أبرز الأحداث
- Following the One Greif approach, in 2024 we completed the development of a unified approach that brings together regulatory monitoring and compliance management into one platform.
- At Greif, we use our EMS program to support compliance with relevant environmental regulations across all our operations. We strive for zero instances of non-compliance across all operations.
- Adapting to a constantly evolving regulatory landscape is critical to maintaining business continuity and we provide colleagues with training materials that cover current laws and regulations.
لماذا تعتبر أنظمة الإدارة البيئية مهمة؟
A comprehensive approach to EMS is essential to accomplishing the Protecting Our Future mission under our Build to Last Strategy. As we evolve towards a low-carbon future through improved energy efficiency, raw material minimization, circular practices, and renewable energy, ensuring our operations comply with environmental regulations is critical. EMS is also a pivotal resource for Greif in mitigating and managing environmental impacts, such as emissions related to manufacturing processes. Through our Global Regulatory Steering Committee, we monitor the environmental regulatory landscape to proactively identify and address sources of environmental compliance risks.
Our Approach
As set out in our Environmental, Health and Safety (EHS) Policy, we implement a comprehensive set of policies, technologies, training programs, audits, and other initiatives to establish a consistent, repeatable, and risk-mitigating approach to managing environmental compliance and impacts. This structured framework forms our EMS.
Advanced EMS technology creates opportunities for improved environmental performance across Greif’s business. Data management is a strategic focus area as we expand its implementation, helping provide key insights for our EMS specialists to make further environmental progress. Looking ahead, we plan to utilize our technological resources to expand the coverage of environmental certifications, including ISO 14001, across our global facilities on our journey to achieving a standardized EMS for all our operations.
شهادات الطرف الثالث الخاصة بنا
Our production facilities manage quality, safety, and environmental standards through certifications such as OHSAS, ISO, FSSC, and SQF. Our Sustainable Fiber Solutions operations maintain ABI, FSC, OSHA, PEFC®, إس إف آي®, RPA 100 and RPTA FDA certifications. All our CorrChoice facilities and mills have SFI® Chain of Custody Certification, and all our mills are certified to FSC® (FSC®C003539), PEFC® Chain of Custody, and RPA100. Throughout our operations, 19 sites have achieved ISO 14001 certification, and we have ISO 50001 certification at 4 sites. Please visit our 2025 Certificates document to learn more about our facility certifications. We continuously work to increase the number of facilities and processes certified to external standards, leading to improved compliance.
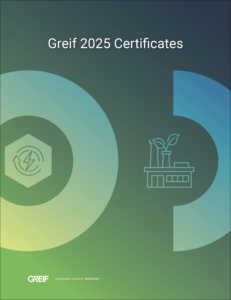
In 2024, we advanced our EMS by transitioning to a unified platform bringing together regulatory monitoring and compliance management activities. Following a One Greif philosophy, we are leveraging this platform to connect these activities that were previously siloed. Across Greif, we are positioning our facilities for compliance with existing and emerging environmental regulatory requirements.
EHS compliance is a core focus of our EMS and in 2024, we established a new role for EHS leadership in North America. With a dedicated senior leader for all EHS matters, we have seen significant growth in terms of EHS compliance and performance across the region. For example, negative 360 Watch findings from EcoVadis have significantly declined from 2023 to 2024. Following the early success of this expansion, we have ambitions to continue to grow our EHS leadership team across the other regions where we operate. For more details on EHS please visit the Health and Safety section of our report.
With a strong EMS, Greif implements a structured framework to maintain and monitor the effectiveness of our pollution control devices, such as Regenerative Thermal Oxidizers (RTOs). In addition to regular, preventative maintenance, we implement a leak detection and repair program, continuous monitoring, internal and third-party inspections, and other activities.
We conduct audits at facilities to assess operations for risks of non-compliance or other environmental impacts. Members of the global EHS team conduct in-person assessments at facilities depending on current needs and projects. Additionally, 100 percent of facilities are analyzed annually via a desktop audit for risks of environmental non-compliance. Depending on the level of risk from the assessment, on-site audits are then conducted by the team to confirm alignment with legal requirements. We aim to conduct an audit at each facility every 5 years on a rolling basis to identify compliance gaps or blind spots so we can take corrective actions to eliminate them. In FY2024, we conducted 16 audits.
Goals, Progress, & Performance
Greif is committed to maintaining a zero-tolerance approach to non-compliance. When we identify instances of non-compliance, we swiftly address and rectify the situation. Greif has adopted a system that regularly scans for local, regional, and federal regulations to evaluate applicability to our operations. This has improved our ability to manage compliance relating to ongoing and upcoming regulations.
- In 2024 we introduced a unified digital platform for Greif’s EMS, a significant step in achieving a uniform system in accordance with the One Greif approach.
- Greif expanded EHS leadership support within its North America operations, which has been a key factor in improving widespread environmental compliance and performance while preparing for global expansion in the future.
المؤكسدات الحرارية المتجددة
في عام 2022، نفذت شركة Greif برنامج صيانة لتعزيز طول عمر مؤكسداتنا الحرارية المتجددة (RTOs) التي تتحكم في انبعاثات الكربون العضوي المتطاير (VOC) في 10 من مواقع GIPNA الخاصة بنا في جميع أنحاء أمريكا الشمالية. واستمرارًا لتحولنا إلى نظام إدارة مدفوع من قبل الشركة، نعمل مع شريك تابع لجهة خارجية لإدارة الأجهزة التي تم تنفيذها مؤخرًا. يساعدنا شركاؤنا الخارجيون في ضمان صيانة مؤكسداتنا الحرارية المتجددة بما يتوافق مع جميع اللوائح ذات الصلة وتجنب أو حل أي مشكلات متعلقة بالصيانة. نجري تقييمات صيانة ربع سنوية ونصف سنوية وسنوية ونتتبع هذا البرنامج داخل نظام إدارة المحتوى الخاص بنا. نستمر في تثبيت مؤكسدات حرارية متجددة جديدة في منشآتنا ونتوقع الاستفادة من البرنامج في جميع المرافق المعمول بها، مما يؤدي إلى تحسين الكفاءة وتقليل الانبعاثات.
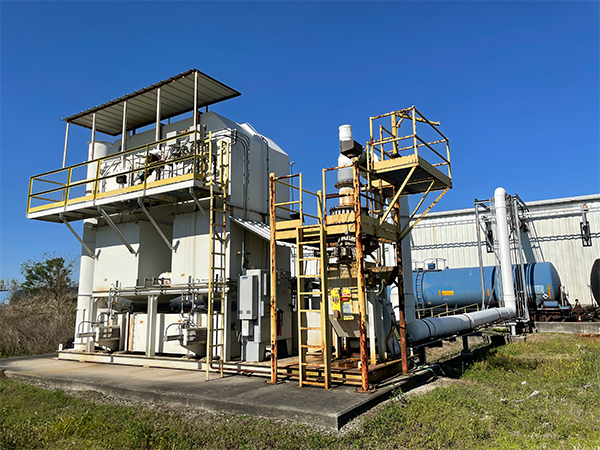