- Über unser Unternehmen
- Über unseren Bericht
- Nachhaltigkeitsstrategien
- Ziele und Leistung
- ESG-Reporting-Indizes
- Bericht-Downloads
Why Cradle to Cradle Manufacturing, Reconditioning, Reuse & Recycling Matters
Führung
Greif’s strength, as an organization, is the breadth of our products covered by our Life Cycle Services (LCS) including steel, plastic and paper products. Therefore, we are working to connect our many life cycle services across our businesses globally. Our Leadership Council prioritized sustainability this year and was divided into five teams each dedicated to a specific area of sustainability, including circularity. The circularity team was dedicated to advancing and operationalizing circularity within our operations and across our value chain. Near the end of 2021, this team created the Global Circularity Team, which is tasked with collecting data and understanding our current circular economy status to inform our 2030 targets. We will develop our 2030 circular economy goals in 2022.
Greif’s Life Cycle Services network collects used, empty, steel, plastic and Intermediate Bulk Container (IBC) rigid packaging products and reconditions or recycles them to be suitable for reuse and then reintroduces them into trade. The reconditioned containers reduce the demand for virgin raw materials while decreasing the number of containers that go to landfills. If we cannot recondition containers, we recycle the materials to use for other products. Many of Greif’s largest customers use our LCS network to recondition their containers. Customers who use the network can receive reports through the Greif Green Tool, enabling them to quantify impact by tracking key indicators such as carbon footprint reduction, waste reduction and material savings. In 2021, we developed our Greif Green Tool Lite, which houses a smaller number of products than the Greif Green Tool, but it allows us to more quickly run analyses for customers. This year, we also introduced our new IBC collections app in four countries in Europe. Through the app customers can submit requests for Greif to pick up their discarded packaging products and recondition them. We plan to expand this app to additional regions in 2022. Across Global Industrial Packaging (GIP), we reconditioned, remanufactured or recycled more than 4.5 million containers, and our Paper & Packaging Services (PPS) business managed over 3.2 million metric tons of recycled fiber in 2021.
Greif Recycling Operations
Paper Packaging & Services
94,991
Metric Tons of Virgin Materials Saved
Our recycling, reconditioning and reuse operations helped us remove over 94,991 metric tons of virgin steel, high-density polyethylene and wood from our supply chain in 2021.
In addition to our reconditioning operations, Greif operates 19 recycling facilities in our Paper Packaging & Services (PPS) business. Through these facilities, we offer complete outsourcing solutions for plastics, pulp and paper fiber procurement, transportation and administration and provide complete paper fiber audit and management solutions. 99.2 percent of the products we handle, by volume, are paper fiber. Our paper fiber recycling operations collect waste paper for use in our own containerboard mills and for sale to other containerboard and recycled paper product manufacturers. Because of our integrated capabilities, Greif holds a central position in the paper recycling industry and operates as a net positive recycler. We use approximately 50 percent of the fiber we collect in our operations to manufacture paper products for use in consumer and industrial settings. The remaining 50 percent of the fiber we collect is sold to external mills and other manufacturing operations to produce new paperboard, molded fiber packaging and other products. More than 78 percent of the fiber we use in our paper manufacturing is from purely recycled inputs.
We are proud to be able to offer services that enable the reuse of fiber. Recovered fiber is an input to many essential goods but has suffered from reductions in supply through the economic closures caused by the global COVID-19 pandemic. Prior to COVID-19, recovered fiber value was at historical lows with the cost of recovery greater than the fiber value for many recyclers. Since the onset of COVID-19, the supply of recovered fiber has lagged behind the demand. Due to high-demand and a shortage of recycling infrastructure, there is insufficient fiber volume to satisfy demand resulting in historically high costs. Today the critical importance of expanding access to recycling is clear, particularly as more commerce takes place at the home instead of in stores. Through our sales force and participation in various industry groups, we are doing our part to educate the market on the dynamics of the changing industry to ensure this remains a viable business with a robust supply chain for all the essential goods that depend on recovered fiber inputs.
