- Sustainability at Greif
- Estrategias de sostenibilidad
- Metas y desempeño
- Índices de informes ESG
- Descargas de informes
Reflejos
- Greif Business System (GBS) 2.0 drives best-in-class execution globally. Through operational excellence and quality management, we strive to produce high-quality, defect-free products that meet demanding customer specifications.
- Our Global Operations Group (GOG) aligns our product quality strategy objectives and approaches globally through our Política global de calidad de productos.
- Product and quality excellence are at the core of Delivering Legendary Customer Service. Through creative solutions, innovations, and fostering close customer relationships, we set our path to success and continuous improvement.
- We achieved a global Corrective Action Rate (CAR) of 1.0 in FY 2024.
Por qué es importante la calidad del producto
Product quality is the foundation of Greif’s business and achieving our strategic mission of Delivering Legendary Customer Service. We aim to be the supplier of choice by creating customer value, earning trust, and incorporating best practices. Through operational excellence and continuous improvement, we are standardizing our processes, designing innovative product solutions, and producing safe, reliable, high-quality products. GBS 2.0 drives our best-in-class execution, capable of meeting challenging industry and regulatory standards and specifications. We prioritize product quality across all business units and strive to consistently improve our standards and efforts.
We create packaging solutions for life’s essentials. Our commitment to high-quality products is vital to protecting the safety of our customers’ products, their employees, consumers, and the environment.
Our Approach
At Greif, we uphold consistent product quality standards through our Política global de calidad de productos. Aligned with our vision, purpose, and Build to Last Strategy, this policy establishes our commitment to a consistent standard and approach and outlines our processes to achieve our product quality expectations for Greif colleagues. Our Global Product Quality Policy demonstrates that our product standards are uncompromised and underpins our quality management system through business operations.
Our Quality Management Program includes Greif’s Top-Level Management Commitment, which defines how Greif collaborates with stakeholders and maintains regulatory compliance. We must maintain compliance globally, across diverse regulatory landscapes and operational contexts. Our dedicated team reviews procedures, distinguishing between global, business unit-specific, and regional regulatory considerations. Potential quality issues and risks uncovered during regulatory review are reported with documented corrective procedures through appropriate channels using our integrated quality management system, Greif QS.
We assess our quality performance using our Quality Management System scorecard. The scorecard generates organizational health reports and tracks events across business processes. Reports include customer complaints, internal corrective actions, management reviews, and supplier evaluations.
Greif QS houses a suite of applications that support quality and consistency in our products and processes across our production facilities. Examples of these applications include:
- Sistemas de respuesta a quejas y acciones correctivas
- Sistemas de acciones correctivas y preventivas internas
- Sistema de Gestión de Auditoría
- Sistemas de calibración
- Sistemas de gestión de proveedores
- Sistema de revisión por la dirección
- Sistemas de gestión de documentos y formación
- Sistema de Gestión de Cumplimiento
Sistema de gestión empresarial Greif 2.0
To strengthen our control over manufacturing and operational processes, we leverage our Greif Business System 2.0 (GBS 2.0), which provides our teams with tools and processes to identify and correct product deviations. This system works proactively, alerting teams before product deviations can affect production or customers. Additionally, GBS 2.0 establishes uniform methods and approaches in scale, shape and size, maintaining consistency across our products.
We strive to continuously improve GBS 2.0 by assessing gaps and expanding the tool’s applications. The Global Regulatory Steering Committee prioritizes improvements based on global product quality performance benefits. Integrating ERP with GBS 2.0 at the item level enhances material transparency, linking certification from raw materials to finished goods.
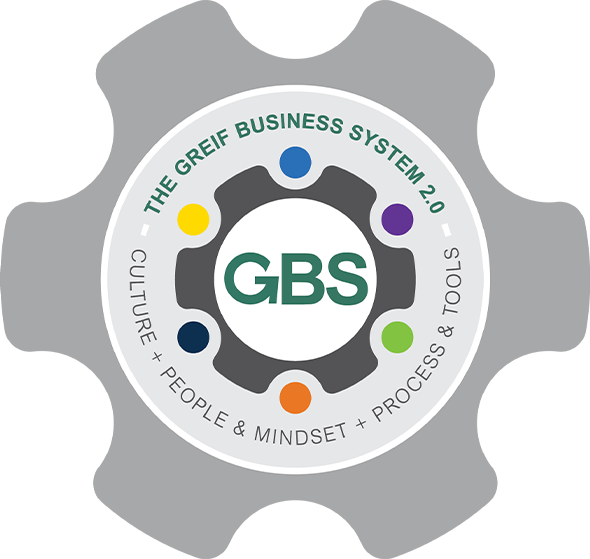
To meet customer specifications, certain products must comply with industry or regulatory standards. Where appropriate, we aim to comply with various material requirements, including the European Union’s (EU’s) Registration, Evaluation, Authorisation and Restriction of Chemicals (REACH) regulation, Restriction of Hazardous Substances Directive (RoHS), and Commission Regulation No 20/2011 (EU20/2011); California’s Proposition List 65 (Prop 65); and various U.S. Food and Drug Administration (FDA) rules.
