- Sobre nuestra compañía
- Acerca de nuestro informe
- Sustainability Strategies
- Goals & Performance
- ESG Reporting Indices
- Descargas de informes
Why Waste Matters
Governance
50
Facilities Achieving Zero
Waste to Landfill
Our efforts to reduce waste are global, with each facility working towards our 2025 goal.
In 2021, Greif’s Leadership Council began overseeing five sustainability issues, including waste, in an effort to further accelerate our ESG strategy. We now report on waste each quarter to the Executive Leadership Team. We also added a waste KPI to Greif’s enterprise scorecard and monthly reports that are shared with managers and tracked via the Greif Business System (GBS) and Must Win Battle (MWB) scorecard. The Global Waste Team, comprised of Greif colleagues from each business unit and region, meets monthly to discuss our waste reduction strategies. The Waste Team holds facility management accountable for managing and reducing waste. Greif implements colleague engagement strategies to empower production colleagues to focus on waste reduction. Greif’s Environmental Health & Safety (EHS) policies, procedures and training govern the labeling, handling, storage and transportation of hazardous waste.
In 2021, 54 plants held a virtual tour that included information sharing on sustainability, including waste. Members of Greif’s executive team and GIP’s leadership team attended the virtual tours to provide collaboration and support our continued waste management progress.
Greif’s Compliance Management System (CMS) allows us to collect data, monitor performance and measure progress accurately and efficiently. In 2020 and into 2021, we improved our ability to view and manage waste data in CMS by enabling monthly access to data. This allows each facility to gain insights into data more quickly and implement programs throughout the year. As part of our CMS, we require all facilities to report monthly waste data, submit invoices for verification in addition to roadmaps. Our waste data is subject to evaluation and verification by our internal audit team to ensure consistency and reliability.
For all Global Industrial Packaging (GIP) facilities, we maintain a detailed waste matrix to help us understand each facility’s waste streams, each waste stream’s disposal method (recycling, reuse, landfilling, etc.) and manage progress. The waste matrices serve as a collaboration tool allowing facilities to compare management of common waste streams. In 2021, our PPS business began the process of developing matrices, allowing for company-wide integration of our waste data and programs. As part of this process, we built a foundation of education and training throughout our PPS business, including trainings on data entry and waste stream identification. These efforts enabled a number of our facilities to reach or make significant progress towards our goal to divert 90 percent of waste from landfills at all facilities. We will complete our waste matrices for all PPS facilities in 2022.
Facilities that have yet to reach our 2025 waste diversion target are responsible for creating a quarterly, or semi-annual, roadmap to evaluate all waste streams going to landfill and develop a diversion strategy. Each facility includes at least the top three waste diversion projects and reports on associated cost reductions, waste to landfill reductions and the status of each project. Our waste diversion roadmaps provide great insight into our facilities and their waste management progress, and help facilities improve performance year over year. Our roadmaps play a critical role in our ability to reach our waste diversion goal, enabling each facility to understand its waste management needs and identify actions for improvement. Waste training for staff is another key component to continuous improvement in achieving our waste strategy and goals.
Greif has partnered with Operation Clean Sweep (OCS) to expand our commitment to reducing plastic waste. Through the partnership, we commit to conducting audits in our facilities to evaluate our plastic resin handling operations and implement best practice housekeeping and pellet, flake and powder containment practices. Third party audits were conducted at our Hazleton, Pennsylvania, Houston, Texas and Mt. Sterling, Kentucky locations from 2017 to 2019, before being paused due to the COVID-19 pandemic. All facilities passed our continued internal audits and we will restart third-party audits in 2022.
Goals & Progress
In 2018, we created a goal to divert 90 percent of waste from landfills from all Greif production facilities globally by the end of fiscal year 2025. In 2020, we began to include waste data from our legacy Caraustar facilities as well, expanding our goal to cover our entire enterprise. Globally, we diverted 85 percent of waste from landfills in 2021 and 149 Greif facilities achieved our waste diversion goal. These facilities continue to improve their waste management practices by leveraging waste matrices and through close collaboration with our stakeholders in support of our circular economy strategy. In 2021, 60 facilities reached 99+ percent diversion, of which, 50 facilities achieved zero waste to landfill.