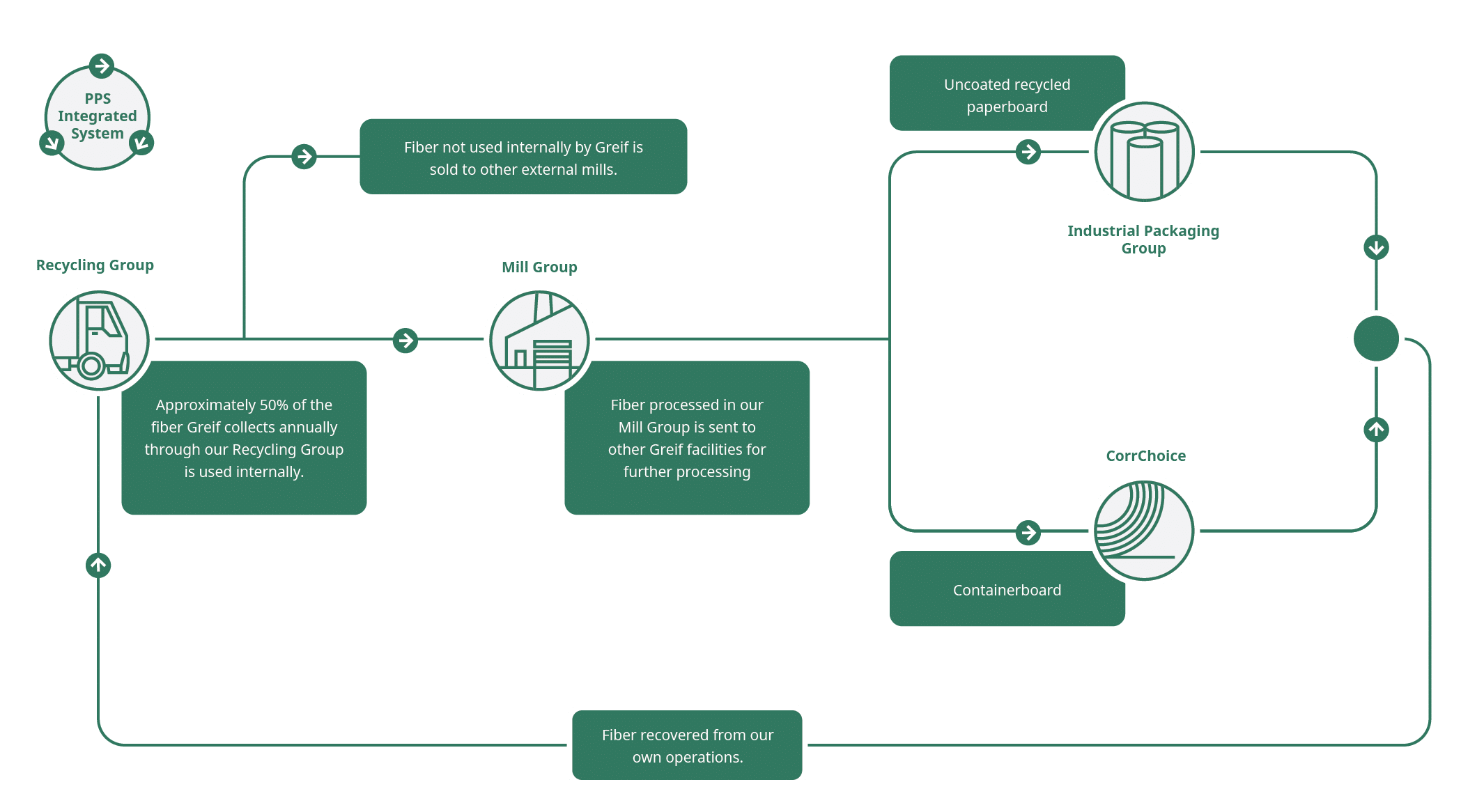
Global Industrial Packaging
In our Global Industrial Packaging (GIP) business, we look for reuse and recycling opportunities wherever possible. 91 percent of our plastic products are recyclable and 100 percent of our internal regrind plastic, which accounts for approximately 20 percent of our drums and IBCs, is reincorporated into our products. We recycle 90 percent of our internal scrap used to produce our flexible products and the balance is sold to recycling companies. There is approximately seven percent recycled plastic (internal scrap) in our FPS plastics products. We make our steel products from approximately 15 percent recycled steel globally and 33 percent recycled steel in North America.
Cradle to cradle and the use of recycled products are just two components of our circular economy strategy that span across our operations and value chain. As part of that strategy, we are working to drive circular economy principles in five key areas:
- Reducing raw material use
- Waste reduction and reducing natural resource use
- Innovation and increasing recyclability, and use of recycled materials, in our products
- Fiber-based alternatives to single-use plastics
- Life cycle services
Please see the Lieferkettenmanagement, Abfall, and Innovation pages of our report for more information about how our circular economy strategy spans our entire business.
