- Acerca de nuestra empresa
- Acerca de nuestro informe
- Estrategias de sostenibilidad
- Metas y desempeño
- Índices de informes ESG
- Descargas de informes
Reflejos
- Water is a critical resource, and Greif pledges to protect it for the benefit of future generations and the well-being of the communities where we live and operate. Through our commitment to increasing water quality, we treat water discharged from our facilities, so it is healthy and safe for wildlife and our communities.
- Our water management efforts focus on water use reduction in our Paper Packaging and Services business and stormwater management in our Global Industrial Packaging business.
- We continue standardizing environmental data dashboards across our mills to better understand and manage water, effluent and energy data to identify efficiency opportunities.
- In 2022, we withdrew 13,365 thousand cubic meters and discharged 12,416 thousand cubic meters of water, similar to our performance each year between 2019-2021.
Por qué es importante el agua
Gobernancia
Our Environmental Health and Safety (EHS) Policy guides our global water conservation and efficiency approach. We uphold our EHS policy managing water use at each Greif facility. We utilize our EHS team to support regulatory compliance and implement best practices regarding water use, treatment and recycling. Our centralized environmental structure oversees our compliance management system and provides any necessary support. Greif encourages and empowers local management teams to improve water efficiencies and quality, reduce water withdrawal to minimize the impact on local sources, maintain regulatory compliance and reduce water-related costs. We also continue to manage water discharge in compliance with individually allocated water permits.
Approximately 95 percent of our water use occurs in 14 paperboard mills within our Paper Packaging and Services (PPS) business. Consequently, we strive to use reclaimed water whenever possible in paper production, and our water management efforts primarily focus on our PPS mills to achieve the most significant potential impact.
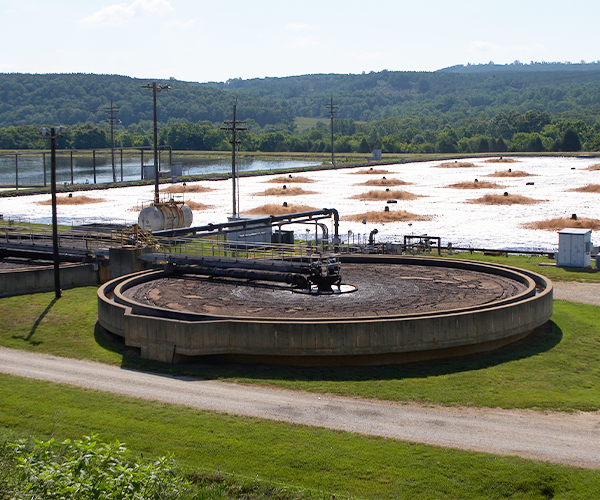
Water Reduction Study
Greif contracted a third-party consultant to perform a high-level evaluation documenting water usage at all the paperboard mills operated by Greif. The analysis considered inflows, major water usage within the production facilities and outflows. Since Greif is already operating with a high degree of internal water reuse, remaining opportunities to increase water reuse can be found by examining the flows of wastewater discharged from the facilities. The study observed that the potential water use reduction goals could be achieved by focusing on the largest water user in the portfolio, the Riverville mill. We are now evaluating water reduction projects for the Riverville mill for FY23.
Due to our Global Industrial Packaging (GIP) facilities’ low water usage, we prioritize good stormwater practices rather than water use reduction in GIP. These facilities conduct frequent stormwater sampling and testing to ensure safe limits and find improvement opportunities. At Greif, we provide all applicable colleagues with annual training on Greif’s stormwater practices and compliance activities to support responsible water management. We also implement localized stormwater pollution prevention plans and spill prevention controls at relevant facilities and have a global contingency plan and emergency procedure to avoid, reduce and mitigate any spill occurrences. We continuously update stormwater training, utilizing third-party consultants where necessary. In 2022, we updated training at all facilities covered by a stormwater permit.
Greif’s water impacts are most significant within our PPS operations. However, it is still essential to responsibly manage water use across all our operations, particularly in water-stressed regions, including Latin America, Africa and the Middle East. To mitigate the negative impacts in these facilities, we reduce water pressure where it is higher than needed, replace leaky valves, recycle water, install touchless faucets and collect and use rainwater. Greif ensures that all facilities operate within their water permits.