Progress:
FY 2021* |
Facilities With 90%+ Diversion |
Facilities With 99%+ Diversion |
Facilities With Zero Waste to Landfill |
---|---|---|---|
Total |
149 |
60 |
50 |
North America |
74 |
17 |
12** |
Europe |
54 |
32 |
29** |
Latin America |
9 |
1 |
0 |
Asia Pacific |
12 |
10 |
9 |
**Data from four facilities that were closed in FY21 is included
Performance
WASTE STREAM
|
FY 2018 |
FY 2019 |
FY 2020 |
FY 2021 |
---|---|---|---|---|
Hazardous Waste | ||||
Total Waste to Landfill |
1,639 |
2,428 |
3,608 |
1,033 |
Waste to Landfill |
1,292 |
1,161 |
2,989 |
584 |
Incinerated (no energy recovery)**** |
347 |
1,267 |
619 |
449 |
Total Non-Landfill* |
14,105 |
20,725 |
19,199 |
14,207 |
Incinerated (with energy recovery)** |
3,372 |
4,073 |
3,275 |
4,480 |
Composted*** |
0 |
0 |
1 |
0 |
Recycled† |
7,604 |
14,084 |
14,160 |
8,502 |
Reused†† |
1,513 |
651 |
706 |
482 |
Reclaimed††† |
217 |
366 |
376 |
172 |
Miscellaneous (Non Landfill) †††† |
1,399 |
1,551 |
681 |
571 |
Total Hazardous Waste |
15,744 |
23,153 |
22,807 |
15,240 |
Non-Hazardous Waste |
||||
Total Waste to Landfill |
54,594 |
33,837 |
137,211 |
155,367 |
Waste to Landfill |
54,110 |
33,380 |
137,066 |
155,148 |
Incinerated (no energy recovery)**** |
485 |
457 |
151 |
218 |
Total Non-Landfill* |
257,219 |
184,357 |
326,546 |
842,268 |
Incinerated (with energy recovery)** |
2,054 |
2,950 |
17,006 |
13,409 |
Composted*** |
35 |
15,784 |
49,734 |
54,132 |
Recycled† |
231,997 |
141,217 |
212,075 |
727,737 |
Reused†† |
11,641 |
12,321 |
19,441 |
18,445 |
Reclaimed††† |
9,439 |
9,847 |
11,701 |
12,192 |
Miscellaneous (Non Landfill)†††† |
2,052 |
2,239 |
16,589 |
16,354 |
Total Non-Hazardous Waste |
311,813 |
218,194 |
463,757 |
997,634 |
Total Waste (Hazardous & Non-Hazardous) |
327,557 |
241,347 |
486,564 |
1,012,874 |
Notes:
- Legacy Caraustar facilities were incorporated into waste reporting in FY 2020.
- Total waste and Non-Hazardous recycling doubled this year due to inclusion of additional data from RFG facilities; last year RFG and IPG only included data from their own operational waste streams. However, RFG also collects waste paper from the market and recycles them.
*Non-Landfill: Includes chemical-physical, incineration with energy recovery, recycled, reused, reclaimed, composted and fuels blending treatment methods
**Incinerated (with energy recovery): Treatment method involving the combustion of solid waste that results in energy capture.
***Composted: Treatment method involving the biological decomposition of solid or liquid operational waste.
**** Incinerated (no energy recovery): Treatment method involving the combustion of solid waste that does not result in energy capture.
†Recycled: Treatment method involving the separation, preparation and sale of recyclable materials to end-user manufacturers.
††Reused: Treatment method involving the use of a material for its original purpose multiple times.
†††Reclaimed: Treatment method involving the process of extracting and converting materials from recycled materials to be used again.
†††† Miscellaneous (Non Landfill): All other treatment methods not mentioned previously, including Deep Well Injection and On-Site Storage.
Greif Joins Alliance to End Plastic Waste
In September 2021, Greif became a member of the Alliance to End Plastic Waste. Since 2019, the Alliance to End Plastic Waste has rallied around 90 member companies, project partners, allies and supporters who are committed to ending plastic waste in the environment. Greif joined this mission to partner with our customers and other organizations to bolster our circular economy strategy. We are the first industrial packaging firm to become a member to provide expertise from our unique perspective and be a leader in our industry. Membership requirements include investing in innovative projects to promote circular solutions. We will have more to share on this exciting development in 2022.