In 2022, we will continue the evolution and expansion of our reconditioning services. In our PPS business, we place greater emphasis on our fiber business to identify solutions that will be valuable to our customers and work to bring them to life.
Leistung
LIFE CYCLE SERVICES – ESTIMATED DRUMS AND IBCS RECONDITIONED*
|
FY 2017 |
FY 2018
|
FY 2019
|
FY 2020
|
FY 2021
|
---|---|---|---|---|---|
Recycled |
904,883 |
849,498 |
831,576 |
968,296 | 1,153,345 |
|
534,369 |
571,355 |
509,884 |
562,980 | 987,427 |
|
212,272 |
161,447 |
243,186 |
358,280 | 95,176 |
|
158,242 |
116,696 |
78,506 |
47,036 | 70,742 |
Reconditioned |
3,218,885 |
3,258,848 |
3,533,358 |
3,276,259 | 3,164,809 |
|
2,565,052 |
2,713,025 |
2,699,393 |
2,483,485 | 2,185,329 |
|
321,188 |
244,497 |
194,011 |
178,627 | 141,782 |
|
332,645 |
301,326 |
639,954 |
614,147 | 837,698 |
Total Collected |
4,136,828 |
4,105,936 |
4,348,706 |
4,164,585 | 4,345,284 |
|
3,099,633 |
3,284,380 |
3,193,049 |
2,971,549 | 3,192,196 |
|
535,460 |
405,944 |
437,197 |
536,281 | 236,958 |
|
501,735 |
415,612 |
718,460 |
656,755 | 916,130 |
Virgin Materials Saved by Reconditioning and Reuse (Metric Tons)** |
63,111 |
63,587 |
76,415 |
71,149 | 74,713 |
|
56,200 |
57,664 |
66,860 |
62,016 | 63,143 |
|
5,150 |
4,243 |
5,897 |
5,553 | 6,610 |
|
1,761 |
1,680 |
3,659 |
3,580 | 4,960 |
Virgin Materials Saved by Recycling (Metric Tons)*** |
18,755 |
16,644 |
14,117 |
14,358 | 19,772 |
|
13,463 |
12,697 |
10,273 |
10,215 | 17,394 |
|
4,580 |
3,385 |
3,402 |
3,871 | 1,960 |
|
712 |
562 |
442 |
272 | 418 |
**Estimates based on the quantity of reconditioned packaging and average packaging specifications (North America and Europe)
***Estimates based on the quantity of recycled packaging and average packaging specifications (North America and Europe)
REBU – ESTIMATED FLEXIBLE INTERMEDIATE BULK CONTAINERS (FIBCS) RECONDITIONED EUROPE, MIDDLE EAST AND AFRICA
|
FY 2017 |
FY 2018 |
FY 2019 |
FY 2020 |
FY 2021 |
---|---|---|---|---|---|
Total FIBCs Collected | - |
316,324 |
275,732 |
242,000 |
220,132 |
|
- |
224,418 |
179,912 |
167,000 |
60,719 |
|
- |
91,906 |
95,820 |
75,000 |
159,413 |
Total Virgin Polyethylene Saved (Metric Tons) |
727.6 |
634.2
|
556.6 |
506.3 |
|
|
- |
516.2 |
413.8 |
384.1 |
366.6 |
|
- |
211.4 |
220.4 |
172.5 |
139.7
|
**Estimates based on the quantity of recycled packaging and average packaging specifications (Europe)
Using Recycled Plastic in IBC Molding
Greif’s Tri-Sure facility in Carol Stream collaborated with GIP North America purchasing, GIP Italy and four GIP NA plants to source 800,000 pounds of recycled plastic resins to use in the production of IBC rear/corner feet and corner protectors. This internal sourcing strategy reduced costs by $100,000. The team also reused empty corrugated bulk boxes to ship the recycled products they manufacture, reducing corrugated bulk box purchases by 84 percent. The project created company value and established environmental and financial benefits, while closing two internal loop systems and contributing to circular economy principles by diverting waste from landfills and finding a new purpose for them. Due to the outstanding sustainability impact of the project and its ability to be scaled to other molding and injection molding facilities, the project and Tri-Sure Carol Stream team was awarded the Michael J. Gasser Sustainability Award.