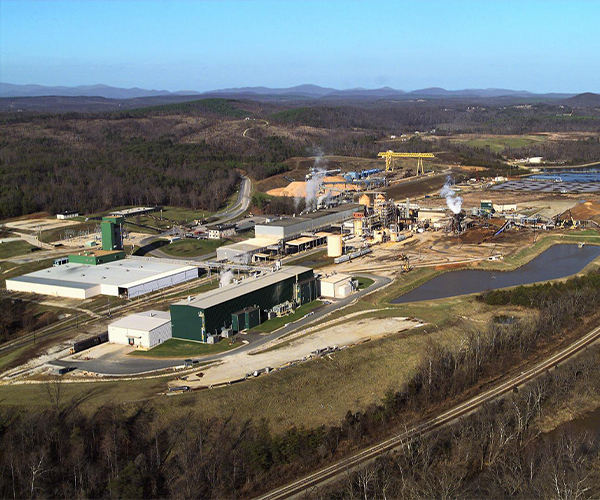
Paper Packaging & Services Water Reduction and Quality Projects
Specific examples of water reduction and quality projects recently undertaken at PPS facilities include:
- In 2021, we continued to invest in our efforts to eliminate direct discharge from our mills by converting our Baltimore, Ohio, mill to discharge to a local municipal water treatment plant. In addition to removing direct discharge from our operations, this transition reduces Greif’s overall water withdrawal by 400,000 gallons a day.
- At our Fitchburg plant, we invested approximately $500,000 to install equipment designed to retrieve suspended air solids and reduce biochemical oxygen demand (BOD) and chemical oxygen demand (COD). This process has enabled us to improve water and air quality and reduce costs.
- In our Los Angeles mill, we installed a small HydroFlo Technologies Dissolved Air Flotation (DAF) clarifier, Hydrofloat, to reduce solids in wastewater and facility expenses. The Hydrofloat recycles approximately 10,000 gallons of water a day.
- Our Fitchburg, MA mill installed and launched a much larger DAF near the end of fiscal 2021. This Evoqua Water Technologies DAF is over 100 square feet in surface area and can treat up to 300,000 gallons per day. By treating all the Fitchburg mill effluent, this DAF will reduce suspended solids (TSS) in our discharge by 80% and allow the mill stricter discharge limits in the future.
Metas, progreso y desempeño
83%
Average Recycled Water
Intake at Mills
Objetivo 2025:
- Reducir la demanda bioquímica de oxígeno descargada en kilogramos en un 10 por ciento por tonelada métrica de producción de las plantas de Riverville y Massillon utilizando una línea de base de 2014 para fines del año fiscal 2025.
To date, we have reduced the BOD by 76% from our 2014 target baseline.
In 2022, we retained a third-party consultant to evaluate our paperboard mill water use. The study created water models for each of our 14 mills and found additional opportunities for water reduction. From this study, we discovered that each mill’s intake consists of 83 percent recycled water on average. According to the models, our best opportunity to meet our water use reduction goal is prioritizing water reductions at our largest water user, the Riverville mill. In 2023, we will explore potential water reuse and reduction projects at this facility.
Greif tracks water usage and wastewater treatment using Key Performance Indicators (KPIs). We continue standardizing environmental data dashboards across our mills to better understand and manage water, effluents and energy data and identify water efficiency opportunities. These KPIs allow us to monitor our progress on our goals constantly.
Practicando la economía circular
En la planta Austell de Greif en Georgia, comenzamos un proyecto de deshidratación de residuos de aguas residuales para convertir los desechos en biocombustible. La práctica de la economía circular barre los sólidos espesados de un manto de sedimentos flotantes a una prensa deshidratadora. Los sólidos fluidos se deshidratan hasta que se pueden transportar a un lugar para secarlos al aire, mezclarlos con otros materiales y consumirlos como combustible complementario para calderas. Este proceso no solo permite reutilizar los materiales para obtener el mayor beneficio de principio a fin, sino que también ahorra las tarifas de eliminación en vertederos de la instalación.
