Historias destacadas
- Acerca de nuestra empresa
- Acerca de nuestro informe
- Estrategias de sostenibilidad
- Metas y desempeño
- Índices de informes ESG
- Descargas de informes
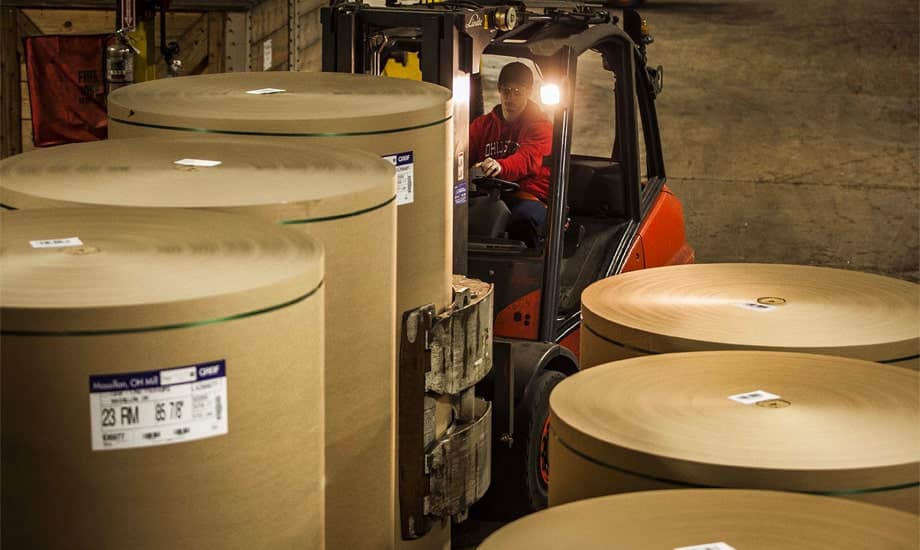
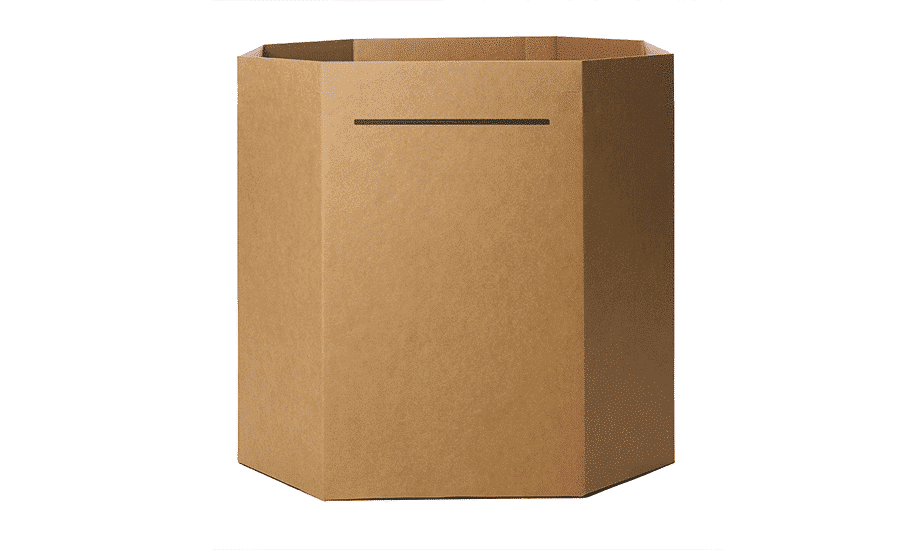
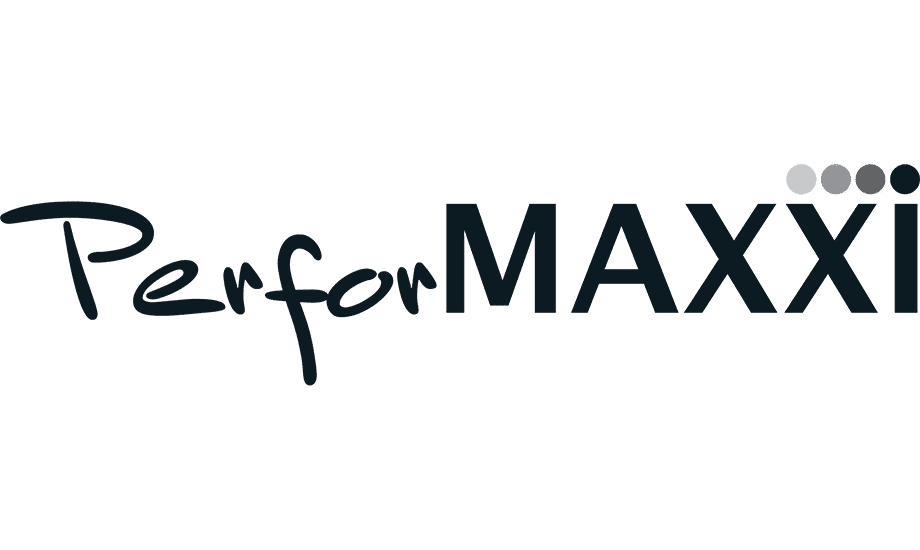
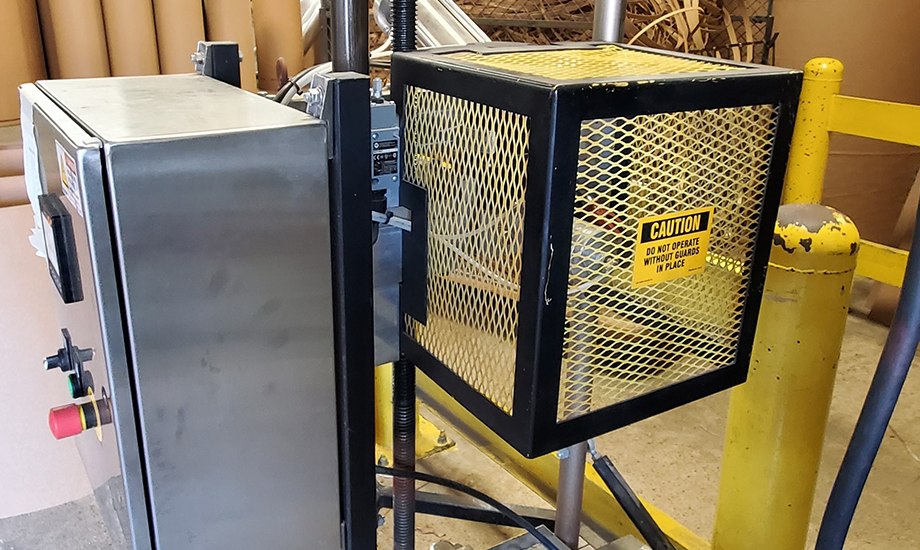
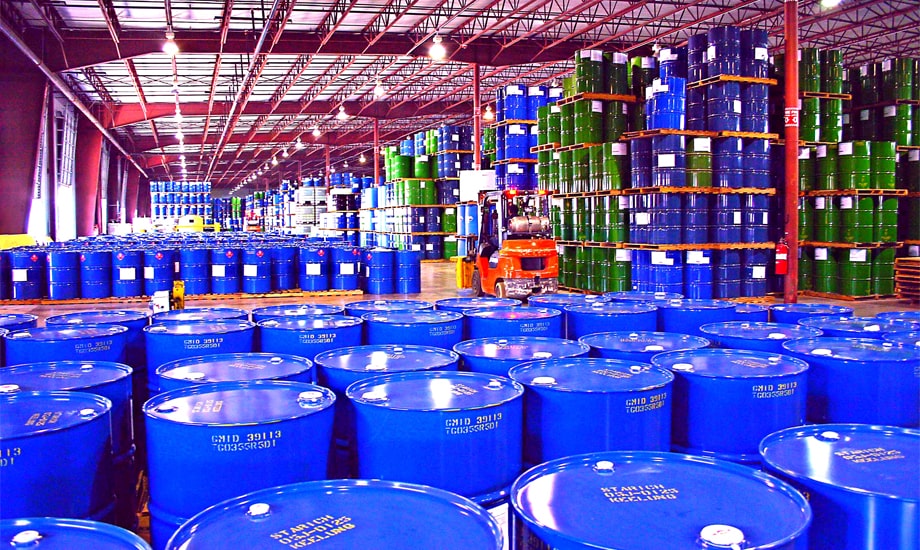
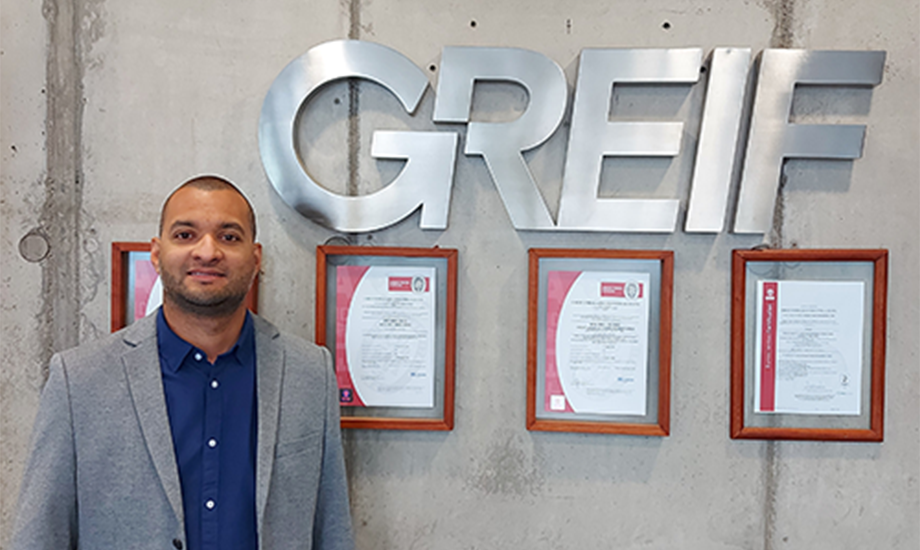
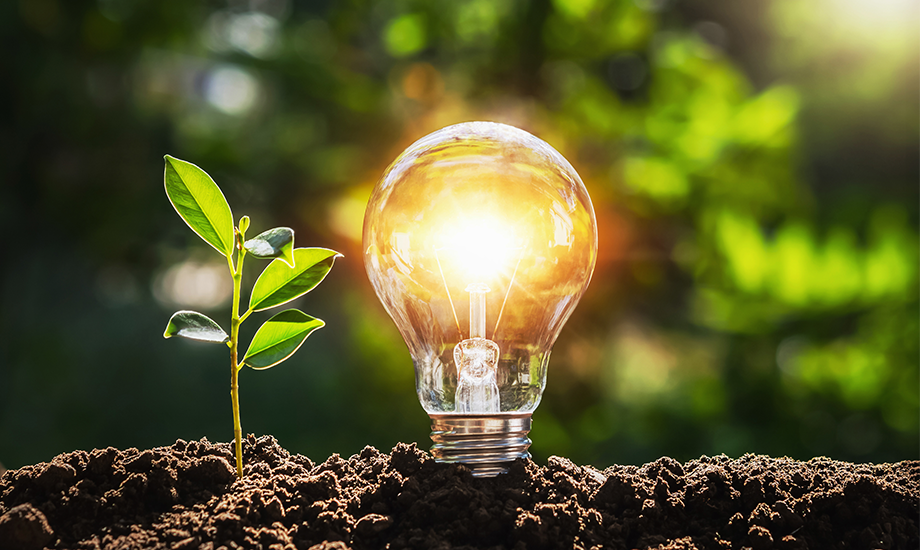
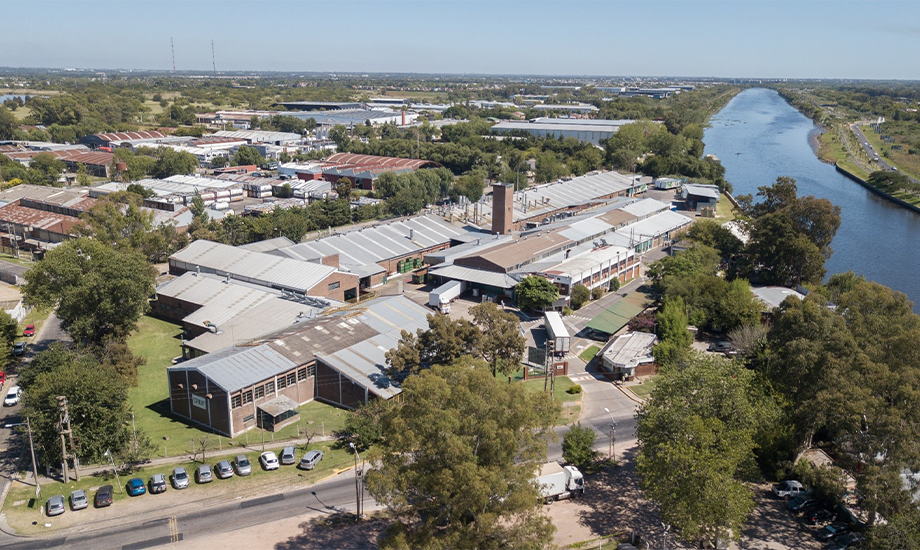
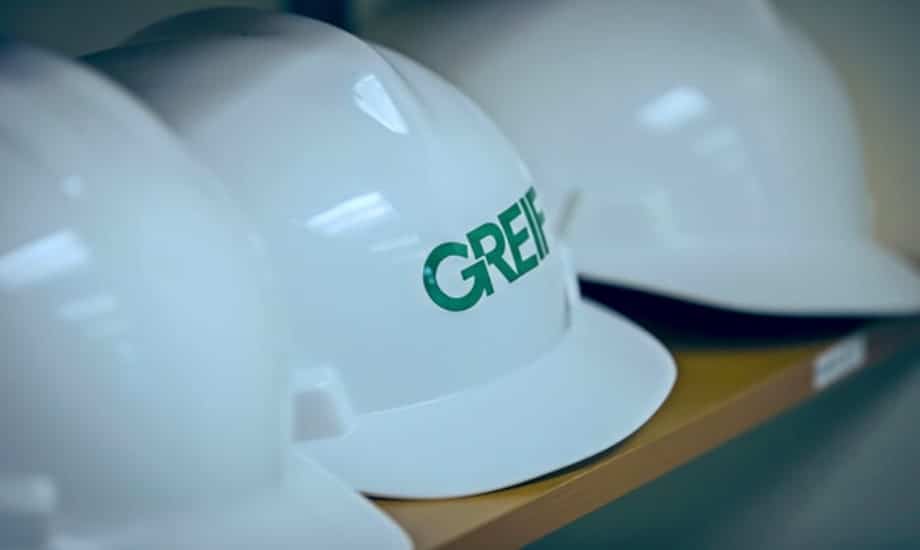
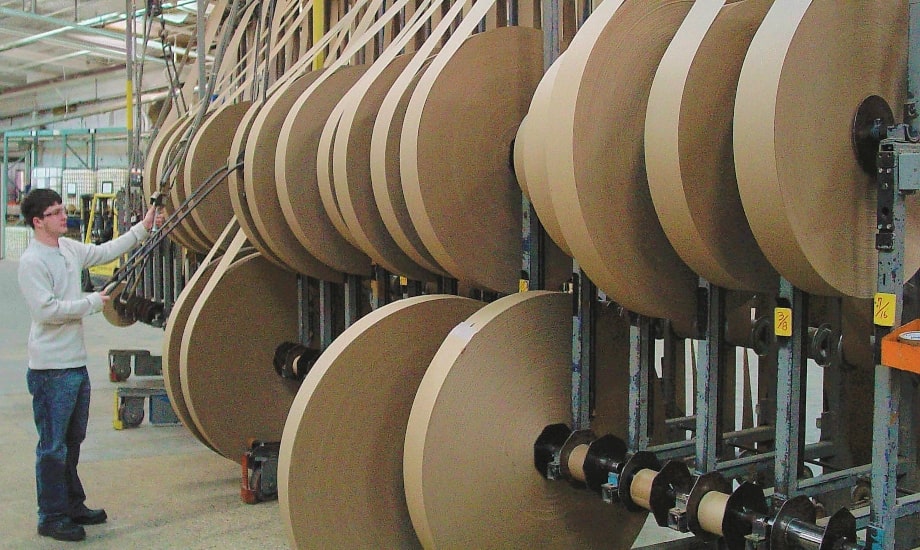
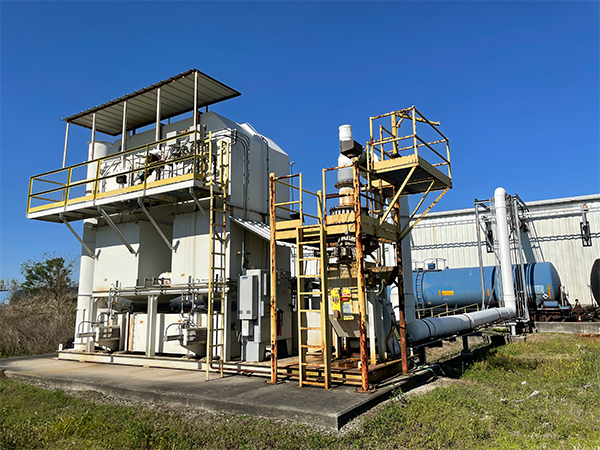

En 2007, Greif estableció un programa de becas para ayudar a los hijos de nuestros colegas que planean continuar su educación en programas universitarios o de escuelas vocacionales. Los beneficiarios de las becas se seleccionan en función de la necesidad financiera, el historial académico, el liderazgo demostrado, la participación en actividades escolares y comunitarias, los honores, la declaración de aspiraciones y objetivos educativos, las circunstancias personales y familiares inusuales y una evaluación externa.
El programa es administrado por Scholarship Management Services, una división de Scholarship America. Scholarship Management Services es el diseñador y administrador más grande del país de programas de becas y reembolso de matrícula para corporaciones, fundaciones, asociaciones e individuos. Los premios se otorgan independientemente de la raza, el color, el credo, la religión, la orientación sexual, el género, la discapacidad o el origen nacional. Scholarship Management Services realiza la selección de los beneficiarios. En ningún caso, ningún funcionario o colega de Greif participa en la selección. En 2023, apoyamos 60 becas. Desde 2007, 336 estudiantes de todo el mundo han recibido becas patrocinadas por Greif.