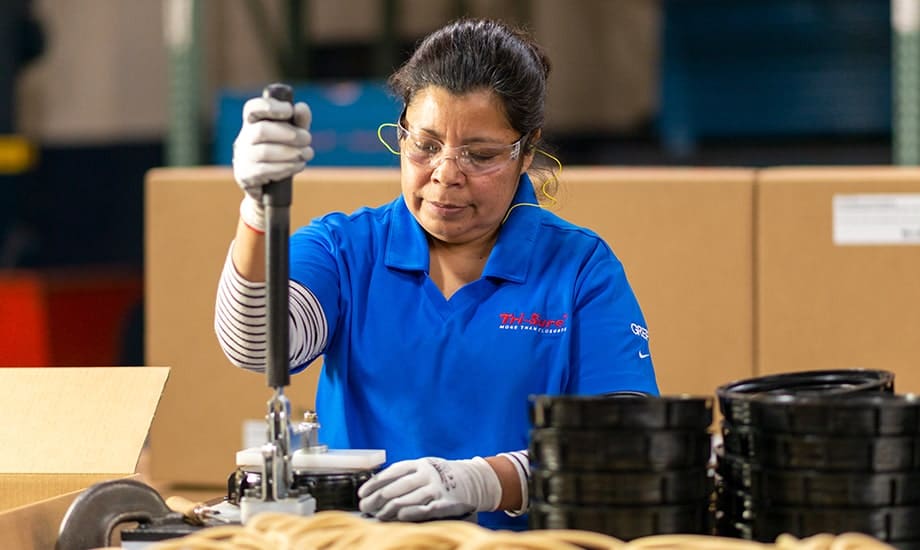
Fiber Recycling for the Flooring Industry
In 2020, our Dalton, Georgia Recycling Facility worked with the floor covering manufacturers in the Dalton area to process recovered fiber and create a “closed loop” for paperboard cores. Each year, the Dalton Recycling team recovers tens of thousands of tons of core waste from these manufacturers and recovers this waste fiber. This same fiber is used by Greif’s paper mills to manufacture 100 percent recycled new paperboard, which is then converted into new tubes and cores in Greif’s Industrial Products Group (IPG). This initiative helps not only sustain the recycling programs in Dalton but also maintain our level of excellent customer service with IPG customers. Annually, this program helps recycle 25,000 tons of cores, 10,000 tons of cardboard, 5,000 tons of boxboard and 2,000 tons of plastic film from the flooring industry in north Georgia.
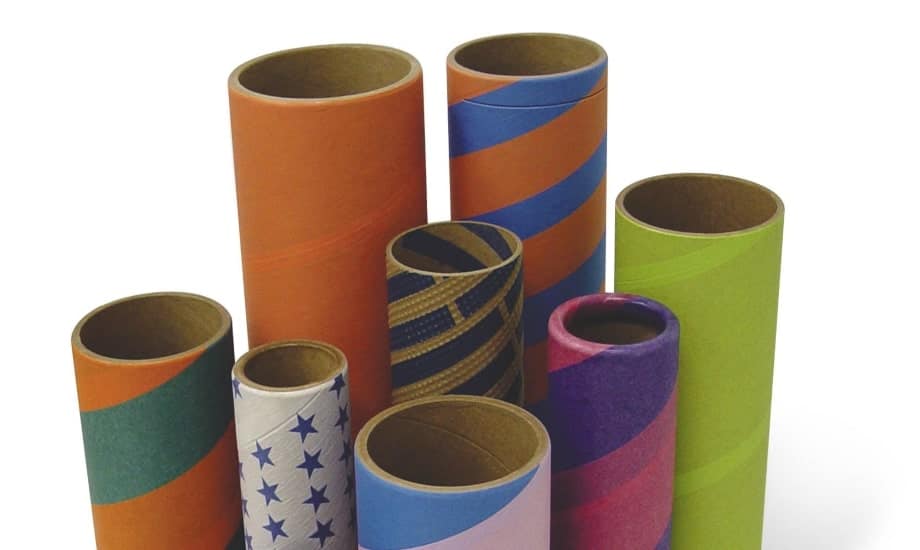
Reconditioning Conical Drums in Portugal
For the past 20 years Greif’s RIPS facility in Iberia, Portugal has been supplying customers with reconditioned conical drums, having reconditioned over 10 million drums and saving 50,000 tons of steel, 197,600 tonnes of CO2 emissions, 2,600,000 gigajoules of energy and 343,200 cubic meters of water in the process. The project was initially started as a way to help address our customers’ wish to reduce waste and lower their carbon footprint and overall improve customer satisfaction. The team collaborated with customers to understand their needs, including volume, specification requirements and safety, developed a reconditioning process and ultimately installed a reconditioning line to begin serving customers. Today, the facility serves a multitude of customers, reconditioning 500,000 conical drums and saving 5,200 tons of steel each year.