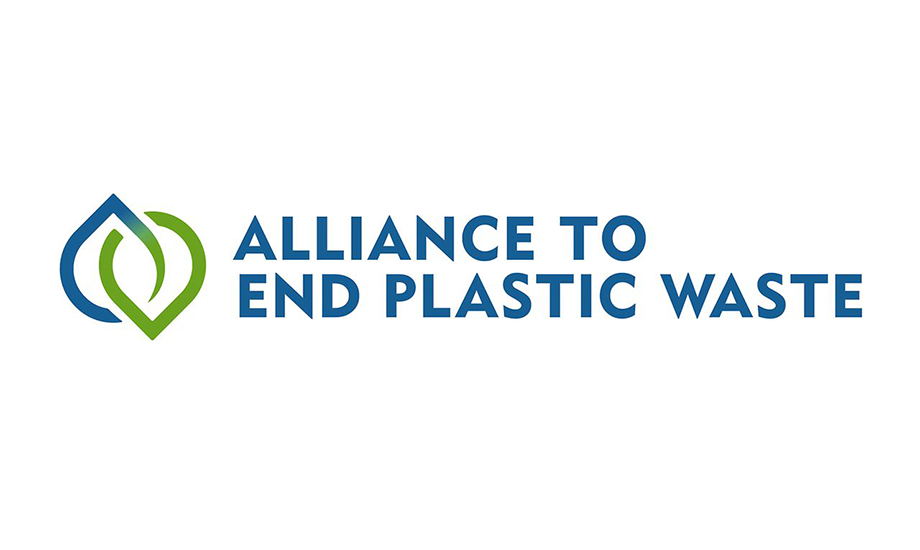
Greif Houston Facility
The Greif facility in Houston saw marked improvement in its ability to divert waste from landfill during 2021. The facility installed a de-chimer, a device designed to safely and efficiently remove the metal chimes which are used to secure the top and bottom of fibre drums. Once the chimes are removed, the fibre and metal can be directed to separate waste streams for recycling. Since the de-chimer’s installation in July 2021, the facility has diverted more than 90 percent of its waste from landfills. The facility sends the fibre to our PPS Recycling Group, further reducing the waste disposal cost.
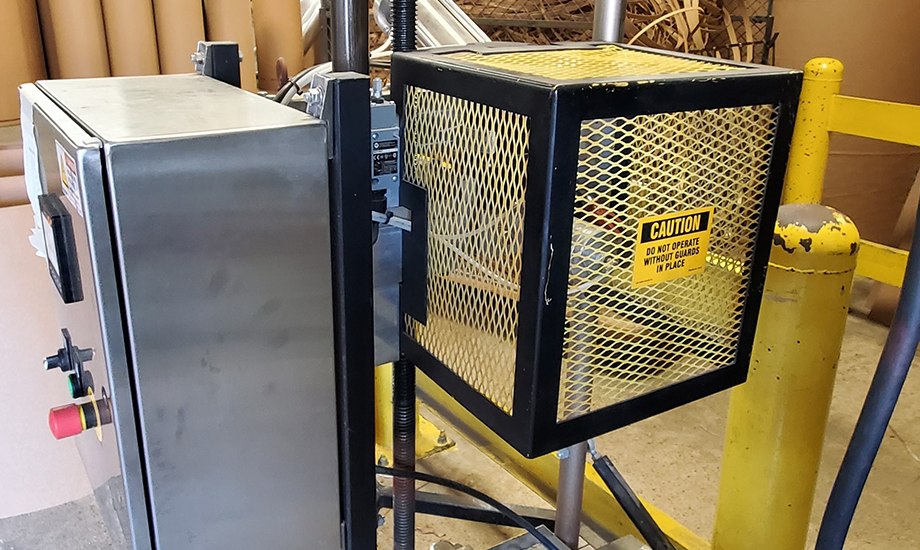
Greif Hadımköy Reaches and Exceeds 90 Percent Waste Diversion Target
During 2020, the Hadımköy team in Turkey developed a waste roadmap by assessing their waste streams and determining a path to reduce their waste going to the landfill. The Hadımköy team introduced separation bins for paper waste in production, separated leftover food waste and sent it to local animal shelters, and introduced separation bins for packaging and paper waste in the cafeteria. In total, these efforts led to a seven percent reduction in their waste to landfill. By the end of 2020, Hadımköy used the projects on their waste roadmap to further reduce their waste to landfill an additional five percent and already exceeded the corporate 2025 waste target. In 2021, Hadımköy further reduced their waste sent to landfill by an additional 15 percent from the previous year.