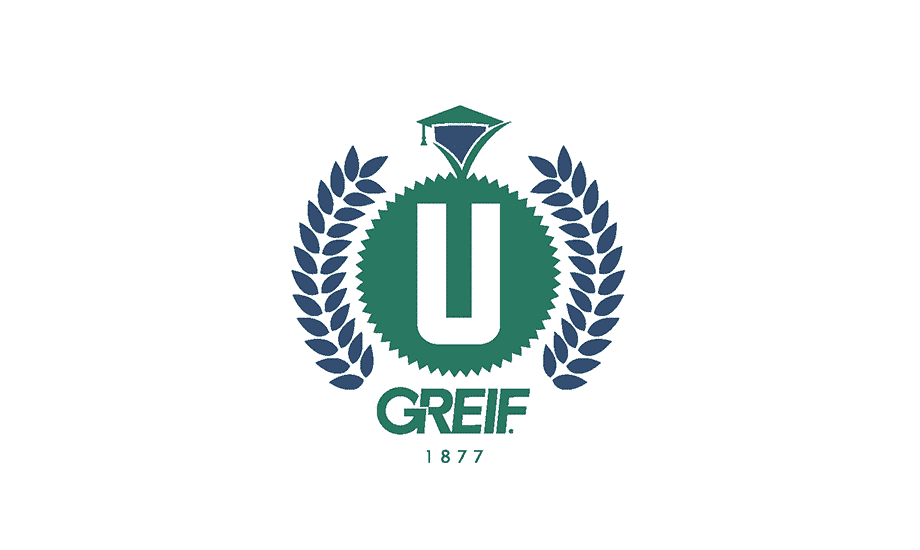
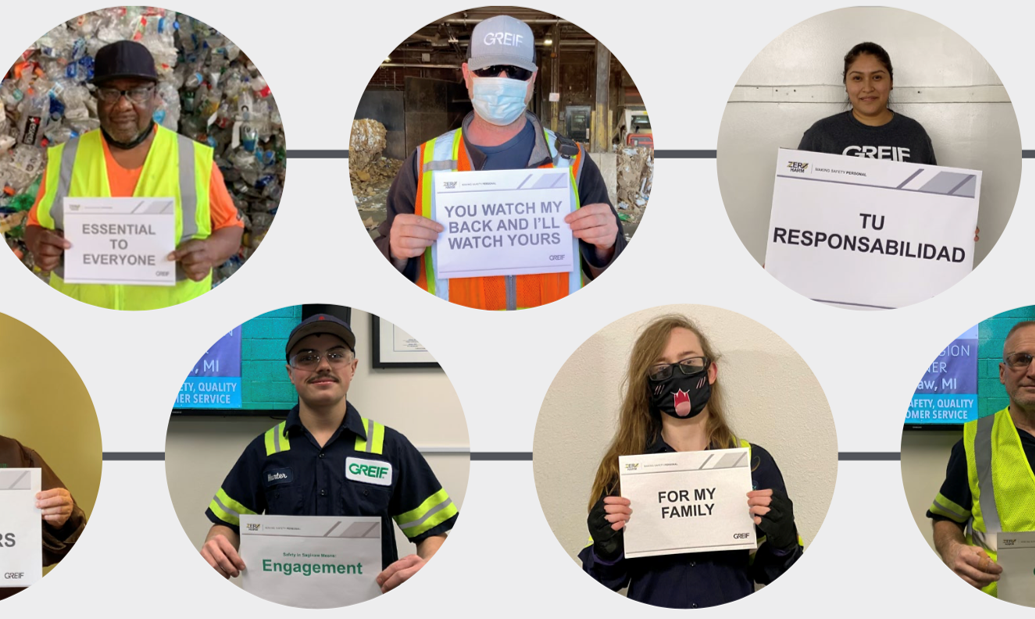
El programa Lead to Last de Greif, lanzado en 2022 como parte de nuestro marco de desarrollo de liderazgo global, brinda a todos los líderes globales un modelo unificado de expectativas de liderazgo. Esta capacitación se ofrece a través de Greif University y se lleva a cabo en ciclos de 12 semanas en los que los participantes aprenden sobre liderazgo inclusivo, seguro y basado en valores. Lead to Last se centra en dotar a los participantes de la capacidad de:
- Desarrollar una mentalidad de líder
- Realizar reuniones individuales periódicas
- Prepare a su equipo para obtener resultados
- Crear una cultura de retroalimentación
- Lidere a su equipo a través del cambio
- Gestiona tu tiempo y energía