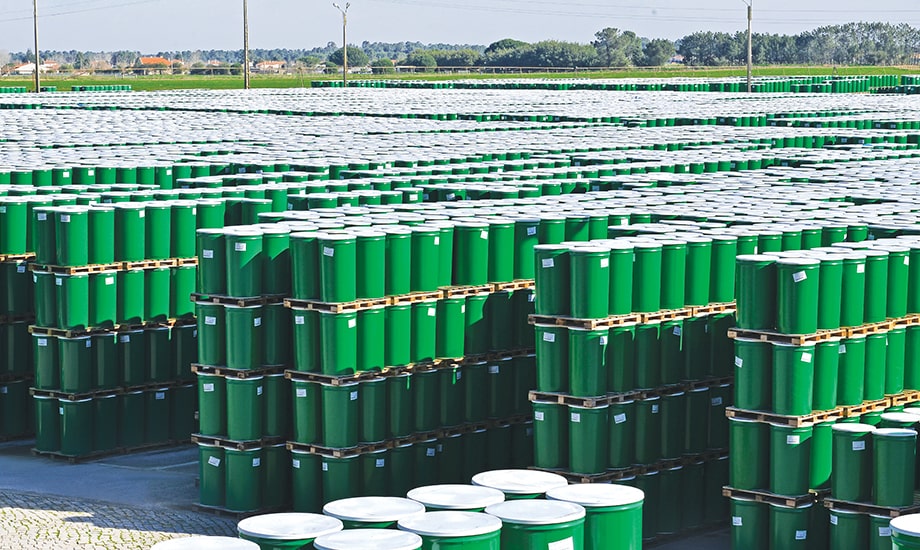
Expanding Cradle to Cradle Services with Investments and Joint Ventures
In 2020, Greif made investments and established multiple joint ventures in order to expand the scale and capabilities of the reuse, recycling and reconditioning services we provide. In April of 2020, Greif acquired a minority stake in Centurion Container LLC, expanding our intermediate bulk container (IBC) reconditioning network in North America. In August of 2020, Greif established a joint venture with Delta Plastics, the leading independent supplier of reconditioned IBCs in the United Kingdom. Finally, in December of 2020, Greif acquired a minority stake in LAF s.r.l., expanding IBC reconditioning services for our Italy-based customers. We look forward to working with our partners to continue to reduce our environmental impact through cradle to cradle solutions.
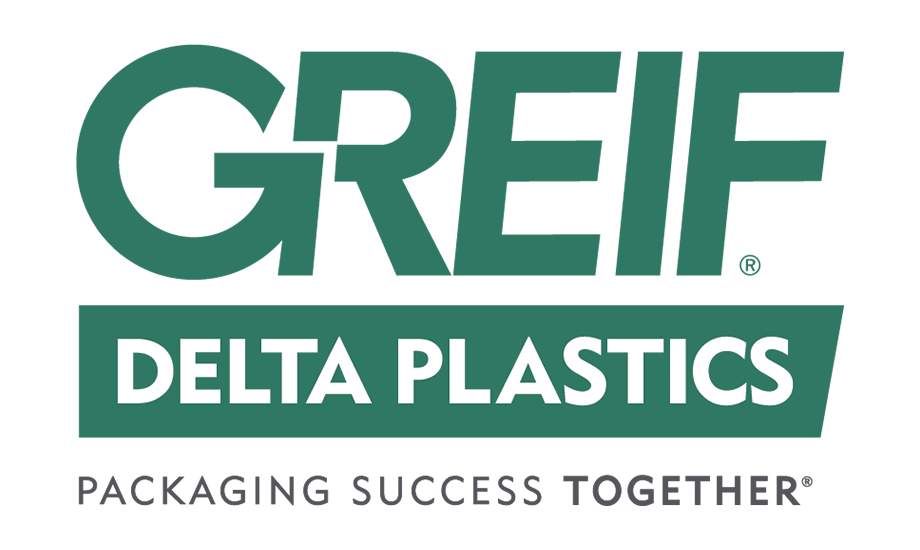
Greif Green Tool
Das Greif Green Tool ist ein flexibler Rechner, der unabhängige Lebenszyklusdaten von Greif-Industrieverpackungsprodukten verwendet. Er wurde entwickelt, um unseren Kunden dabei zu helfen, fundierte Entscheidungen darüber zu treffen, welche Industrieverpackung am besten zu ihren Produkten passt und ihre Nachhaltigkeitsziele zu erreichen. Das Green Tool wurde von einem Drittanbieter auf Grundlage der Normen ISO 14040/14044 entwickelt und ermöglicht es Kunden, die Umweltauswirkungen von Kunststofffässern, Stahlfässern, IBCs, Fiberfässern und Big Bags, die speziell auf ihr Geschäft bezogen sind, zu überprüfen und zu vergleichen. Die Ergebnisse können verwendet werden, um eine Umwelt-Grundlinie zu erstellen und Kunden dabei zu helfen, aussagekräftige Vergleiche zwischen verschiedenen Verpackungsarten