Why Cradle to Cradle Manufacturing, Reconditioning, Reuse & Recycling Matters
Greif actively manages the life cycle of industrial packaging through manufacturing, reconditioning, reuse and recycling to advance circular economy principles. We work with our customers, and even their customers, to produce new packages and products that build economic, environmental and social capital. Our Circular Economy management through manufacturing, reconditioning, reuse and recycling solutions helps divert waste from landfills while strengthening relationships within our supply chain. As the demand for sustainable solutions increases, our collaborative efforts with our suppliers and our customers enable us all to reach our collective sustainability goals.
Gobernancia
Containers that are collected throughout our network are reconditioned so they are suitable for reuse and then reintroduced into trade. The reconditioned containers reduce the demand for new containers and demand for virgin raw materials, while decreasing the number of containers that go to landfill. If a container cannot be reconditioned, the materials are recycled for use into other products. Many of Greif’s largest customers use our LCS network to recondition their containers. Customers who use the network can access real-time reports through the Greif Green Tool, which enables customers to quantify performance by tracking key indicators like carbon impact and weight of reused and recycled materials. Across Global Industrial Packaging, we reconditioned, remanufactured, or recycled more than 4.5 million containers and our Paper & Packaging Services (PPS) business managed over 3.4 million metric tons of recycled paper in 2020.
Greif Recycling Operations
Greif Recycling Operations
71,149
Metric Tons of Virgin Materials Saved
Our reconditioning and reuse operations helped us remove over 70,000 metric tons of virgin steel, high-density polyethylene and wood from our supply chain in 2020.
In addition to our reconditioning operations, Greif operates 18 recycling facilities in our Paper Packaging & Services (PPS) business. Through these facilities, we offer complete outsourcing solutions for plastics, pulp and paper fiber procurement, transportation and administration and provide complete paper fiber audit and management solutions. 98 percent of the products we handle, by volume, are paper fiber. Our paper fiber recycling operations collect waste paper for use in our own containerboard mills and for sale to other containerboard and recycled paper product manufacturers. Because of our integrated capabilities, Greif holds a central position in the paper recycling industry and operates as a net positive recycler. Approximately 50 percent of the fiber we collect is used in our own operations to manufacture paper products for use in consumer and industrial settings. The remaining 50 percent of the fiber we collect is sold to external mills and other manufacturing operations for use in the production of new paperboard, molded fiber packaging and other products. Over 90 percent of the fiber we use in our paper manufacturing is from purely recycled inputs.
We are proud to be able to offer services that enable the re-use of fiber. Recovered fiber is an input to many essential goods but has suffered from reductions in supply through the economic closures caused by the global COVID-19 pandemic. Prior to COVID-19, recovered fiber value was at historical lows with the cost of recovery greater than the fiber value for many recyclers. Today the critical importance of expanding access to recycling is clear, particularly as more commerce takes place at the home instead of in stores. Through our sales force and participation in various industry groups, we are doing our part to educate the market on the dynamics of the changing industry to ensure this remains a viable business with a robust supply chain for all the essential goods that depend on recovered fiber inputs.