Greif introdujo las sesiones de Lead to Last en español, chino y portugués, además de inglés, en 2023. Desde el inicio del programa, 686 colegas han participado en él.
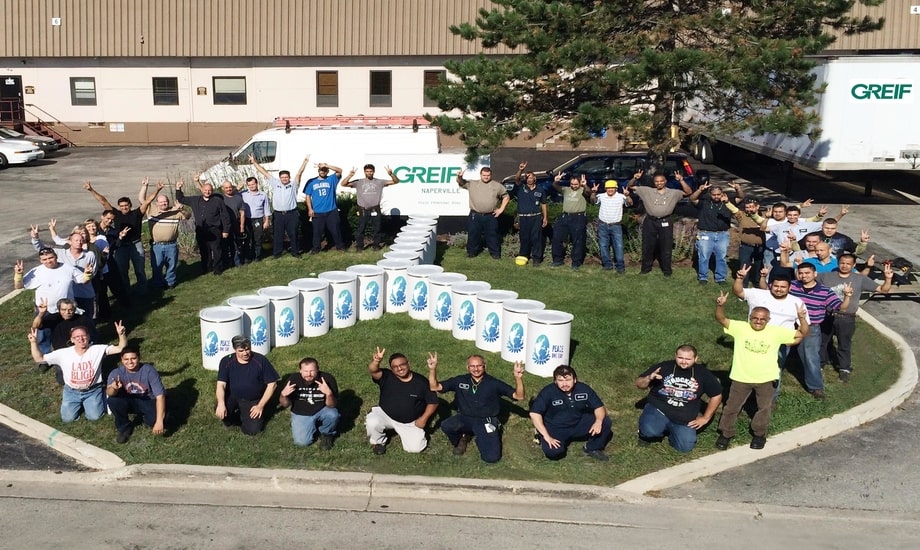
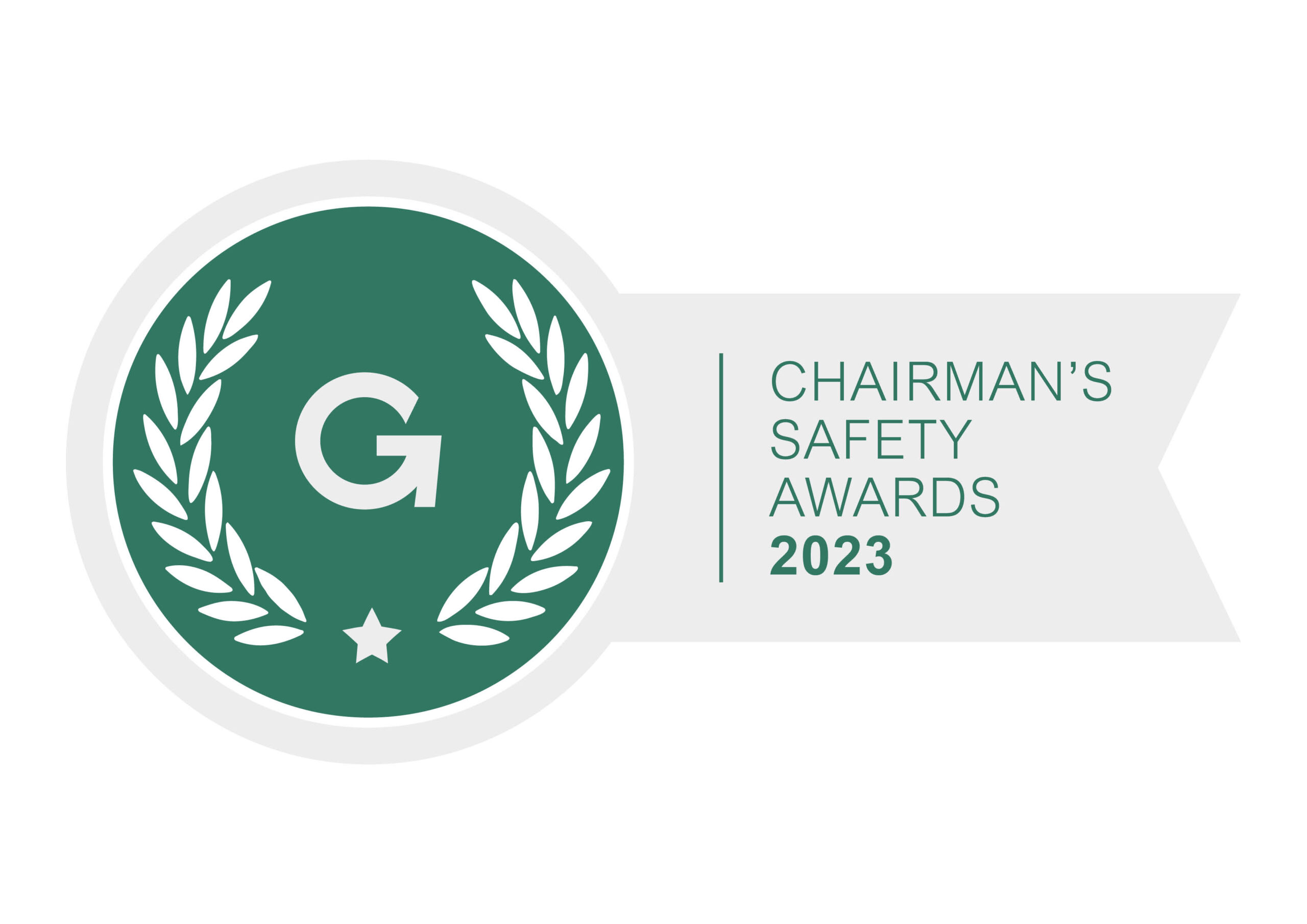
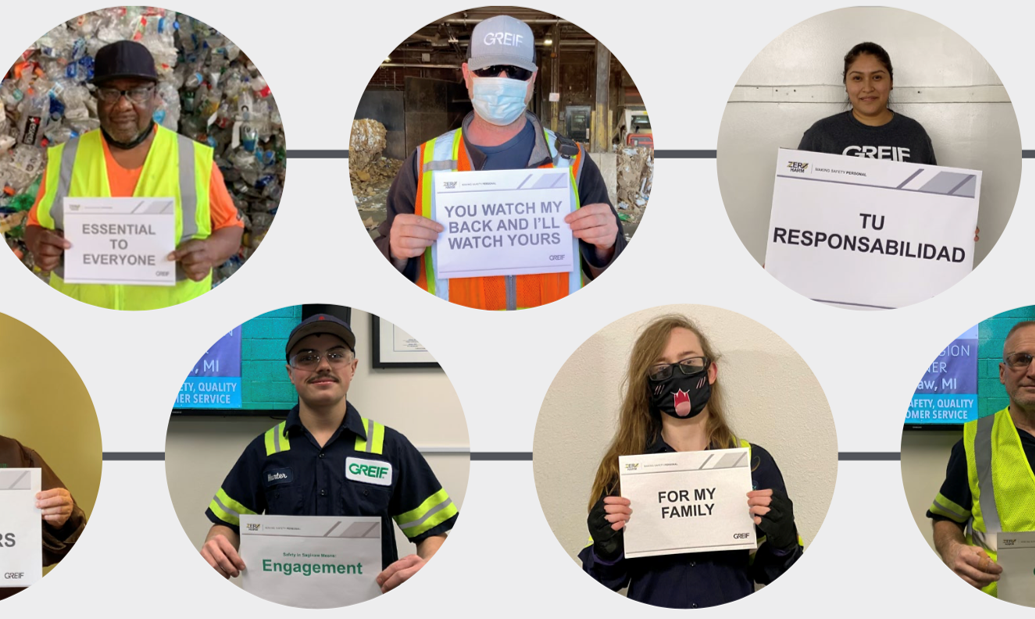
- Amaititlan, Guatemala – 16 años
- Beloyarsky, Rusia – 15 años
- Omsk, Rusia – 15 años
- Delta Cincinnati, EE. UU. – 14 años
- Volgogrado, Rusia – 15 años
- Vung Tau, Vietnam – 12 años
- Tri-Sure Vreeland/Vreeland Paint, Países Bajos – 10 años
- Kazán, Rusia – 15 años
- Vologda, Rusia – 15 años
- Mobeni, Sudáfrica – 10 años
Estos logros, así como otras instalaciones con cero accidentes en 2022, proporcionan modelos sólidos en apoyo de nuestra aspiración de cero accidentes en todas nuestras instalaciones en todo el mundo.
