- Sustainability at Greif
- Nachhaltigkeitsstrategien
- Ziele und Leistung
- ESG-Reporting-Indizes
- Bericht-Downloads
Highlights
- We are accelerating our delivery of legendary customer service through digital technologies and experiences, including the Greif+ digital platform.
- In 2024 we introduced our Business Modernization Program to assess our current operational landscape, identify opportunities and challenges, and develop strategies that better position the company to achieve its 2030 goals.
Why Automation & Digital Technology Matters
Our efforts to expand the use of advanced technologies, including automation, digital solutions, artificial intelligence (AI), and others globally, support our aim to be an employer, supplier, and customer of choice. Within our production operations we leverage these technologies to support our manufacturing processes to improve operational efficiency and safety while reducing costs and scrap without sacrificing product quality. We provide our customers and colleagues with enhanced digital experiences that support business value.
Our Approach
Our Global Operations Group (GOG) is responsible for the company’s Enterprise Automation Strategy, continuous improvement planning, environment, health and safety, quality and regulatory compliance, engineering and capital deployment, and operational execution. Through our Enterprise Automation Strategy development process we identified, classified, and prioritized common automation applications globally and across all our Strategic Business Units. The analysis evaluated the benefits from safety improvements, cost and risk reductions and efficiency and other operational improvements associated with automation opportunities. Following this approach we carefully consider and invest in plant modernization and automation initiatives that are customer driven, implementing these efforts in different waves to ensure that both existing and new technologies drive improvements in key business areas.
Automating Processes to Reduce Safety Hazards and Improve Operational Effectiveness
When manufacturing a steel drum, the top and bottom ends are attached to its body through a process known as seaming. Traditionally, this requires manual loading and alignment by a colleague. Personal protective equipment, proper training, and machine guarding help to protect the colleague from pinch points, ergonomic strain, and sharp edges but do not eliminate the potential hazards. At our Durable Metal Solutions facility in Bogotá, Colombia we installed an automated machine to feed parts, eliminating the need for manual loading. This automation enhances colleague safety, improves operational efficiency, and maintains consistent product quality.
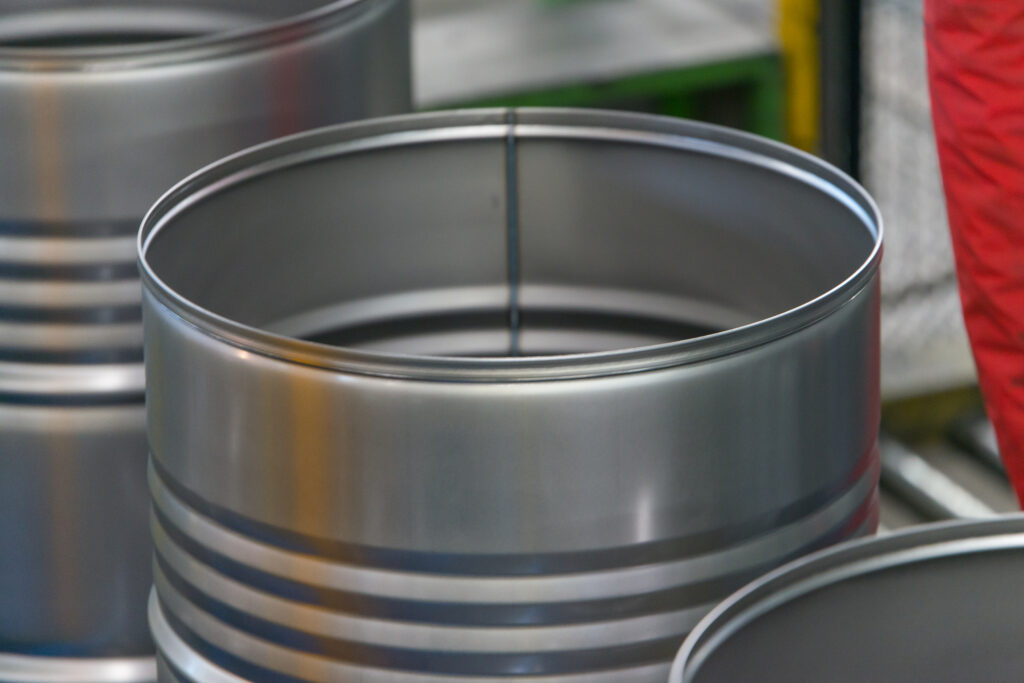
Through our Digital and Technology group, we work to empower our customers and colleagues with innovative digital solutions and experiences. By building on and expanding our digital capabilities, we are better able to connect processes, people, and data to create value. In 2024, Greif began a Business Modernization Program to prepare our operations and colleagues with the systems and processes to help achieve our long-term strategic priorities. Our Executive Leadership Team defined strategic tenants for Greif’s operating model and identified both opportunities and challenges that will arise along our journey. As part of the program, we are evaluating enterprise resource planning (ERP) systems to support not only our current operating model but the ERP critical to our future. The enhanced ERP system will provide improved traceability in the supply chain, greater access to data to optimize resource use, and new opportunities to support the achievement of our business goals.
Greif+ Legendary Customer Service at Customers’ Fingertips
We continue to expand the reach and features of Greif+, our customer digital portal. Offering 24/7 availability for all our customers in North America, Greif+ enables customers to submit, modify, and track orders. Through the platform customers also gain access to valuable, detailed information about our products and services, including being able to view and select more sustainable solutions. The online platform also allows us to work directly with customer service on issues. With expanded accessibility and capabilities, this advanced digital platform drives operational efficiency while providing a much-improved experience for our customers.
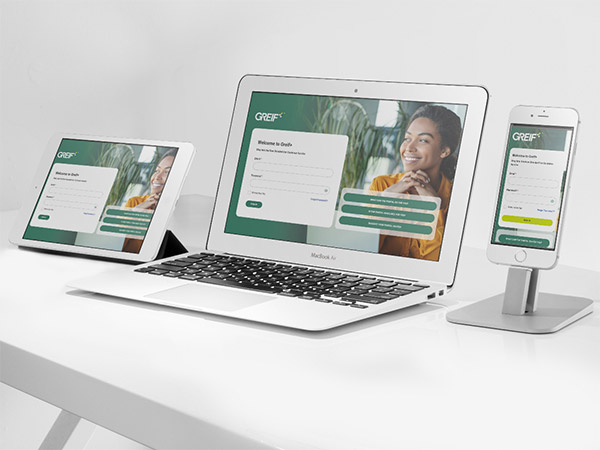
In September 2023, we published our Generative Artificial Intelligence Use at Work Policy to establish guidelines for the appropriate and responsible use of generative AI tools at Greif and to highlight common risks encountered when using generative AI. We use this policy to inform responsible use of generative AI as we test, pilot, and incorporate this technology into our tools and processes to provide legendary customer service.
Goals, Progress, & Performance
Across our operations and ways of working we are leveraging advanced technologies to support our Company’s growth objectives. We measure the success of this work on a project-by-project basis, setting clear key performance indicators relevant to the project. We consider efficiency improvements, impact on colleagues, impact on customers, and other factors as appropriate.