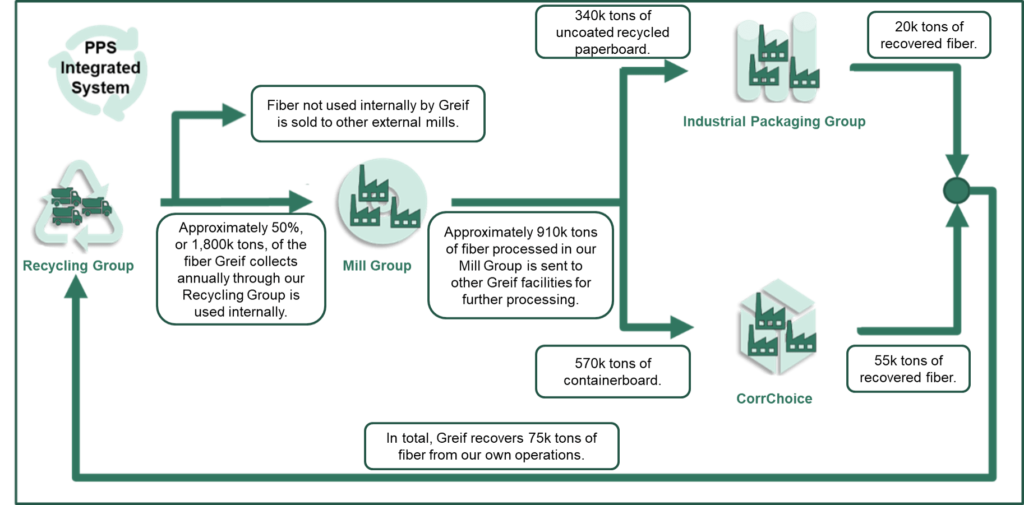
Global Industrial Packaging
In our Global Industrial Packaging (GIP) business, we look for reuse and recycling opportunities wherever possible. All our plastic products globally are 100 percent recyclable and 100 percent of our internal regrind plastic, which accounts for approximately 20 percent of our drums and IBCs, is reincorporated into our products. Our steel products are made from a minimum of 15 percent recycled steel globally and a minimum of 33 percent recycled steel in North America. We recycle 90 percent of our internal scrap used to produce our flexible products and the balance is sold to recycling companies. There is approximately seven percent recycled plastics (internal scrap) in our FPS plastics products.
Cradle to cradle and the use of recycled products are just two components of our circular economy strategy that span across our operations and value chain. As part of that strategy, we are working to drive circular economy principles in five key areas:
- Reducing raw material use
- Waste reduction and reducing natural resource use
- Innovation and increasing recyclability, and use of recycled materials, in our products
- Fiber-based alternatives to single-use plastics
- Life cycle services
In 2020, EarthMinded LCS introduced new terms for containers acceptable for reconditioning including requirements for containers that previously contained substances that can emit flammable gasses when in contact with water, requirements for all packaging to be fully closed upon acceptance, and stricter requirements for what constitutes an empty container. Collectively, these terms help us ensure our operations remain in compliance with relevant regulations and provide for better health and safety of our colleagues and those in the communities in which we operate. In 2020, Greif expanded its IBC, drum and jerrycan recollection capabilities in Italy by establishing a joint venture with LAF s.r.l., a leader in reconditioning services. In addition to reconditioning, LAF s.r.l. transforms HDPE components into raw secondary materials that are used in industry, building, furniture, and flooring.
In 2021, we will continue to expand our reconditioning services. In Spain, we will establish new joint ventures that will allow us to recondition more drums and IBCs. In our PPS business, we place greater emphasis on our fiber business to identify solutions that will be valuable to our customers and work to bring them to life.
Actuación
EARTHMINDED LIFE CYCLE SERVICES – ESTIMATED DRUMS AND IBCS RECONDITIONED*
REBU – ESTIMATED FLEXIBLE INTERMEDIATE BULK CONTAINERS (FIBCS) RECONDITIONED EUROPE, MIDDLE EAST AND AFRICA
|
FY 2016 |
FY 2017 |
FY 2018
|
Año fiscal 2019
|
Año fiscal 2020
|
---|---|---|---|---|---|
Recycled |
1,045,093 |
904,883 |
849,498 |
831,576 |
968,296 |
Tambores de acero |
689,513 |
534,369 |
571,355 |
509,884 |
562,980 |
Poly Drums |
277,672 |
212,272 |
161,447 |
243,186 |
358,280 |
IBC (Contenedores a granel) |
77,908 |
158,242 |
116,696 |
78,506 |
47,036 |
Reconditioned |
3,808,242 |
3,218,885 |
3,258,848 |
3,533,358 |
3,276,259 |