As a part of our Back-to-Basics workstream, we launched a Visual Quality System (VQS), designed to enhance our product quality processes. In coordination with the VQS, we require foundational training for colleagues handling steel, fiber, and intermediate bulk containers to maintain visual quality standards at critical workstations. Furthermore, to facilitate compliance and prompt customer notification, we use our Management of Change (MOC) tool within Greif QS. The MOC categorizes changes in raw materials, processes, suppliers, and other indicators that may affect product quality and safety. Our MOC assesses change severity, initiates a review process, and communicates approved changes across all Greif functions.
We evaluate critical raw materials using our integrated ERP system and Quality Management System applications. Through these processes, we evaluate raw materials against the most current regulations and standards. In the unlikely event non-compliant raw materials are used, our systems will prevent the creation of a declaration for the applicable regulation or standard. We also create critical control plans for each substrate by analyzing data from internal and external sources including complaints, internal corrective actions, audit findings, and defect records.
Greif’s Technical Information System manages product material and safety information. Colleagues refer to Safety Data Sheets and chemical databases to monitor compliance with internal and external regulations prior to purchasing products. The Supplier Raw Material System (RMS), an application in Greif QS, evaluates raw materials and components for compliance with product declaration articles and regulations. For instance, regulatory requirements set out by the FDA or EU10/2011 require we declare the absence of certain substances in our products for the regulatory bodies to assess and document potential risks related to customer health and safety compliance. We expanded RMS globally in 2024, connecting our finished products to raw materials so we can consistently provide product declarations. Product declarations are our guarantee to customers that the package is safe.
We also monitor and take appropriate measures to avoid products listed in The REACH Candidate List of substances of very high concern (SVHC). In addition, we work to identify and introduce alternative substances and extend this expertise to customers. We offer Safety Data Sheets, packaging advice, and information on products to support responsible packaging choices.
Each year, we enhance and refine our approach to product food-safety to safeguard customer health and meet the requirements of the good manufacturing practice (GMP) program. Our ISO/GMP system seamlessly integrates food safety requirements into our manufacturing processes company wide. To align with growing customer and regulatory demand, we expanded our food safety certification system. We certified thirteen of our locations in North America with the Global Food Safety Initiative, an international effort that benchmarks and harmonizes various food safety standards.
Our CorrChoice facilities, which make corrugated and box products, conduct testing and real-time data collection for product quality. In the performance labs, we test raw materials to provide consistency in our finished products. All of our labs are operated by certified test technicians and outfitted with standardized equipment. The labs facilitate collaboration with customers to assess material combinations and performance and determine cost-effective product specifications.
Leveraging GBS 2.0 to Drive Improved Customer Satisfaction
We partnered with our customers to balance sustainable product development and complaint management. We apply the principles of our Greif Lean Six Sigma Program to drive well-defined projects. Using the A3 Define-Measure-Analyze-Improve-Control process, we focused on improving product quality, customer service, collaboration, and complaint management. As part of our GBS 2.0 evolution, we are focused on market excellence through targeted go-to-market strategies and enhanced sales effectiveness through processes, governance, and digital enablement. Together, we are driving operational excellence by aligning Lean Six Sigma projects with high value opportunities that improve mission critical KPI’s and globally scale our best practices. This end-to-end approach builds improved customer relationships and differentiation through equal emphasis on People, Mindset, and Culture.
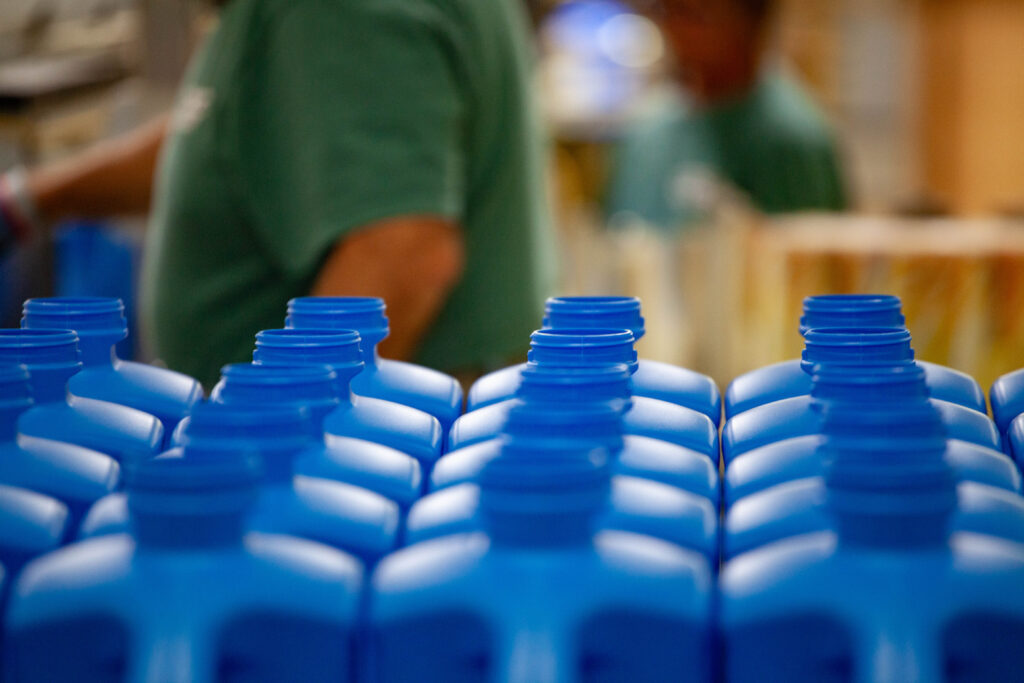
Greif is dedicated to fostering a culture of safety and accountability. This requires involvement from every colleague. Our Commitment-Based Safety/Quality (CBS/Q) program encourages best practice sharing through daily dialogues about product quality and safety. In 2024, we expanded this initiative to reach our colleagues at all levels of the organization. Learn more about our CBS/Q program in our Salud y seguridad sección.