anzustellen und ihre Fortschritte im Laufe der Zeit zu verfolgen. Als Ergänzung zum Greif Green Tool ermöglicht uns Greif Green Tool Lite, unseren Kunden schnell Informationen bereitzustellen. Das Greif Green Tool Lite bietet Kennzahlen zum CO2-Fußabdruck und zur CO2-Reduktion, die unsere Kunden durch die Umstellung auf ein nachhaltigeres Produkt erreichen können.
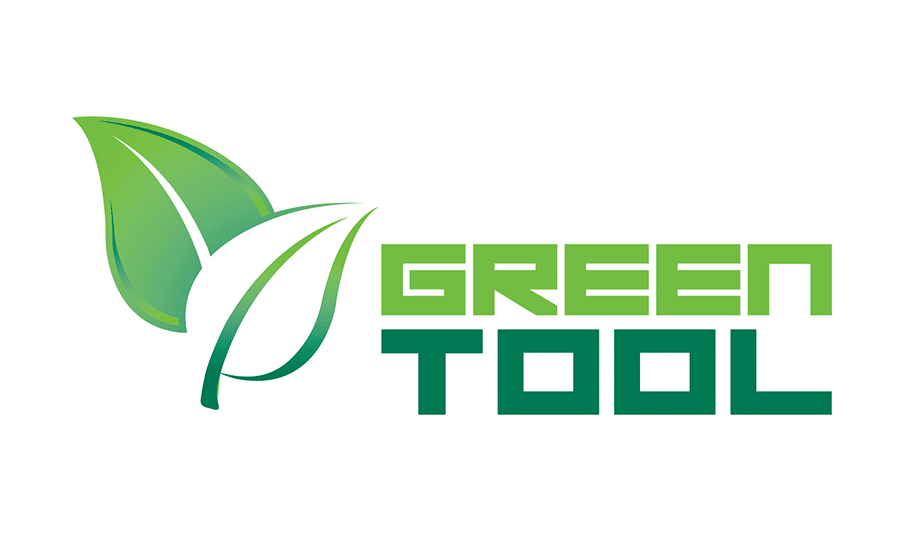
State of the Art Reconditioning Services in Lille
Greif’s LCS facility in Lille, France has taken significant steps to innovate the logistics associated with offering reconditioning services to our customers. Traditionally, empty IBCs were picked up from and delivered to a single location for a single customer. LCS Lille has begun picking up from locations along our customers supply chain, then delivering reconditioned IBCs back to our customers, simplifying logistics for our customers. Lille has also implemented Datamatrix, a traceability system that allows us to record all production steps from reception to delivery, have visibility into the origins of an IBC and provide a real time view of our inventory in support of overall enhanced customer service. Datamatrix also supports better management of residue in the IBCs they collect. Each IBC that enters the facility is automatically weighed to determine how much residue is in the container and inform how it is treated. With Datamatrix, this information can be sent directly back to customers to improve how they manage IBCs that are ready for pick-up. Lille uses a closed loop water system for water that is used to clean IBCs recycling 100 percent of the water they use, and collects, treats and shreds plastic that is used to manufacture new IBCs and plastic drums.