Tambores de acero |
3,072,348 |
2,565,052 |
2,713,025 |
2,699,393 |
2,483,485 |
Poly Drums |
375,307 |
321,188 |
244,497 |
194,011 |
178,627 |
IBC (Contenedores a granel) |
360,587 |
332,645 |
301,326 |
639,954 |
614,147 |
Total Collected |
4,853,335 |
4,136,828 |
4,105,936 |
4,348,706 |
4,164,585 |
Tambores de acero |
3,761,861 |
3,099,633 |
3,284,380 |
3,193,049 |
2,971,549 |
Poly Drums |
652,979 |
535,460 |
405,944 |
437,197 |
536,281 |
IBC (Contenedores a granel) |
438,495 |
501,735 |
415,612 |
718,460 |
656,755 |
Virgin Materials Saved by Reconditioning and Reuse (Metric Tons)** |
71,573 |
63,111 |
63,587 |
76,415 |
71,149 |
Steel |
65,743 |
56,200 |
57,664 |
66,860 |
62,016 |
High-Density Polyethylene |
5,830 |
5,150 |
4,243 |
5,897 |
5,553 |
Wood |
1,761 |
1,680 |
3,659 |
3,580 | |
Virgin Materials Saved by Recycling (Metric Tons)*** |
17,402 |
18,755 |
16,644 |
14,117 |
14,358 |
Steel |
13,288 |
13,463 |
12,697 |
10,273 |
10,215 |
High-Density Polyethylene |
3,817 |
4,580 |
3,385 |
3,402 |
3,871 |
Wood |
297 |
712 |
562 |
442 |
2720 |
**Estimates based on the quantity of reconditioned packaging and average packaging specifications (North America and Europe)
***Estimates based on the quantity of recycled packaging and average packaging specifications (North America and Europe)
|
FY 2016 |
FY 2017 |
Fy 2018 |
Año fiscal 2019 |
Año fiscal 2020 |
---|---|---|---|---|---|
Total FIBCs Collected | - | - |
316,324 |
275,732 |
242,000 |
Reconditioned |
- |
- |
224,418 |
179,912 |
167,000 |
Recycled |
- |
- |
91,906 |
95,820 |
75,000 |
Total Virgin Polyethylene Saved (Metric Tons) |
727.6 |
634.2
|
556.6
|
||
Virgin Polyethylene Saved by Reconditioning and Reuse (Metric Tons)*
|
- |
- |
516.2 |
413.8 |
384.1 |
Virgin Polyethylene Saved by Recycling (Metric Tons)** |
- |
- |
211.4 |
220.4 |
172.5 |
**Estimates based on the quantity of recycled packaging and average packaging specifications (Europe)
Maintaining Our Commitments Through Natural Disasters
In 2017, Greif’s North American operations were hit by hurricanes Harvey and Irma, resulting in a roughly $5 million of impact to our business. Despite the impact, our risk management and business continuity practices allowed us to meet our customer commitments during recovery without declaring force majeure. Greif supported our colleagues directly impacted by the hurricanes by continuing to pay wages during the week production was down, paying for hotels and rental cars and setting up a Wish List for colleagues in North America to purchase items for their peers. Greif also matched colleague cash donations to the Red Cross to support relief efforts, donating a match of $11,745.
In 2020, hurricanes moving through the Gulf of Mexico impacted the Mobile Recycling, Bay Minnette and Woodbine Paper Packaging & Services (PPS) plants and a derecho impacted our Tama, Iowa Mill. In all cases, we worked to supply customers through capacity at other locations as plants faced downtime of one-half to two days depending on the event. Our business continuity plans ensured the downtime resulted in no lost business and we delivered on our promises to our customers.