Goals, Progress, & Performance
We develop product quality roadmaps with detailed plans for short-term initiatives and three-year plans for focus initiatives. Roadmaps are reviewed annually by GOG leadership. Initiative outcomes are a component of individual and team performance goals that help Greif improve on our overall performance metrics. Our product quality efforts collectively aid in our continuous improvement of customer priority areas: product integrity, on-time delivery, contaminants, and aesthetic quality.
In 2024, Greif launched several initiatives to enhance product quality and safety. We implemented a high-level global United Nations governance program to track all relevant certificates and implement validation programs. We launched this program in the U.S. and will expand to Mexico and Latin America in 2025. In our roadmap, we include a focus on engaging colleagues in product quality through World Quality Day and other development opportunities.
Por favor vea el Excelencia en el servicio al cliente section to learn more about how we are enhancing our complaint handling process, our online customer digital platform, Greif+, and One Greif approach to learn more about our approach to meet and exceed customer expectations.
TASA DE ACCIÓN CORRECTIVA 1
Gestión de calidad en tiempo real
Las instalaciones CorrChoice de IGreif, parte de nuestro negocio de Servicios y Empaques de Papel (PPS), han implementado un conjunto de herramientas que nos permiten monitorear y corregir posibles problemas de calidad en tiempo real. Las herramientas establecen alertas para una variedad de factores que pueden afectar la calidad, como la temperatura y la capacidad de almacenamiento de material, y corrigen cualquier desviación antes de que se salga de las especificaciones. Esta capacidad nos permite reducir el desperdicio, rastrear posibles desviaciones recurrentes y evitar tiradas largas de productos que no cumplirían las expectativas del cliente. Como parte de nuestro Sistema de Cero Defectos, nuestras líneas de producción están equipadas con sensores ultrasónicos capaces de detectar cualquier separación o variación que pueda ocurrir durante el proceso de fabricación, como diferencias en el espaciado de los calibradores y en los pesos del papel. El sistema rastrea los defectos a medida que avanzan por la línea de producción, eliminando los productos defectuosos y reciclando los desechos.
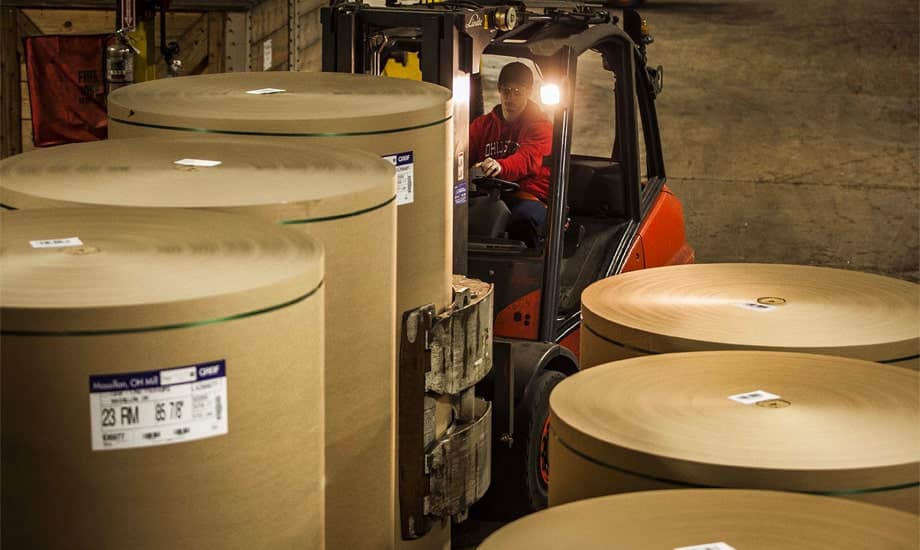