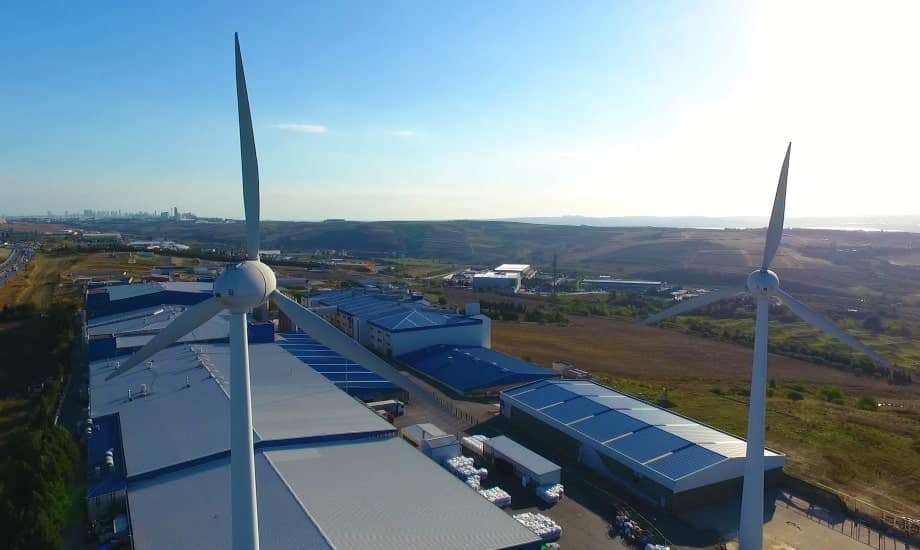
Reducing VOC’s Through Use of Water-Based Exterior Paints
Greif is committed to using water-based exterior paints in our operations where possible, rather than high volatile organic compound (VOC) exterior paints. In Global Industrial Packaging (GIP) North America, eight out of our nine steel plants use water-based paints. In GIP China, the Greif Zhuhai plant has converted to over 75 percent water-based paints and, in 2021, they began testing the use of water-based regular drum liners in our products to further reduce the VOC impact of our products. The Greif Shanghai plant begun the conversion process in 2021 as well. In EMEA, the Czech Republic, Belgium, Germany, Hungary, and Poland use water-based paints alongside solvent-based paints.
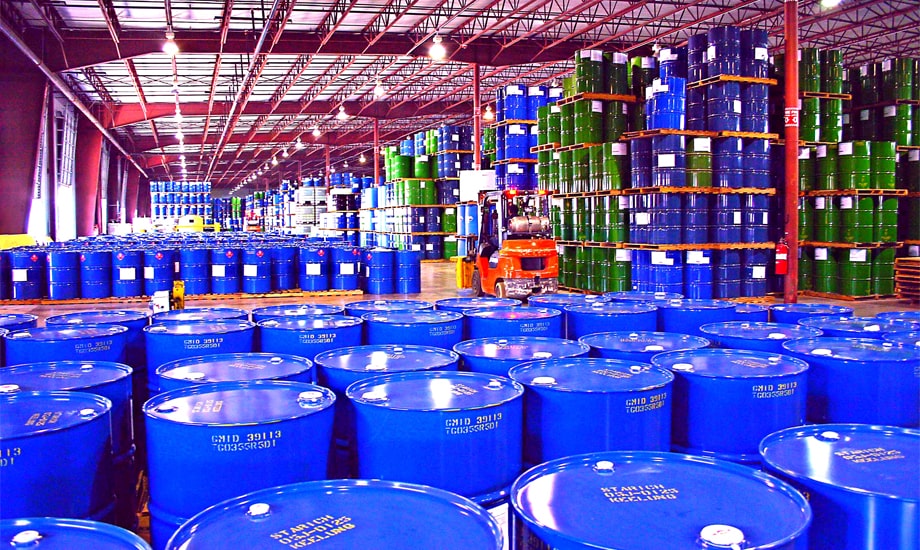
Achieving Waste Reduction through Customer Service Excellence
In 2019, Greif’s Global Industrial Packaging (GIP) facility in Sweden received a customer complaint that jerrycans were being damaged during unpacking because the plastic film used to wrap the pallets was too tight and difficult to remove. In response, the facility tested a number of film alternatives that were easier to remove and posed less risk of damaging the cans and ultimately selected an alternative that reduced the use of film by 48 percent, saving 7,500 kg of materials annually. The transition also led to $12,000 USD savings and a 22,000 kg emission reduction. In order to scale the project, the team has updated the standard operating procedure for using similar films and have worked with our procurement team to update the supplier and material for the film.