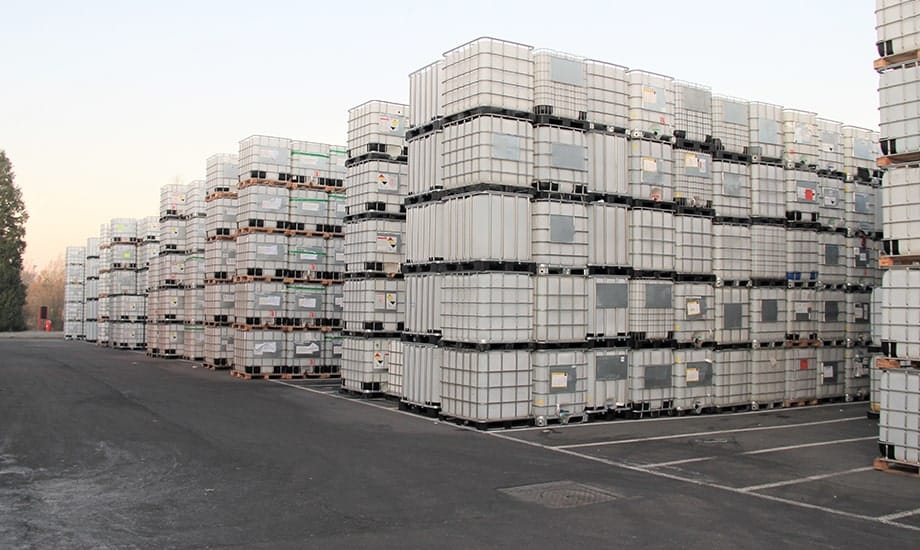
Providing Our Customers a Circular Solution
The CorrChoice GreenGuard® product line provides our customers with a food safe recyclable and repulpable alternative to supplemental materials, such as plastic liners. Our GreenGuard® line of paper coatings are safe for direct contact with most food types and feature oil, grease, water, moisture and abrasion resistance as well as an innovative wax replacement technology. By applying the coating to corrugated containers, we eliminate the need for supplemental materials used in many food applications. We work with our customers to ensure our products meet their needs for safe and secure food handling while providing packaging products that are 100% recyclable and repulpable, advancing our circular economy strategy while enabling our customers to meet their sustainability objectives.
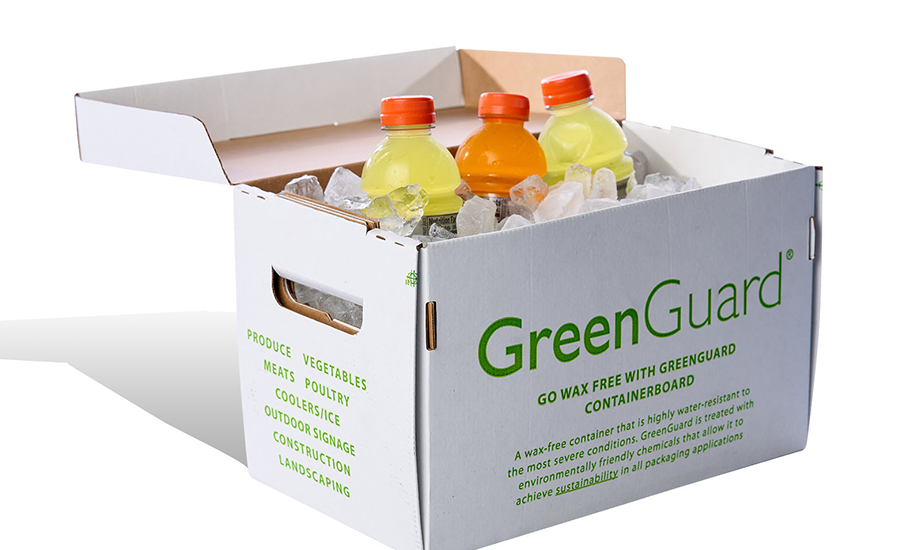
NACHHALTIGKEITS-HIGHLIGHTS
4.5 M
Containers Collected, Recycled and Reconditioned
Through our Life Cycle Services network, we collected, recycled and reconditioned steel drums, poly drums, IBCs and FIBCs.
94,991
Metric Tons of Virgin Materials Saved
Our recycling, reconditioning and reuse operations helped us remove over 94,991 metric tons of virgin steel, high-density polyethylene and wood from our supply chain in 2021.