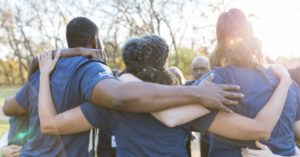
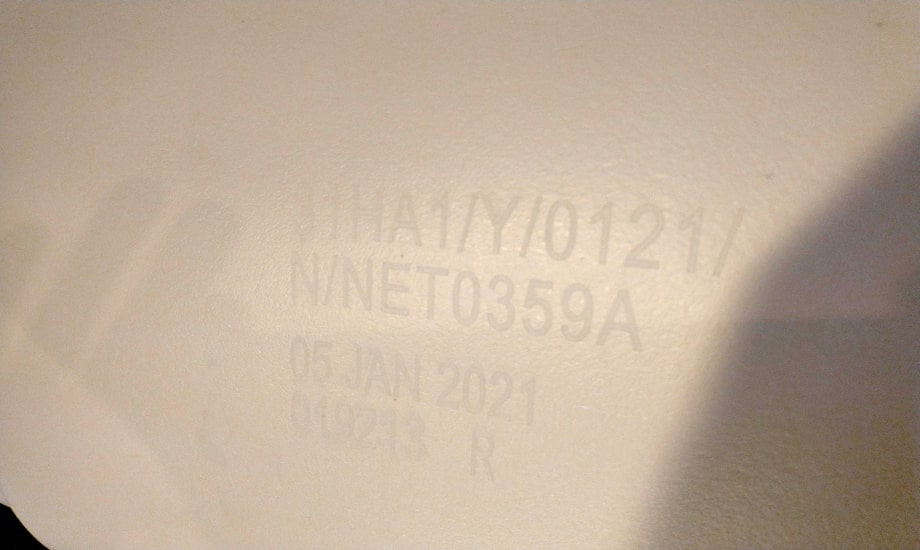
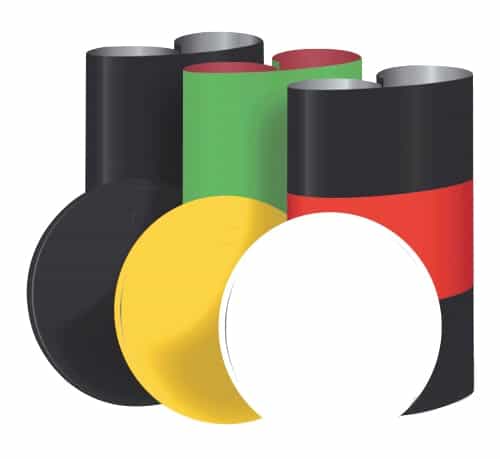
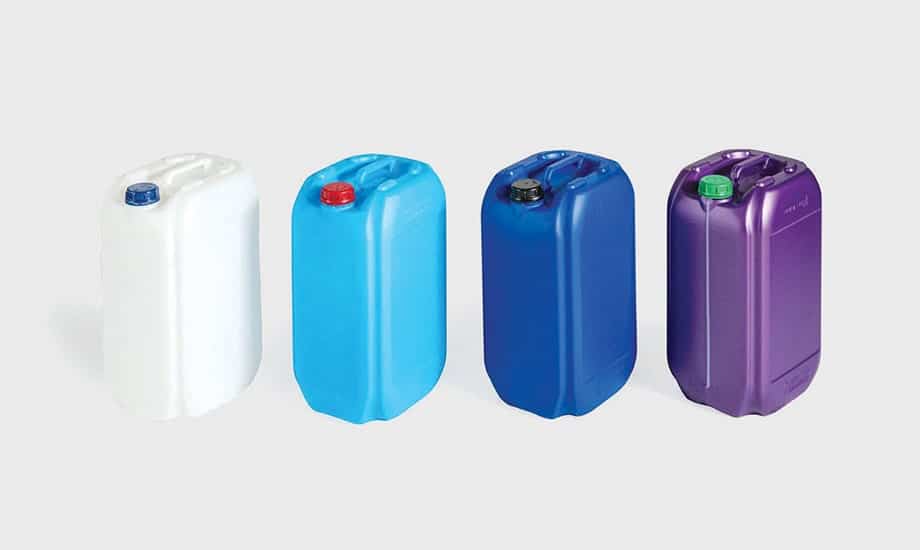