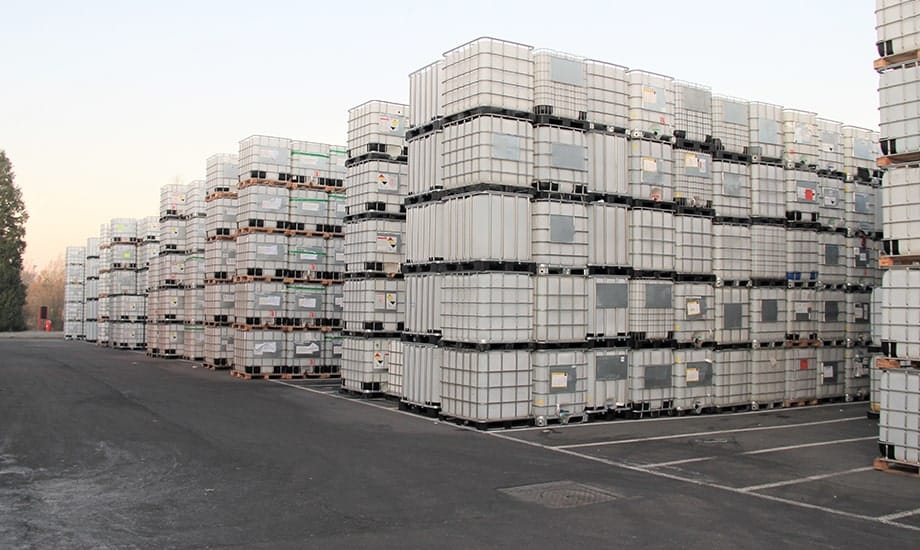
Greif Takes Majority Share in Tholu
In 2019, Greif signed an agreement to acquire a majority share in the Tholu group, a Netherlands-based market leader in IBC rebottling, reconditioning and distribution. Tholu implements a variety of high-speed, state-of-the-art, closed looped systems to recondition IBCs to a high level of reconditioning that is suitable to use to store and transport a wide variety of products. All IBCs collected by the facility are collected as waste under government regulation. All IBCs that are collected by the facility are either cleaned and returned to use or processed to be used in alternate products. Greif’s investment in Tholu helps us to strengthen our footprint in the overall IBC market in Northwestern Europe. A family-owned business, Tholu has been buying Greif produced IBCs in Ede, Netherlands since 2016 through a joint-venture agreement. Tholu reported $45.2 million in revenue in 2018. The new venture is known as Greif Tholu and operates under current Tholu management.
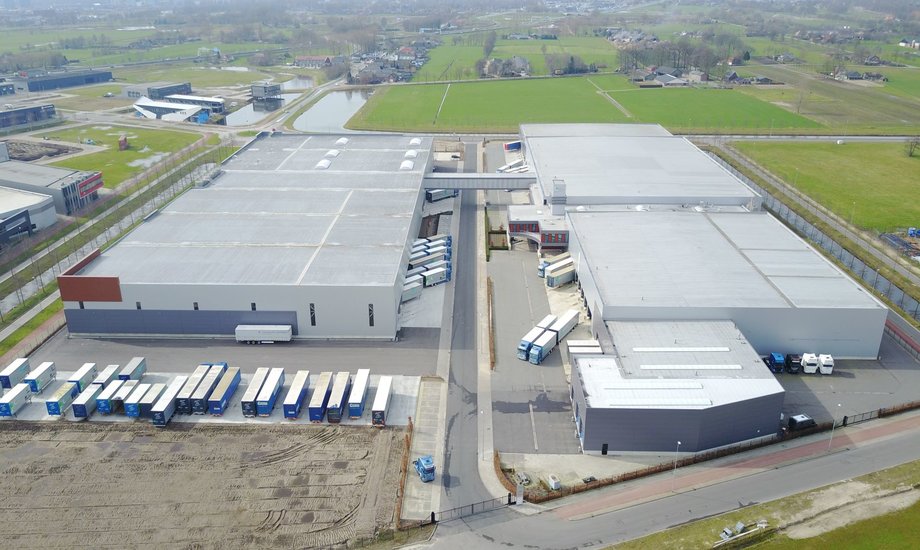
Using Recycled Plastic in IBC Molding
Greif’s Tri-Sure facility in Carol Stream collaborated with GIP North America purchasing, GIP Italy and four GIP NA plants to source 800,000 pounds of recycled plastic resins to use in the production of IBC rear/corner feet and corner protectors. This internal sourcing strategy reduced costs by $100,000. The team also reused empty corrugated bulk boxes to ship the recycled products they manufacture, reducing corrugated bulk box purchases by 84 percent. The project created company value and established environmental and financial benefits, while closing two internal loop systems and contributing to circular economy principles by diverting waste from landfills and finding a new purpose for them. Due to the outstanding sustainability impact of the project and its ability to be scaled to other molding and injection molding facilities, the project and Tri-Sure Carol Stream team was awarded the 2019 Michael J. Gasser Sustainability Award.
