills
Our efforts to reduce waste are global, with each facility working towards our 2025 goal.