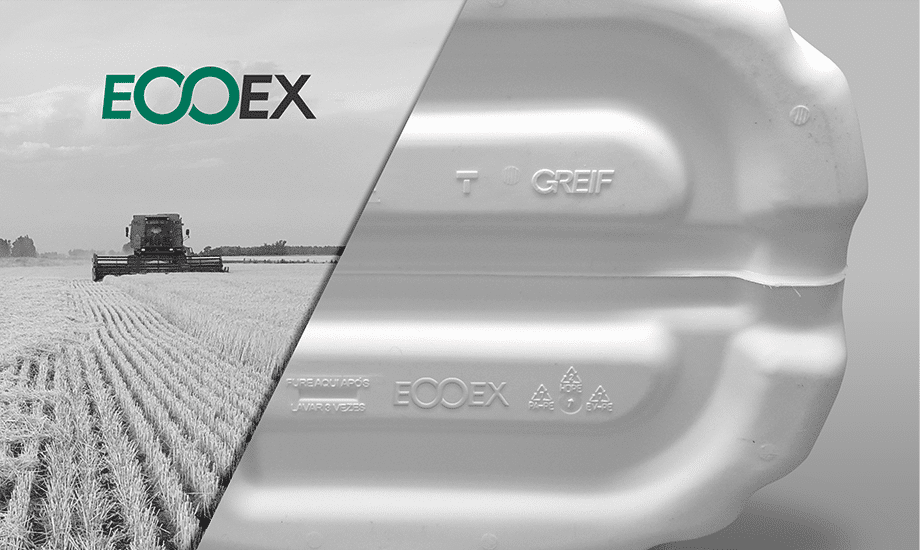
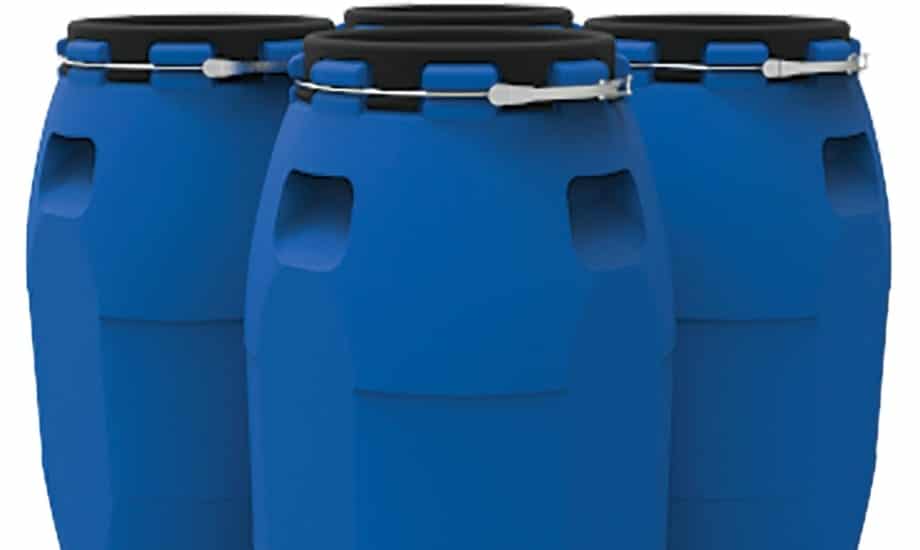
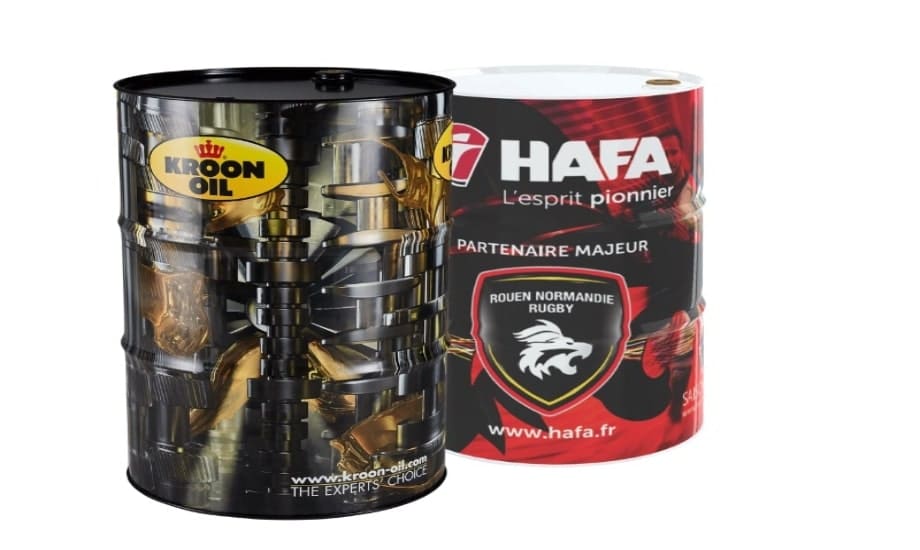
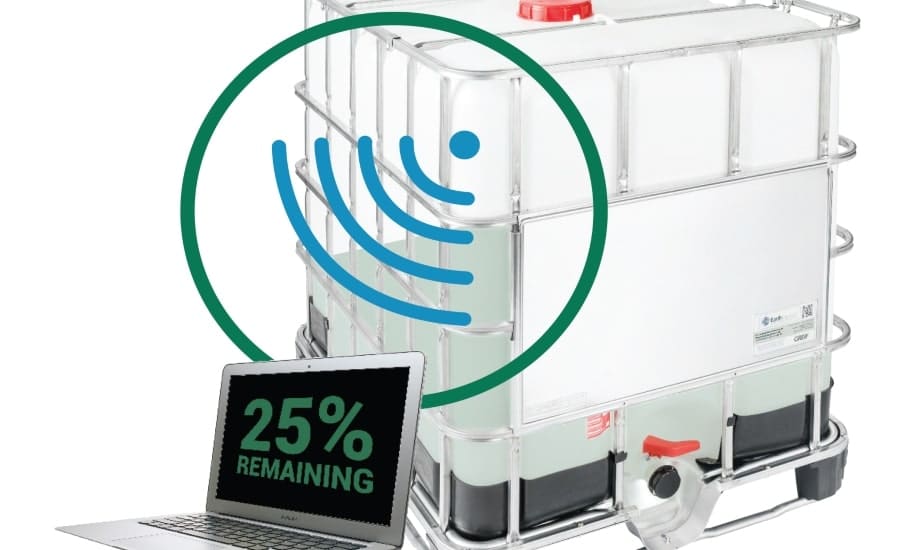
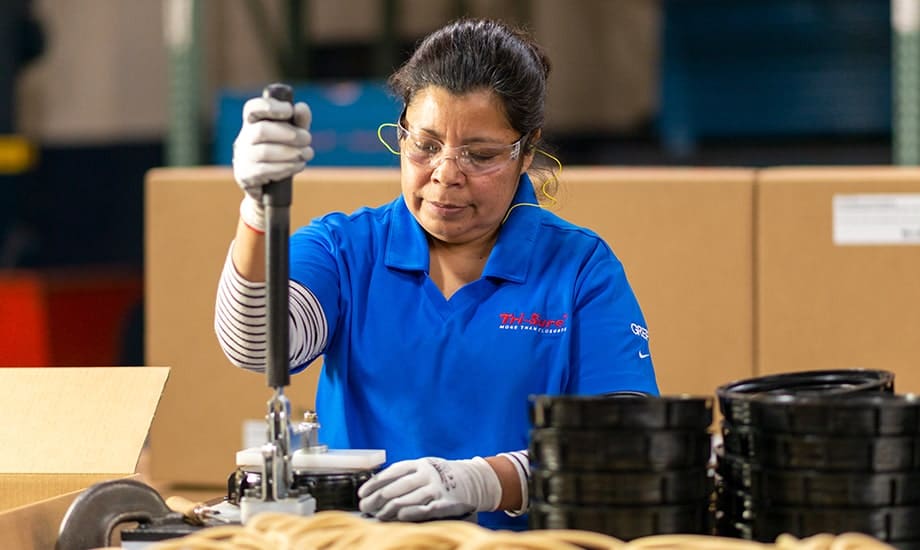