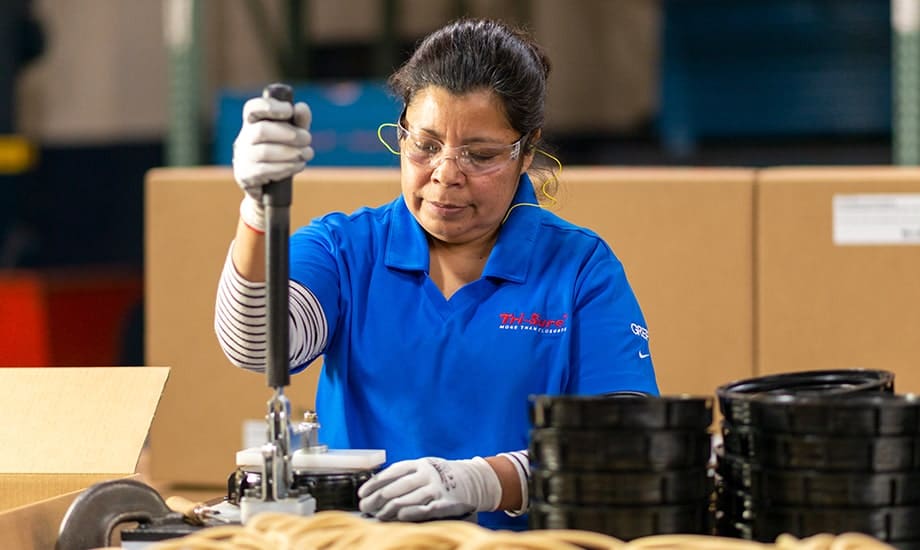
Fiber Recycling for the Flooring Industry
n 2020, our Dalton, Georgia Recycling Facility worked with the floor covering manufacturers in the Dalton area to process recovered fiber and create a “closed loop” for paperboard cores. Each year, the Dalton Recycling team recovers tens of thousands of tons of core waste from these manufacturers and recovers this waste fiber. This same fiber is used by Greif’s paper mills to manufacture 100 percent recycled new paperboard, which is then converted into new tubes and cores in Greif’s Industrial Products Group (IPG). This initiative helps not only sustain the recycling programs in Dalton but also maintain our level of excellent customer service with IPG customers. Annually, this program helps recycle 25,000 tons of cores, 10,000 tons of cardboard, 5,000 tons of boxboard, and 2,000 tons of plastic film from the flooring industry in North Georgia.