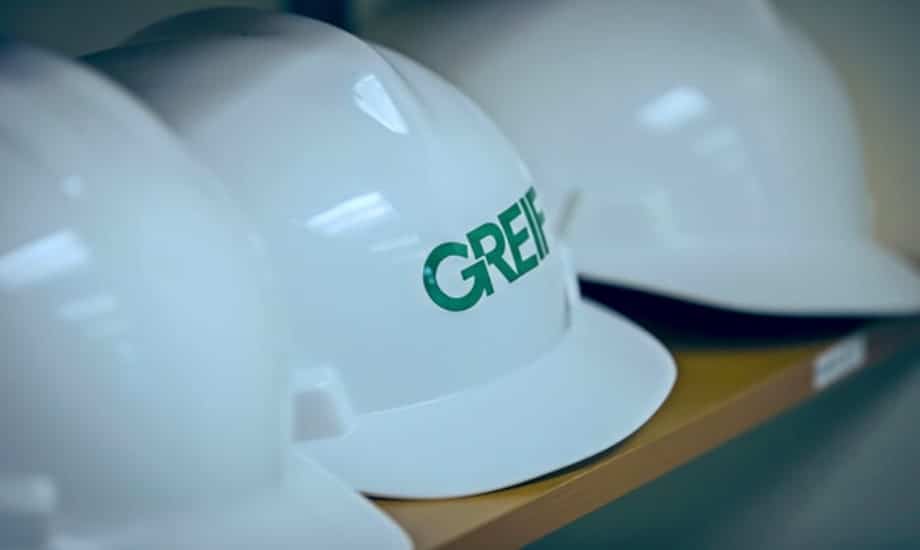
Reducción de agua en nuestra fábrica de Florence, Kentucky
A fines de 2019, la planta de Greif en Florence, Kentucky, instaló una planta de tratamiento de aguas residuales para reducir nuestra carga de desechos peligrosos y reciclar el agua para devolverla a la ciudad. El proceso funciona introduciendo agua en el sistema, eliminando cerca de 100% de los contaminantes del proceso de pintura y enviando el agua limpia a la planta de tratamiento local. Luego, la planta de tratamiento recicla el agua para redistribuirla a la comunidad. El material sobrante del proceso se elimina en la basura en lugar de en los desechos peligrosos. Cuando el equipo entró en funcionamiento por completo a mediados de 2020, el proceso no solo redujo significativamente los desechos peligrosos generados por la planta, sino que también redujo el costo de los desechos en $40,000 por mes.
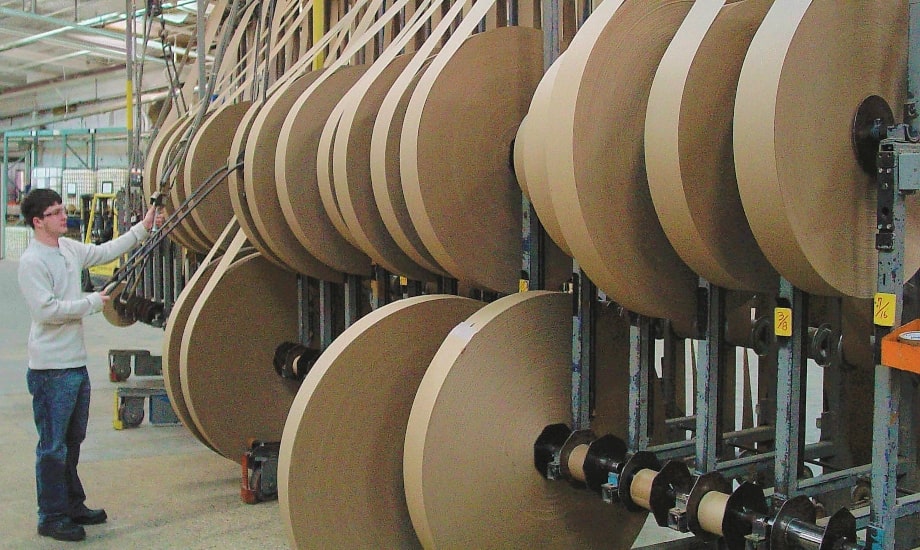