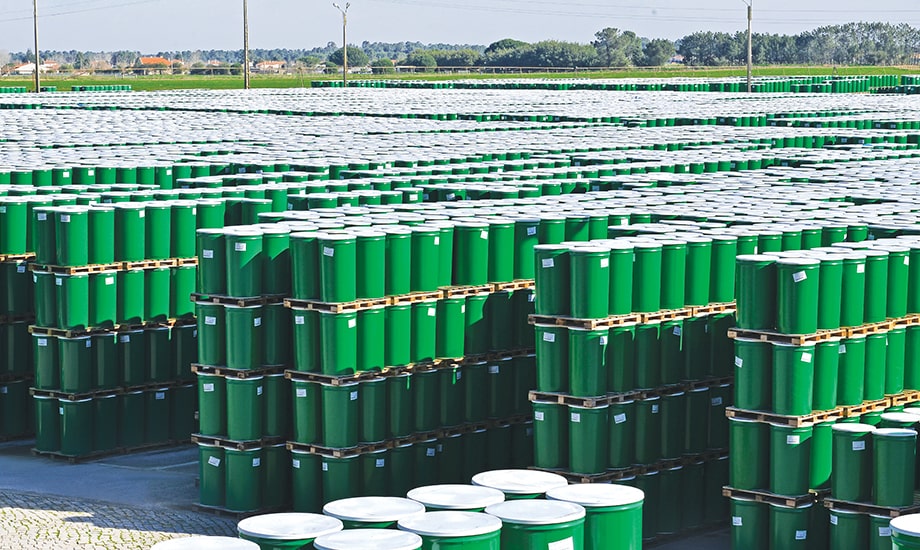
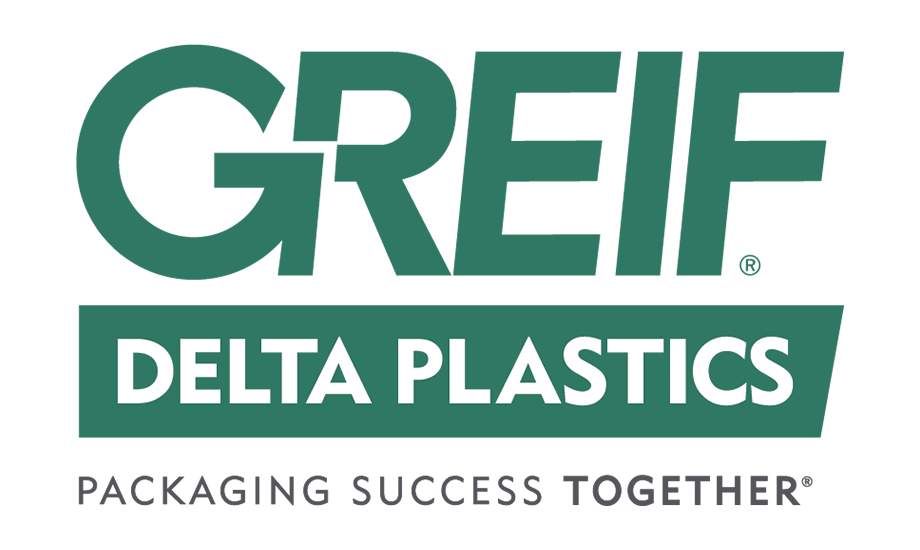
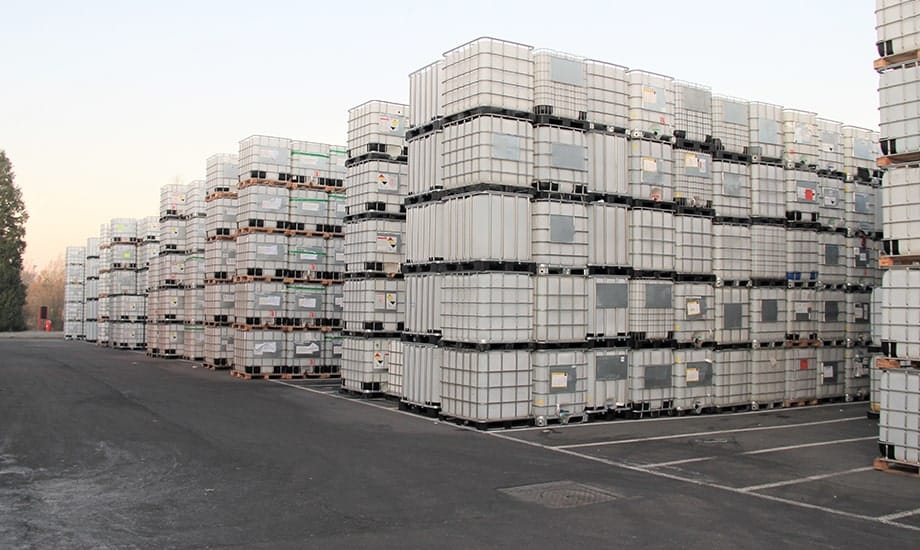
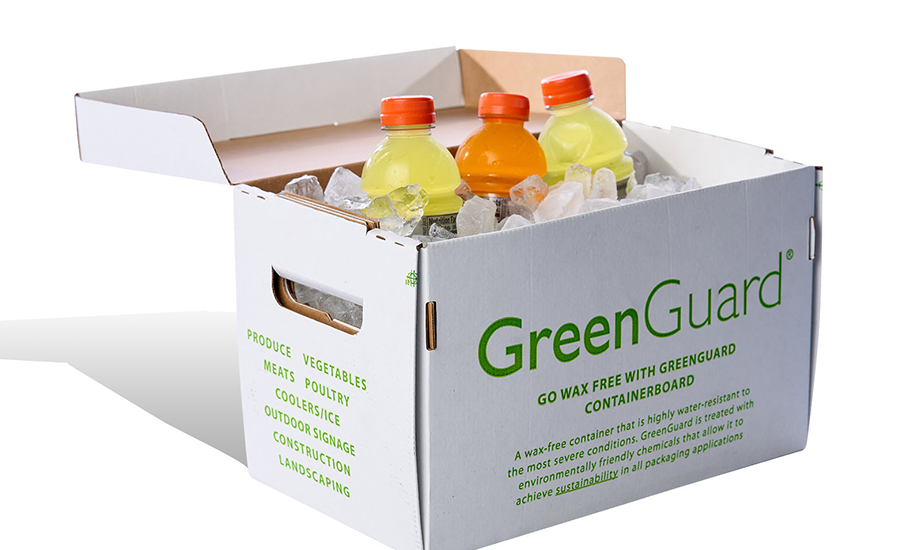