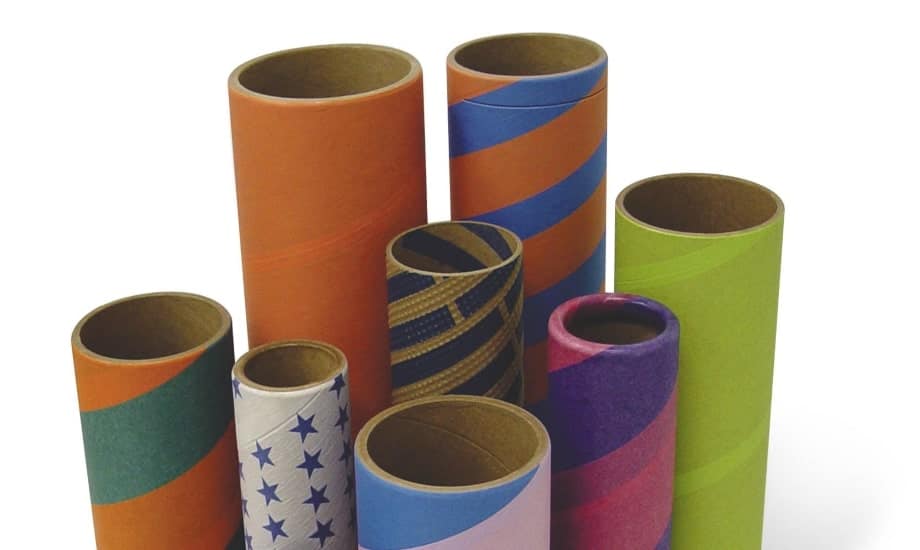
Reconditioning Conical Drums in Portugal
For the past 20 years Greif’s RIPS facility in Iberia, Portugal has been supplying customers with reconditioned conical drums, having reconditioned over 10 million drums and saving 50,000 tons of steel, 197,600 tonnes of CO2 emissions, 2,600,000 gigajoules of energy, and 343,200 cubic meters of water in the process. The project was initially started as a way to help address our customers’ wish to reduce waste and lower their carbon footprint and overall improve customer satisfaction. The team collaborated with customers to understand their needs, including volume, specification requirements and safety, developed a reconditioning process, and ultimately installed a reconditioning line to begin serving customers. Today, the facility serves a multitude of customers, reconditioning 500,000 conical drums and saving 5,200 tons of steel each year.
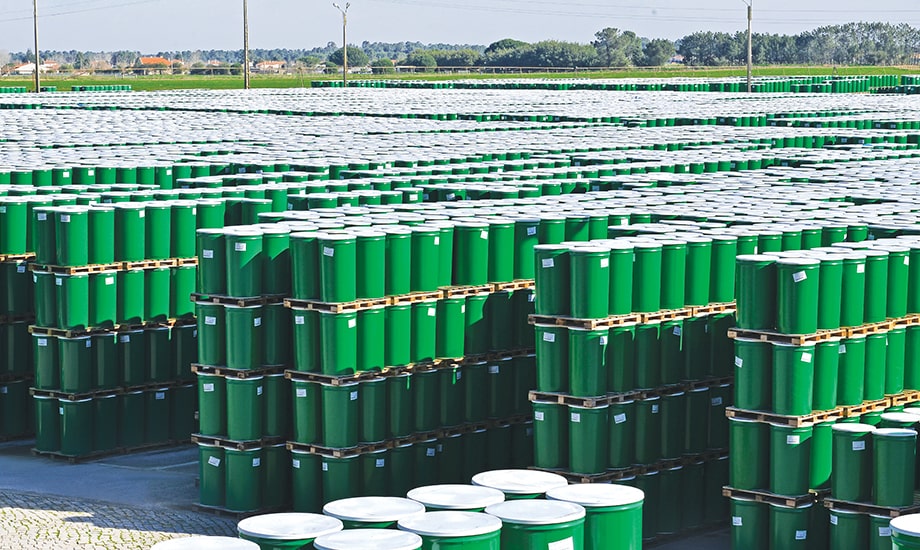
Life Cycle Assessments
Life cycle assessments (LCAs) are key to Greif’s innovation process. LCA is a technique that evaluates the environmental impact of products over their entire lifetime including raw material extraction, manufacturing, transportation, distribution, use and disposal or recycling. This information helps us understand the overall environmental profile of our existing products, where and how our impacts occur, target improvements in materials and products, and to prioritize analysis of processes, components and materials that have the greatest environmental impact. In the mid-2000s, we began using LCA to evaluate our entire product portfolio to assess our products’ overall environmental impact and identify steps in the cycle where a sustainable improvement can have the most positive impact. We learned that material mass is strongly linked to the environmental performance of most industrial packaging. This finding led us to focus on lightweighting our products, including the NexDRUM®, contributing to reduced emissions and environmental impact in our supply chain. LCAs also showed that extending product life has a greater impact on the environmental profile of our businesses than transportation of our products. Based on this knowledge, we launched EarthMinded Life Cycle Services, to recondition, refurbish and recycle used drums, extending the life of our products and fulfilling a critical need for our customers.