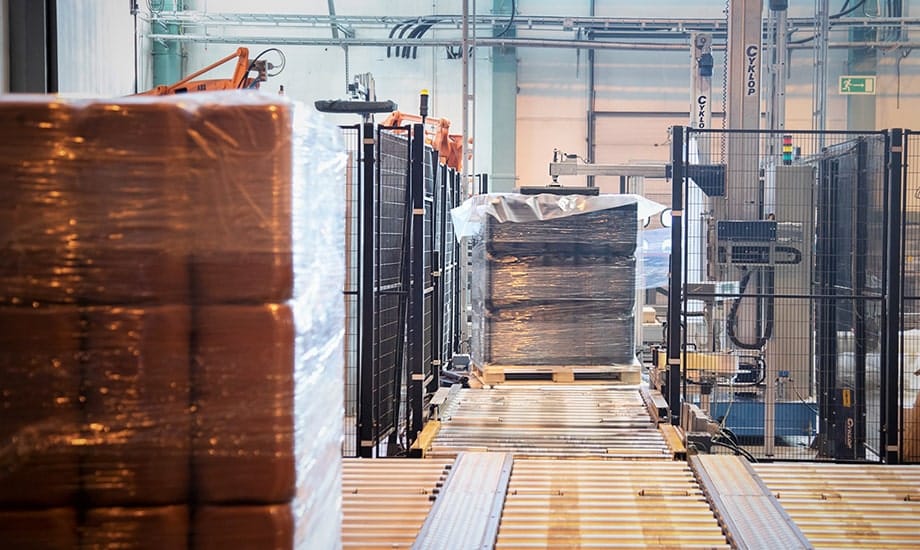
Recycle and Reuse Initiatives at GIP Flexibles Facility
Our GIP Flexibles Facility in Thirsk, UK has implemented a variety of initiatives related to recycling and reuse, in close collaboration with customers and suppliers. The facility introduced programs to reuse cardboard dividers, pallets, thread spools, solvent, bag on roll tubes and scrap wood. Our reuse initiatives include close collaboration with suppliers to return spools and cardboard dividers for them to reuse, reducing costs and environment impacts for both companies. We also work with our customers to collect pallets and tubes for our own reuse. The facility also recycles all plastic, cardboard, paper and solvent that cannot be reclaimed. These practices help reduce Greif’s footprint and can often reduce costs, such as incineration expenses.
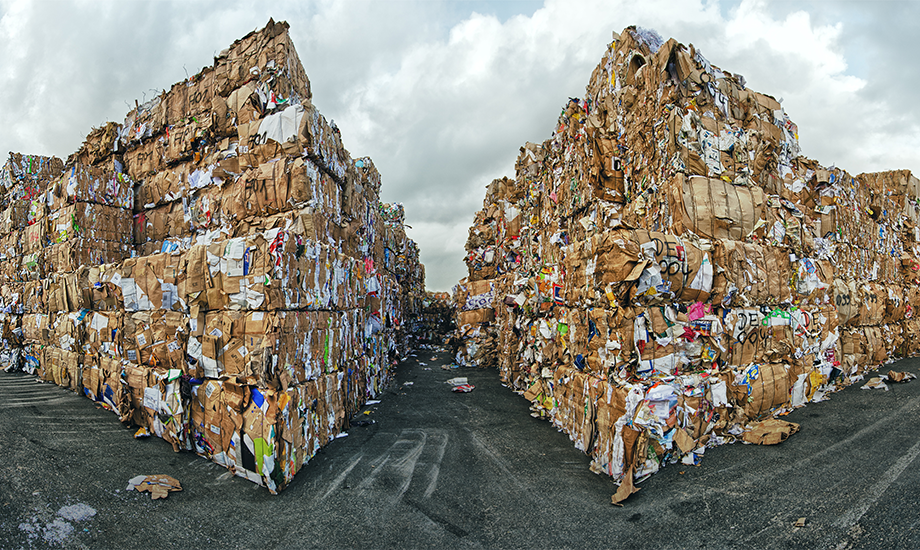
SUSTAINABILITY HIGHLIGHTS
85%
Of Waste Diverted From Landfills
Our efforts to reduce waste are global, with each facility working towards our 2025 goal.
50
Facilities Achieving Zero Waste to Landfill
Highlighting best management practices to eliminate, reduce and divert waste.