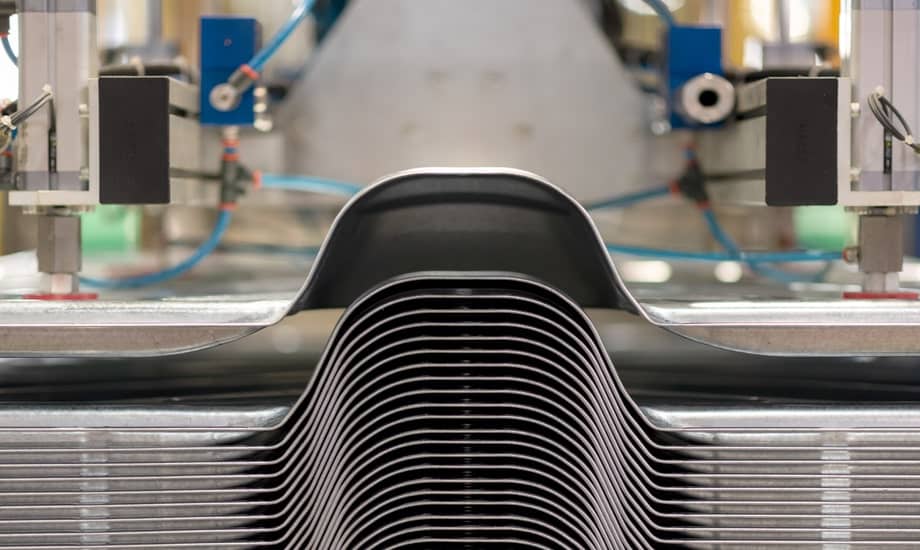
Expanding Cradle to Cradle Services with Investments and Joint Ventures
In 2020, Greif made investments and established multiple joint ventures in order to expand the scale and capabilities of the reuse, recycling and reconditioning services we provide. In April, Greif acquired a minority stake in Centurion Container LLC, expanding our intermediate bulk container (IBC) reconditioning network in North America. In August, Greif established a joint venture with Delta Plastics, the leading independent supplier of reconditioned IBCs in the United Kingdom. Finally, in December, Greif acquired a minority stake in LAF s.r.l., expanding IBC reconditioning services for our Italy-based customers. We look forward to working with our partners to continue to reduce our environmental impact through cradle to cradle solutions.
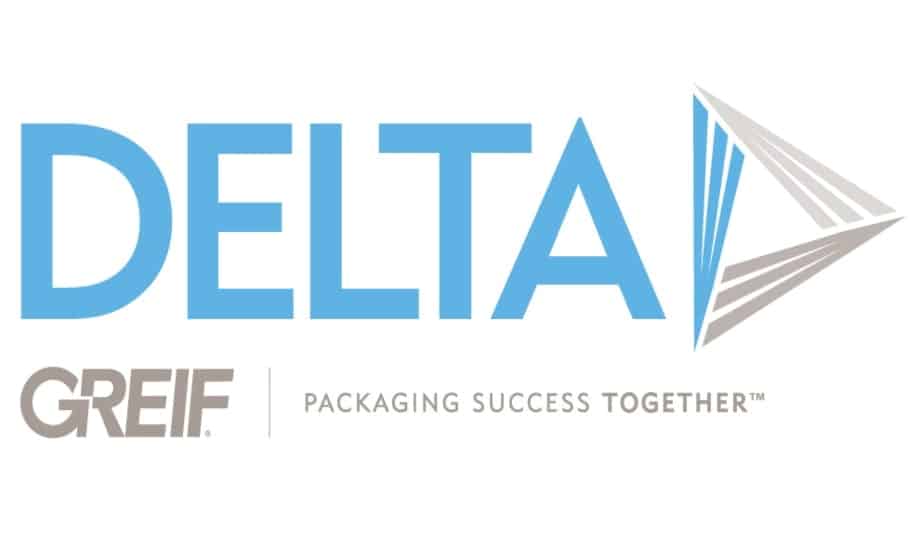